Neil Lickfold
Member
- Joined
- Mar 10, 2025
- Messages
- 7
I made a spacer plate from what was supposed to be 10mm acrylic sheet. What arrived was actually 9.3mm thick.
So to attach the spacer, did this.
The 2 pins on the plate were marked with a 5.9mm drill in the inner corner of the rectangular holes. Drilled with a 6mm drill.
2 plastic pins were then pushed into the holes to protrude no more than 3.5mm.
To drill the hole for the front pin, was marked out based on a 5.8mm pin in place. A 4mm hole was drilled through, and opened up with a
6mm step drill. As the front little recess is slightly tapered, the idea was if it was loose, could tighten it by pushing the pin through a little more.
It is a light clip fit to the base and stays very centred.
Marked a centre line on the bottom to match that of the centreline of the plastic plate. Did read the instructions about aligning that plastic insert plate
test to get it all working as it should be.
As there is a gap of 9mm or so between the lines, when aligning up against the 18mm ply, it works very well. In a piece over 600mm long and lining up the marks,
the slots can all be done on the narrow setting and they all go together. (6X40 domino's with a homemade extension for the 6mm DF500 cutter). Also did some other 8mm tenons but they were from the outside , going into the 18mm ply 50mm deep.
Since the plate was not the nice 10mm I wanted, then set to, and made my own depth stop gauge. Not as fancy as the original or the 3d print copies, but works well.
It has a 5 steps in the block that make the centreline from 9.15mm +, 9.0mm 0, 8.9mm -, 8.8mm =(double minus) for the lower 2 settings. This will become my 18mm plywood depth stop block. I plan on making the blocks to suite the various plywoods etc that are sold out here.
This tuneable stop is primarily made to adjust the flat side position centre line thickness to match that of when a slot is cut near an edge of the board and the end result to be flush. Like when they match at 90 degree and wanting the corners to be flush to each other.
There maybe a much better way to put the 14mm deep 6mm wide slots in the edge of the plywood that what I have done, and if so, would be keen to learn more.
Here are the pics of the 2 pieces for the pivot base and the space for the fixed base.
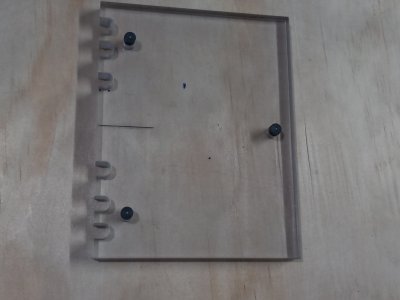
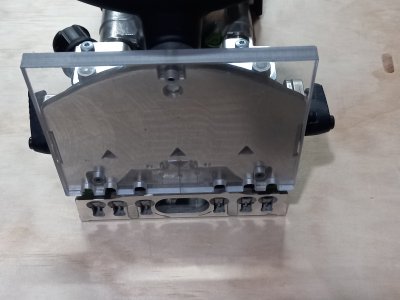
Step block
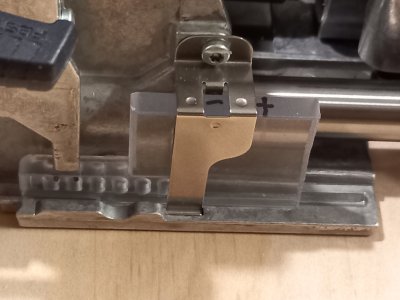
Bottom plate spacer for edge holes.

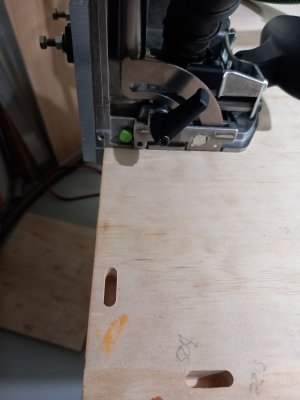
Neil
So to attach the spacer, did this.
The 2 pins on the plate were marked with a 5.9mm drill in the inner corner of the rectangular holes. Drilled with a 6mm drill.
2 plastic pins were then pushed into the holes to protrude no more than 3.5mm.
To drill the hole for the front pin, was marked out based on a 5.8mm pin in place. A 4mm hole was drilled through, and opened up with a
6mm step drill. As the front little recess is slightly tapered, the idea was if it was loose, could tighten it by pushing the pin through a little more.
It is a light clip fit to the base and stays very centred.
Marked a centre line on the bottom to match that of the centreline of the plastic plate. Did read the instructions about aligning that plastic insert plate
test to get it all working as it should be.
As there is a gap of 9mm or so between the lines, when aligning up against the 18mm ply, it works very well. In a piece over 600mm long and lining up the marks,
the slots can all be done on the narrow setting and they all go together. (6X40 domino's with a homemade extension for the 6mm DF500 cutter). Also did some other 8mm tenons but they were from the outside , going into the 18mm ply 50mm deep.
Since the plate was not the nice 10mm I wanted, then set to, and made my own depth stop gauge. Not as fancy as the original or the 3d print copies, but works well.
It has a 5 steps in the block that make the centreline from 9.15mm +, 9.0mm 0, 8.9mm -, 8.8mm =(double minus) for the lower 2 settings. This will become my 18mm plywood depth stop block. I plan on making the blocks to suite the various plywoods etc that are sold out here.
This tuneable stop is primarily made to adjust the flat side position centre line thickness to match that of when a slot is cut near an edge of the board and the end result to be flush. Like when they match at 90 degree and wanting the corners to be flush to each other.
There maybe a much better way to put the 14mm deep 6mm wide slots in the edge of the plywood that what I have done, and if so, would be keen to learn more.
Here are the pics of the 2 pieces for the pivot base and the space for the fixed base.
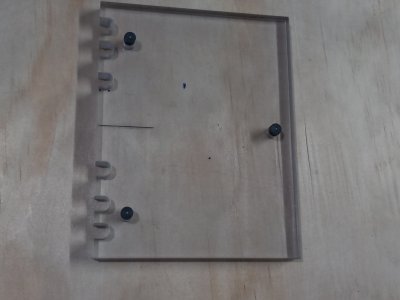
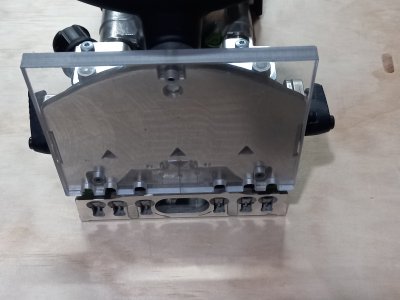
Step block
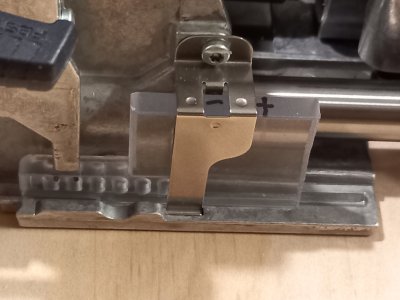
Bottom plate spacer for edge holes.

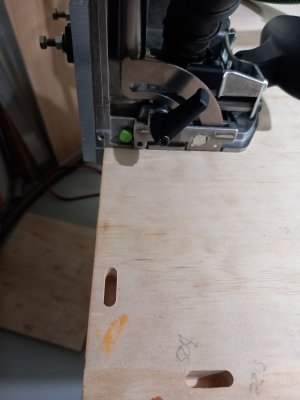
Neil