Hi all, haven't done a WIP in ages so I started a project today so here goes. Its a simple side unit for storage with a 50mm radius on the sides. Other than the radius it is a fairly straight forward build. The body will be oak with the back and shelves made from oak veneered MDF. The top and feet will be made from ABW.
The design: The blue bits will be ABW.
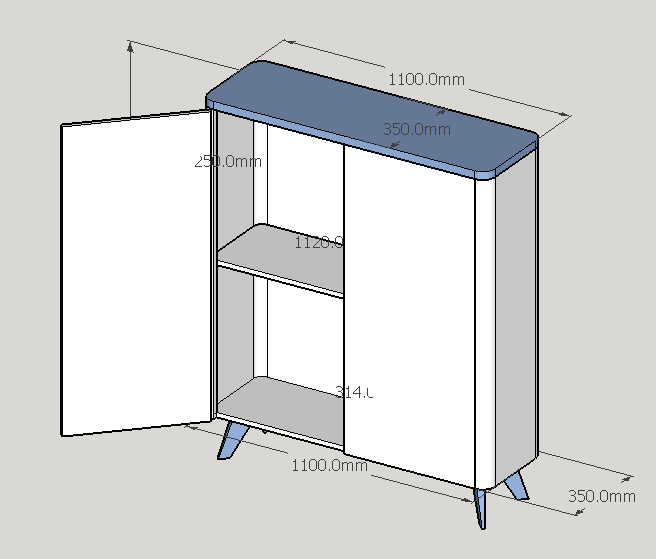
Starting at the bottom, here are the feet:
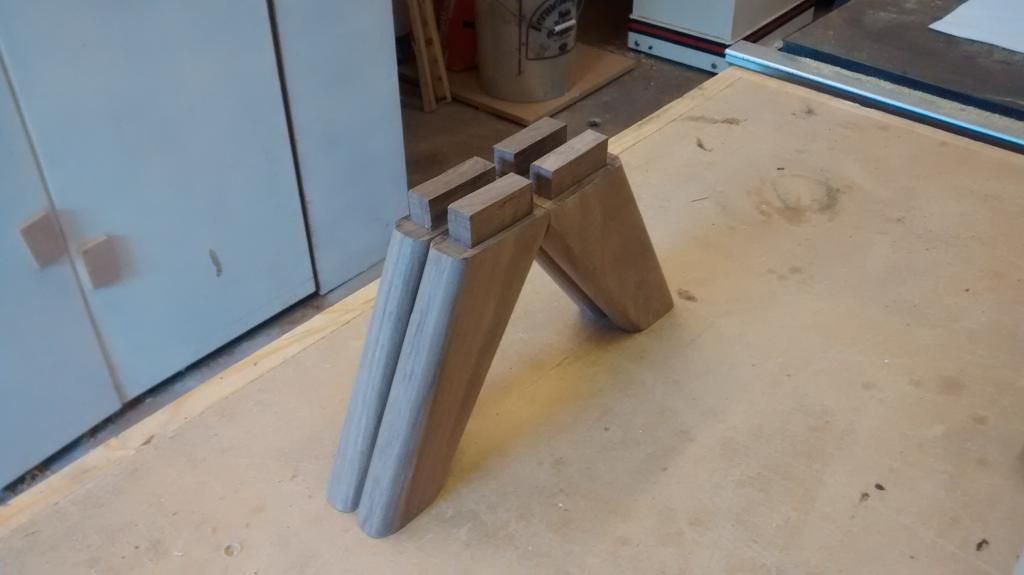
For the curves I'm using a 100mm x 100mm piece which will be rounded and then quartered.
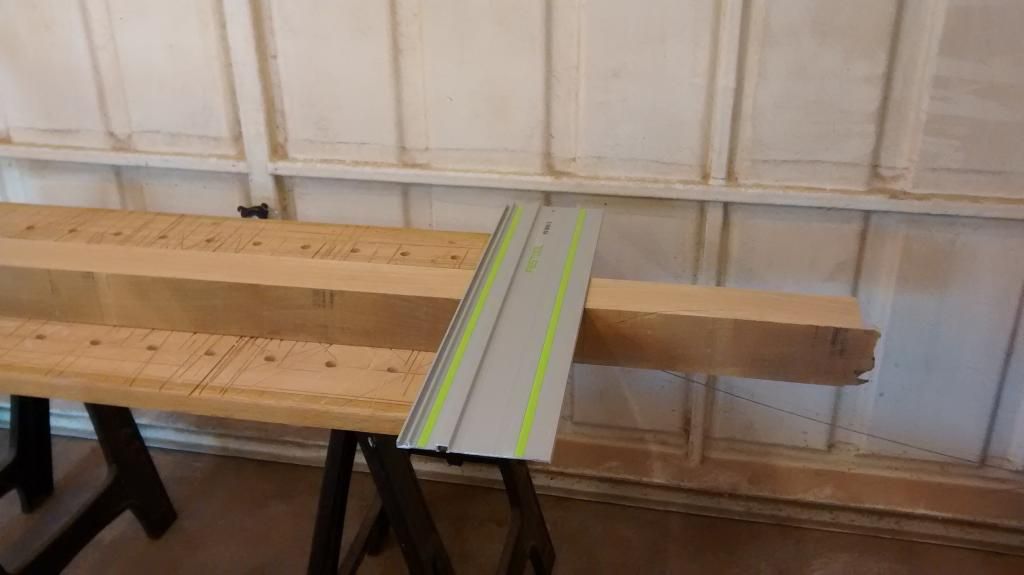
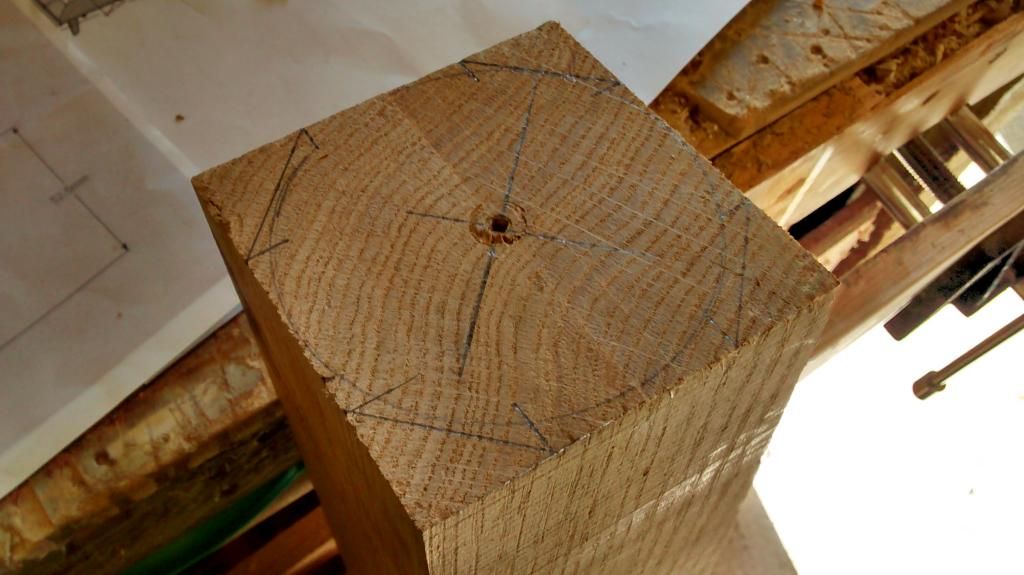
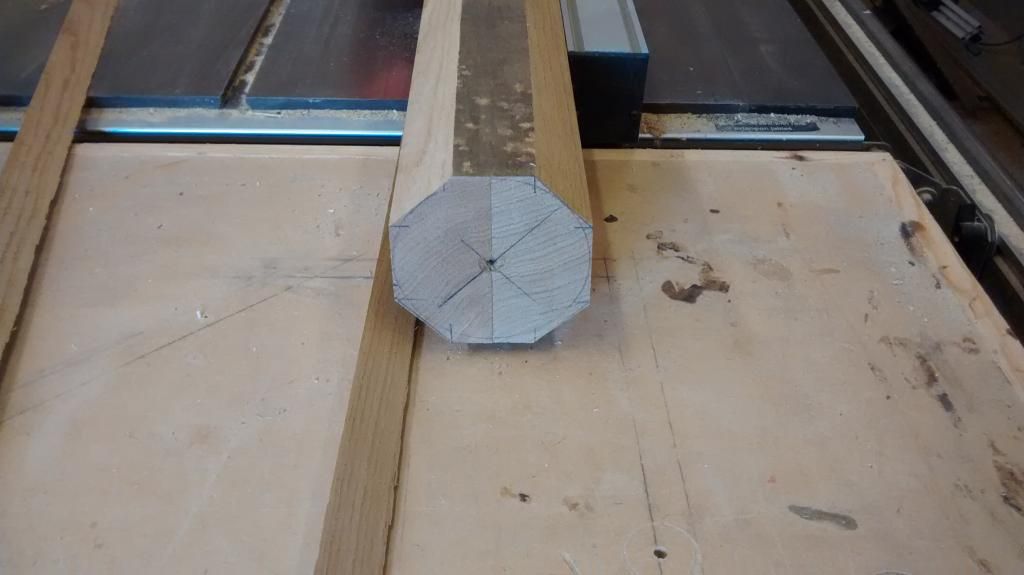
As I don't have a lathe I used a router jig to make the cylinder:
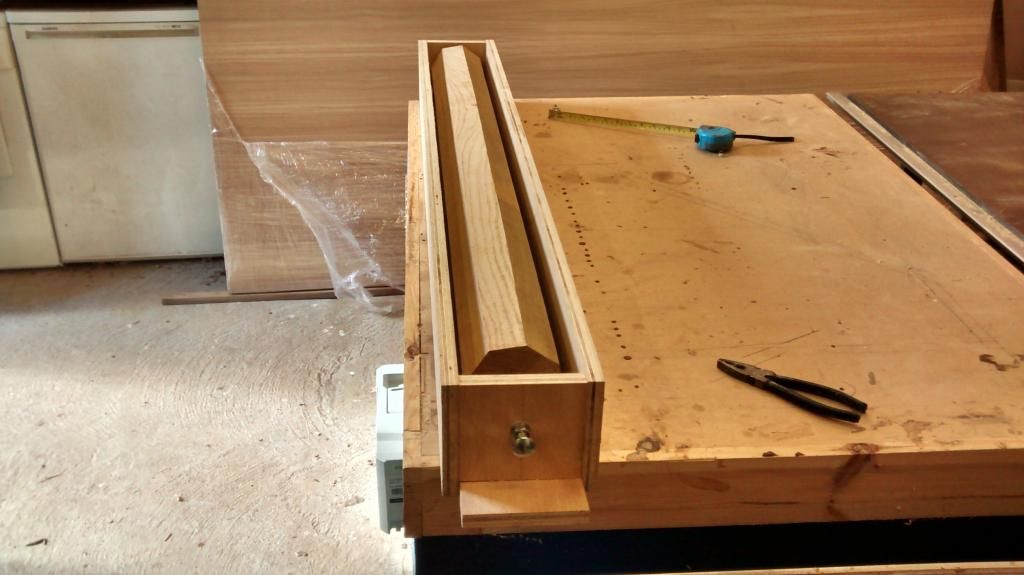
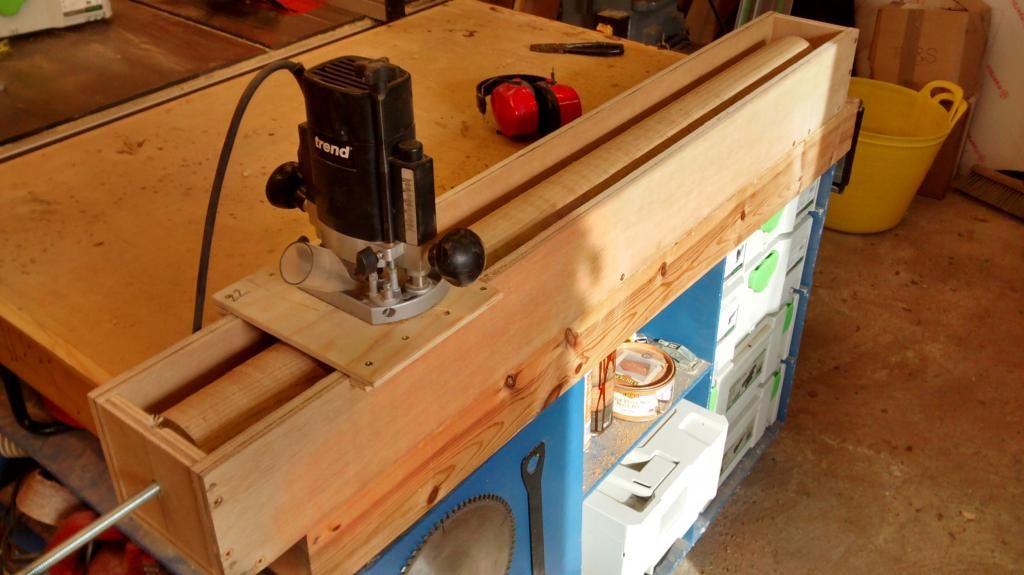
Good video of the jig here:
I then used the Rotex to smooth it out, just keep it moving to avoid flatting the cylinder and ended up with:
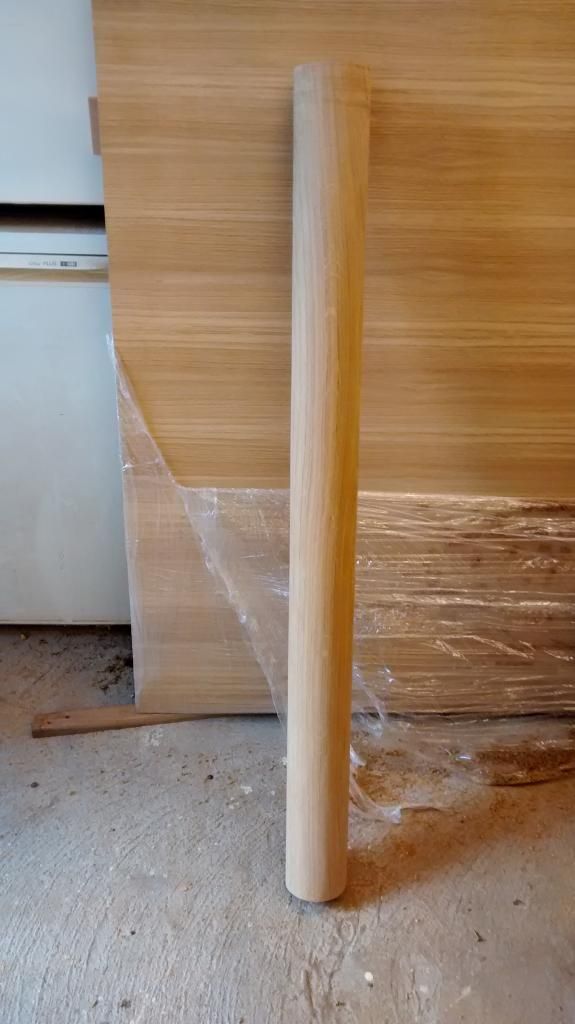
I then fixed on some end blocks and quartered the cylinder into quadrants with the TS:
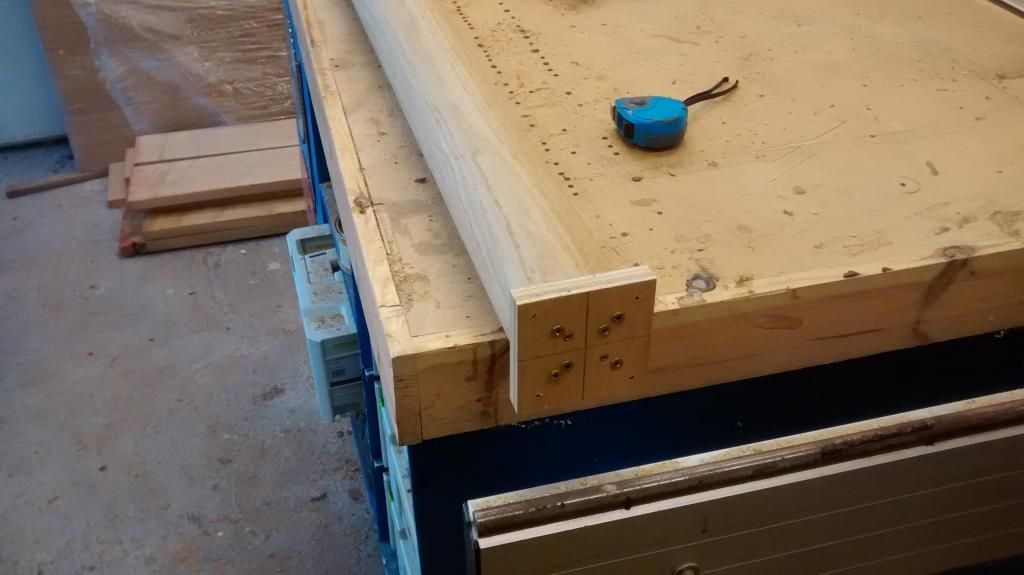
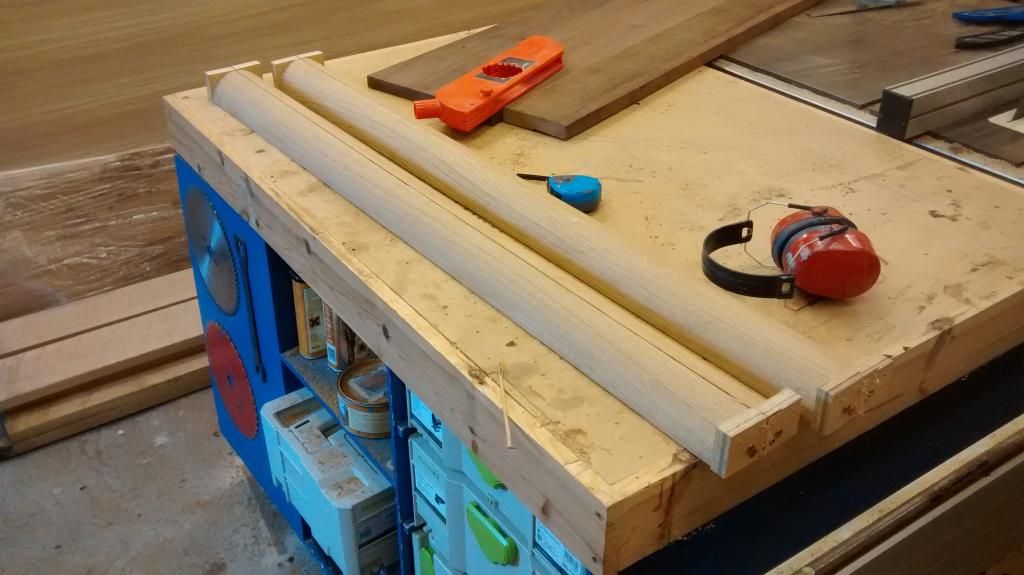
And that was as far as I got in 3-4 hours this afternoon. Tomorrow I'm hoping to get the base of the unit made and the sides and back on. The only really tricky bit is truing up the quadrants on the planer (jointer for americans) to ensure the corners of the unit do end up as 90. I've got the most beautiful pieces of ABW for the top and am really looking forward to getting it finished and seeing the oil go on! Here it is from a few days ago. I've since ripped off one of the boards as its a little lighter than the other two. I'll replace it with a new darker one I've had delivered.
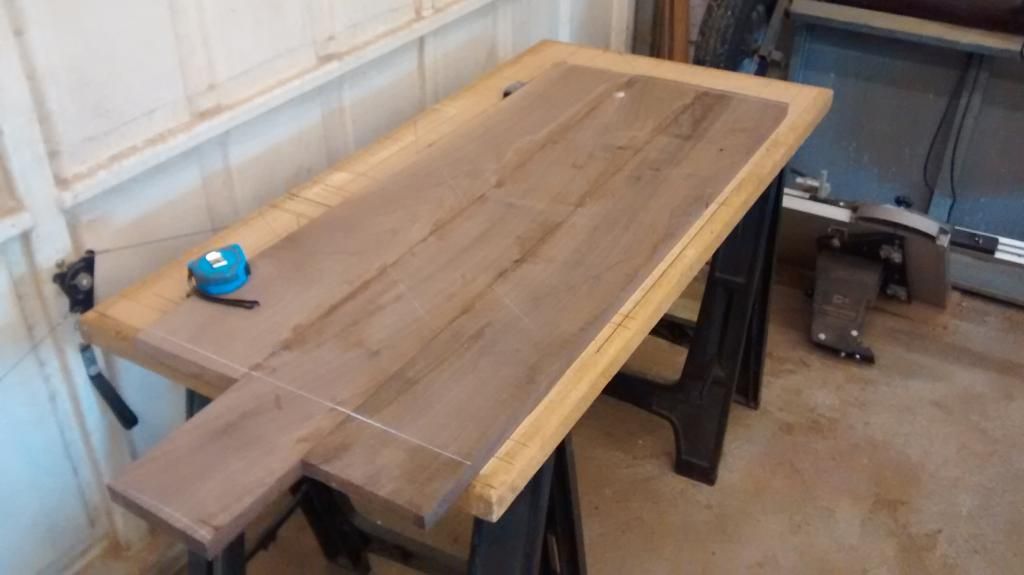
The design: The blue bits will be ABW.
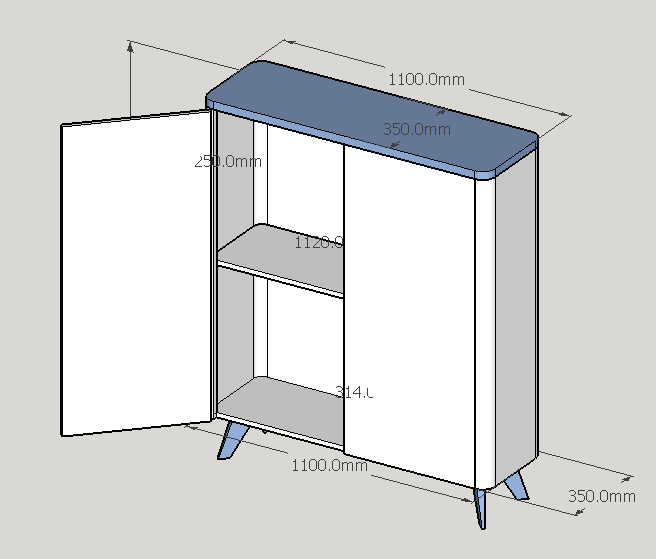
Starting at the bottom, here are the feet:
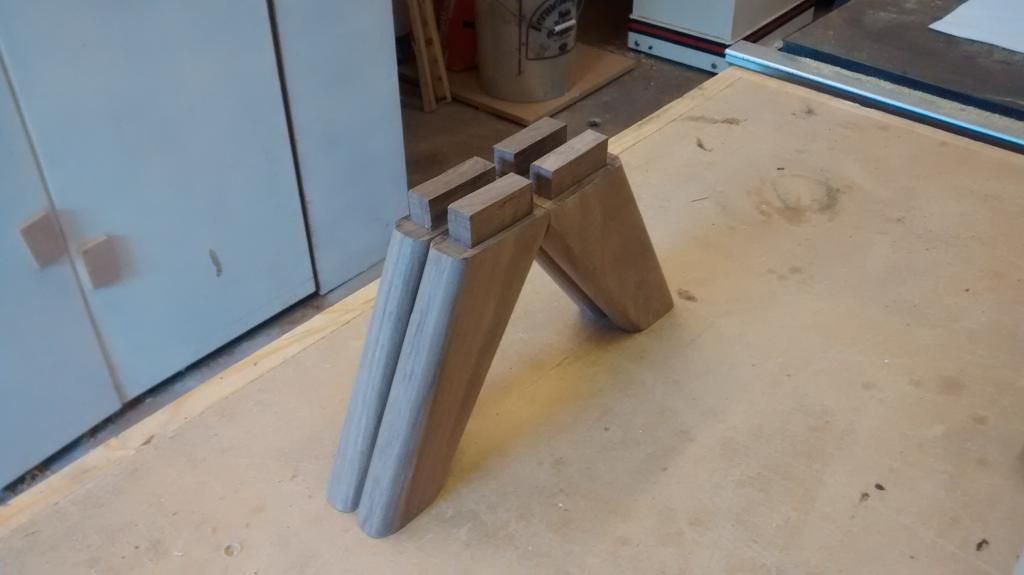
For the curves I'm using a 100mm x 100mm piece which will be rounded and then quartered.
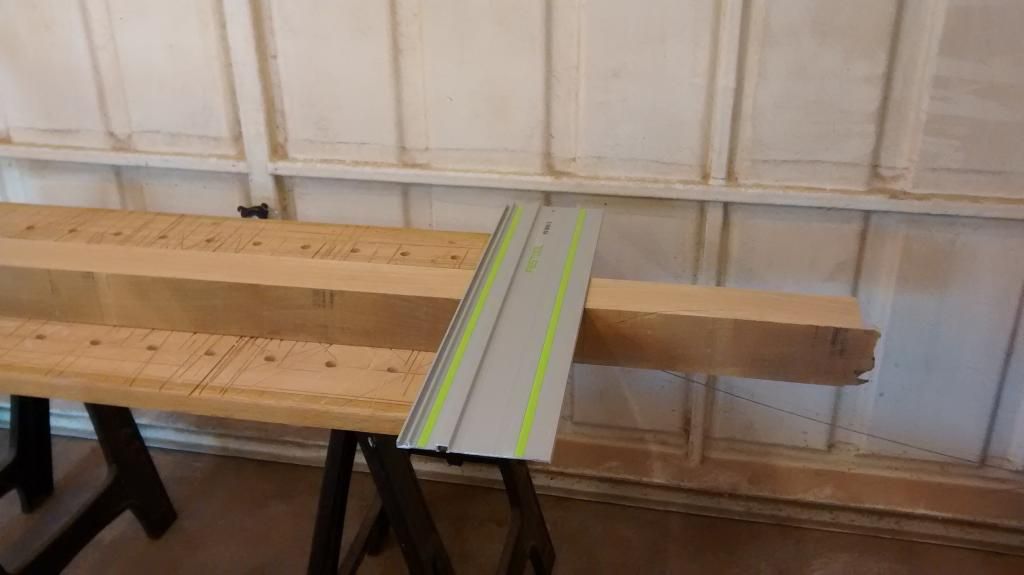
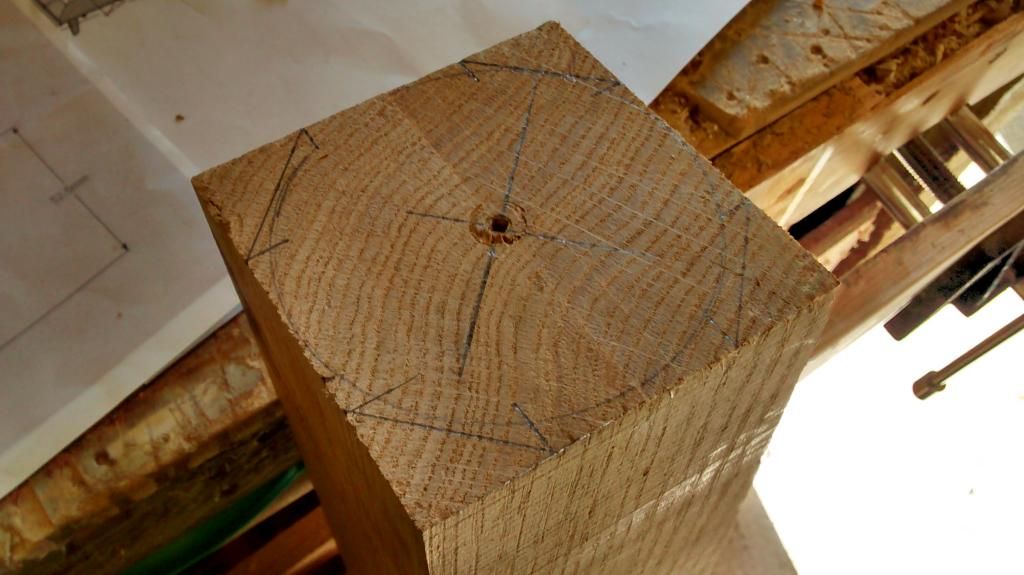
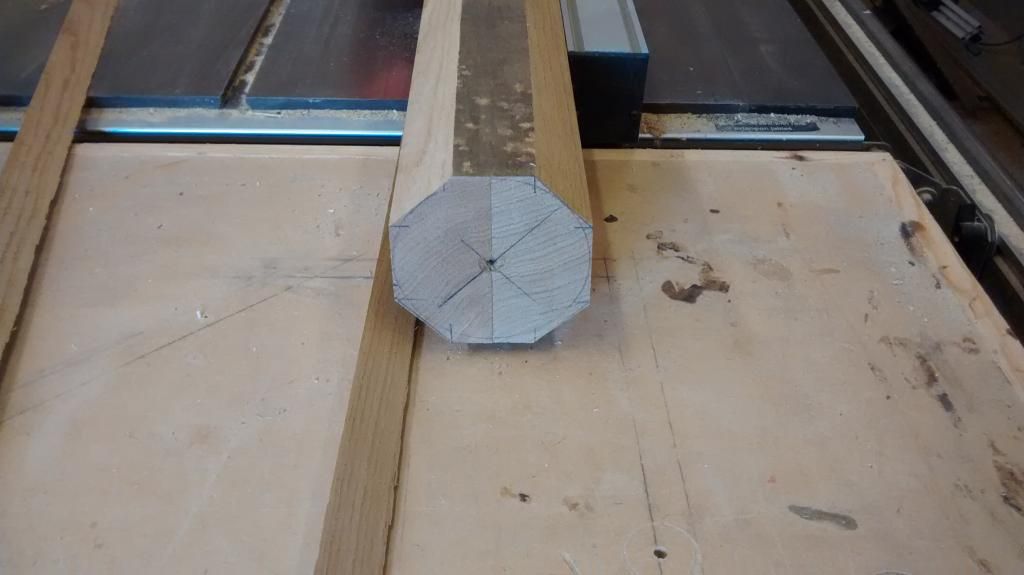
As I don't have a lathe I used a router jig to make the cylinder:
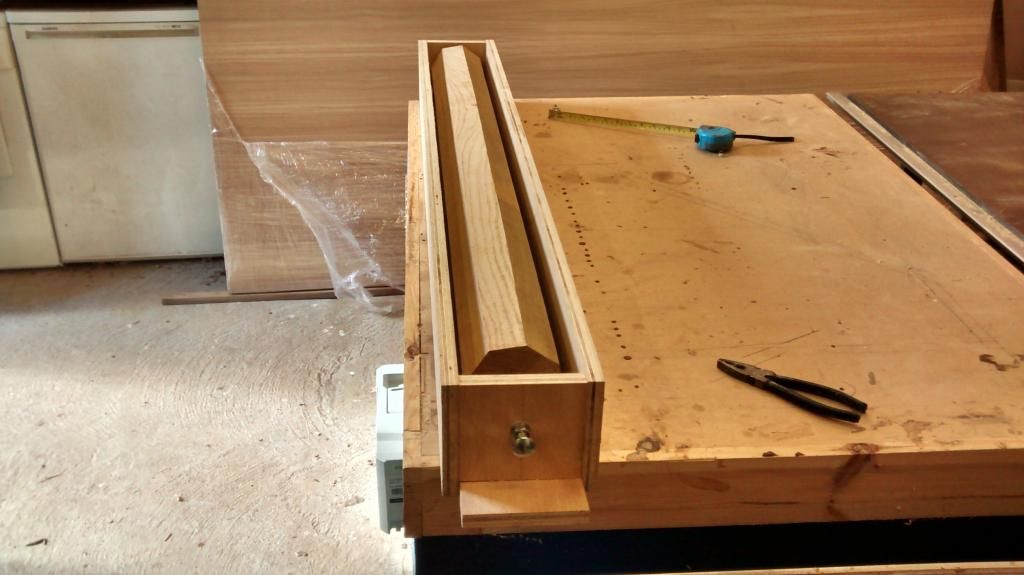
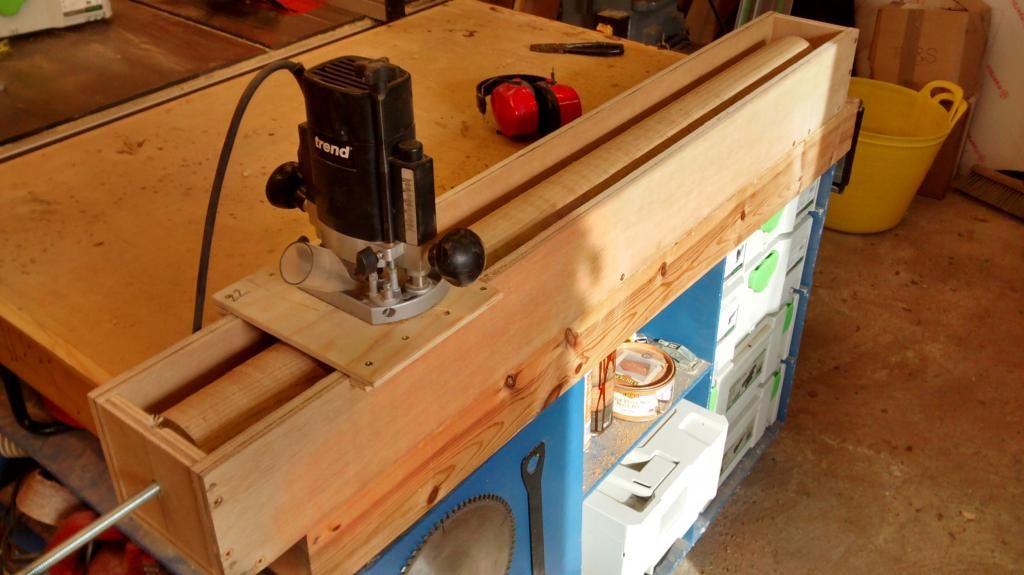
Good video of the jig here:
I then used the Rotex to smooth it out, just keep it moving to avoid flatting the cylinder and ended up with:
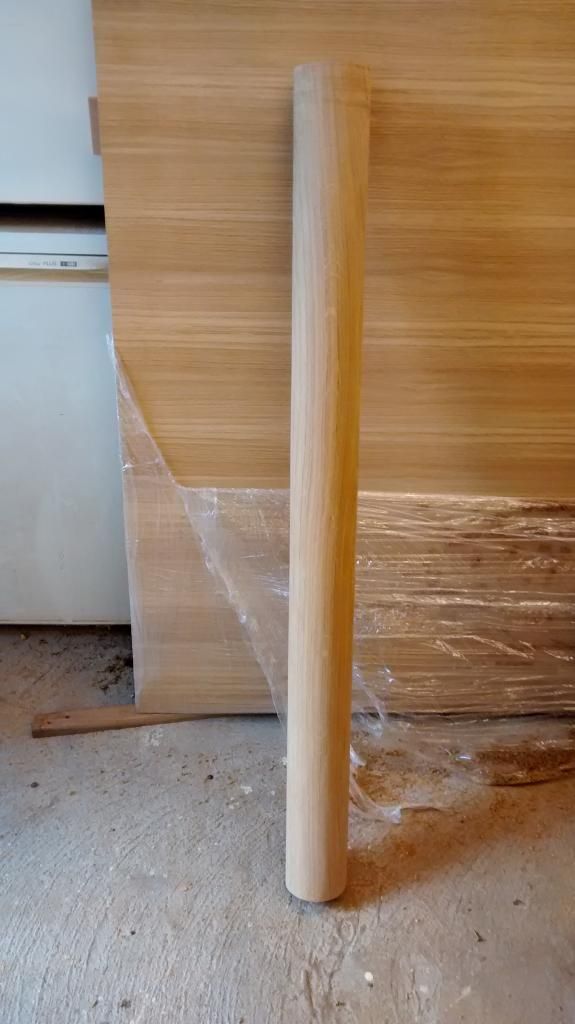
I then fixed on some end blocks and quartered the cylinder into quadrants with the TS:
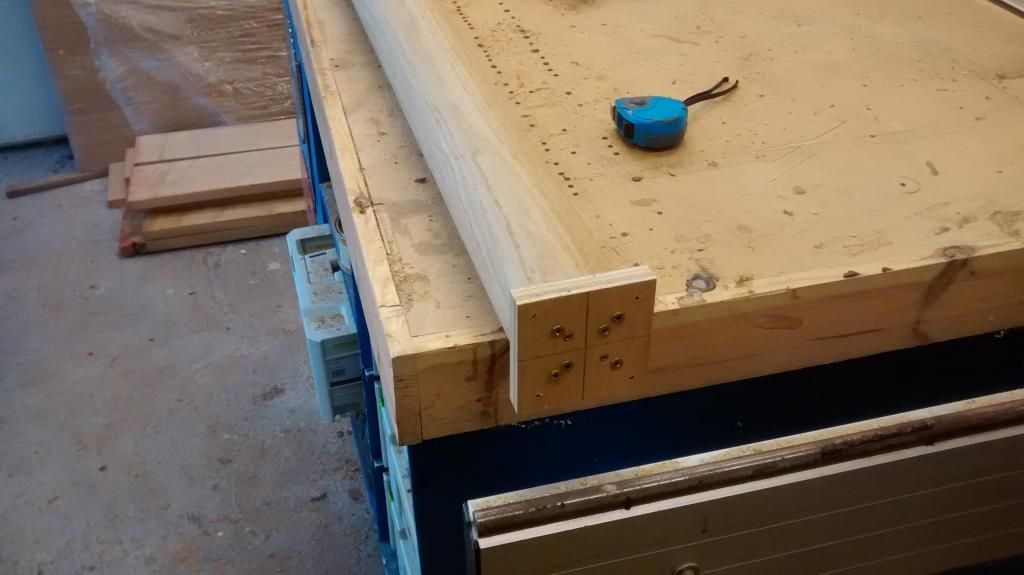
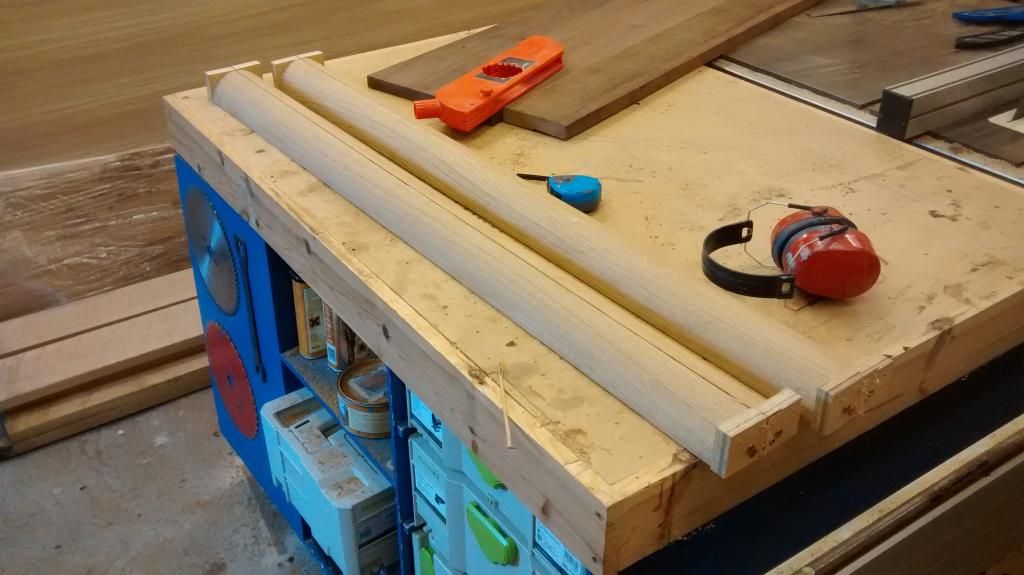
And that was as far as I got in 3-4 hours this afternoon. Tomorrow I'm hoping to get the base of the unit made and the sides and back on. The only really tricky bit is truing up the quadrants on the planer (jointer for americans) to ensure the corners of the unit do end up as 90. I've got the most beautiful pieces of ABW for the top and am really looking forward to getting it finished and seeing the oil go on! Here it is from a few days ago. I've since ripped off one of the boards as its a little lighter than the other two. I'll replace it with a new darker one I've had delivered.
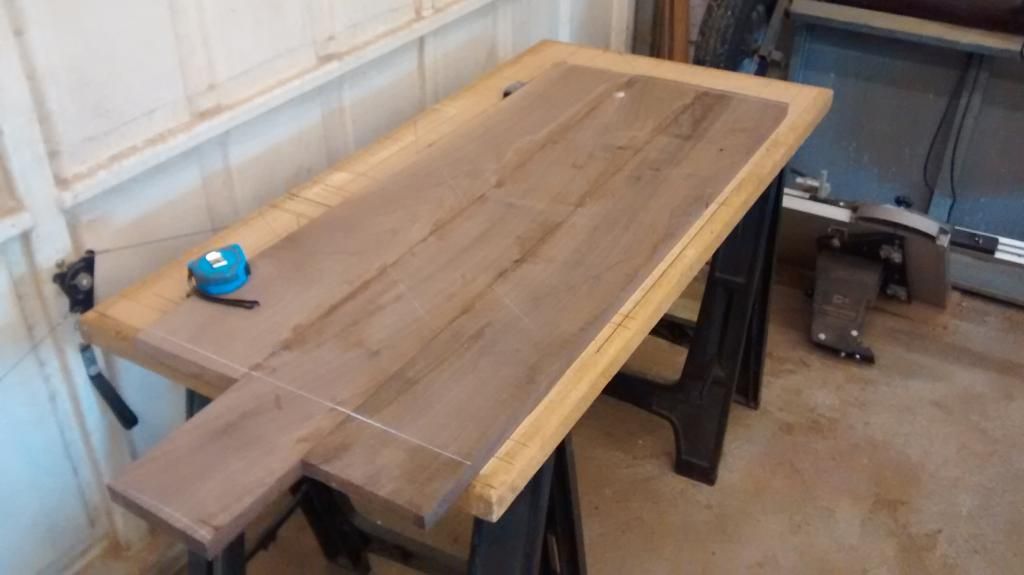