Recently finished this off, its Festool at heart with domino been the tool of choice. Un-fortunately I don't have any more festool, but I will be buying more, this was my first and I got it in America cheap whilst on holiday at Christmas. I'm early on in my woodworking so all my tools are cheap first tools but as I replace them they will all be replaced by Festools. Next is a vac and the TS55 or TS75.
Lot of pictures enjoy!
The american ash I picked up was lovely and straight from the start so I just thicknessed it and only needed to cut two boards down to get them through.
?98 for the lot.
Started off with making the end panels.
Changed the cutter in the domino, its so easy it sort of screws onto a screw not like a router at all.
With the larger cutter in it actually seems to be more smooth almost. I guess like using an 8mm shank over a 1/4 inch.
The glued up 4 parts to do make the panels for the frames, wished I had a bandsaw at this point, could have book matched them as the stock was very thick.
I want it finished by next Wednesday, not including the weekend as I probably won't touch it over then. I do so wish I had a drum sander thou
I left it this evening having done all the rebates and the 2 end panels in clamps, the nice thing about the panels been made from 2 pieces is it shouldn't need any cleaning up I'm hoping.
Target for tomorrow, completed frame, bottom shelf and uprights, ready then for top, door and drawer next week.
Lot of pictures enjoy!
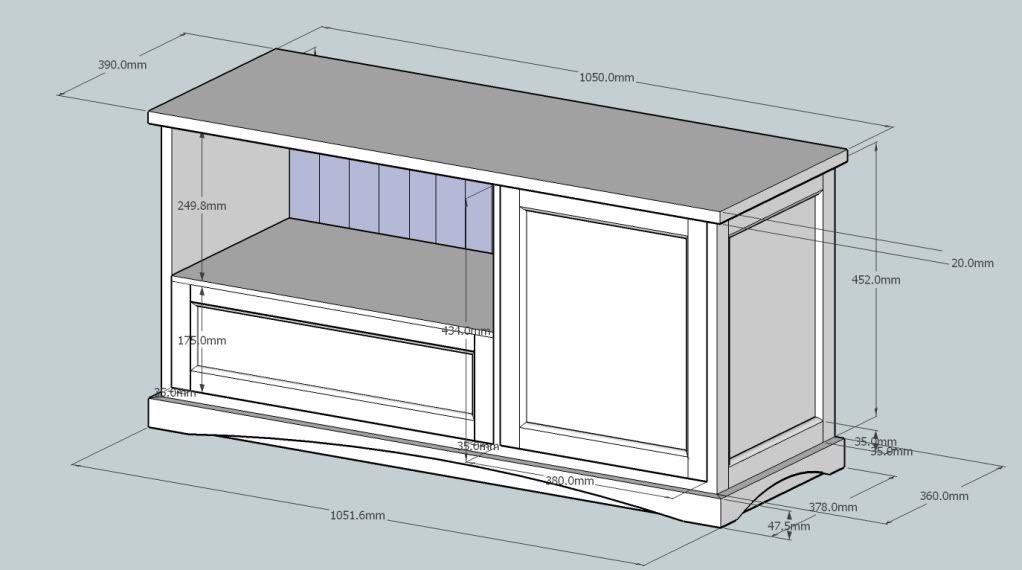
The american ash I picked up was lovely and straight from the start so I just thicknessed it and only needed to cut two boards down to get them through.
?98 for the lot.
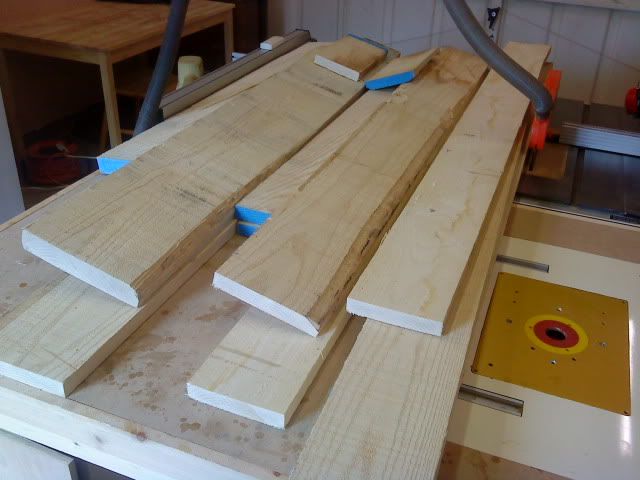
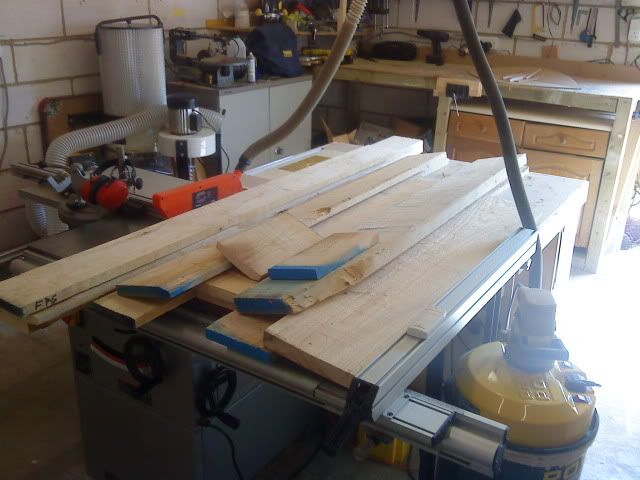
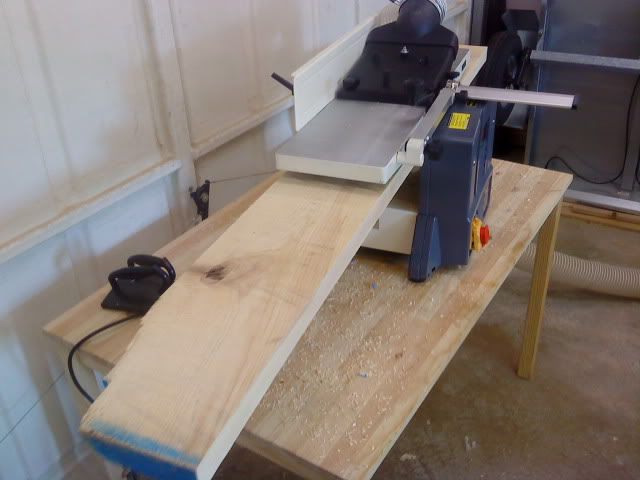
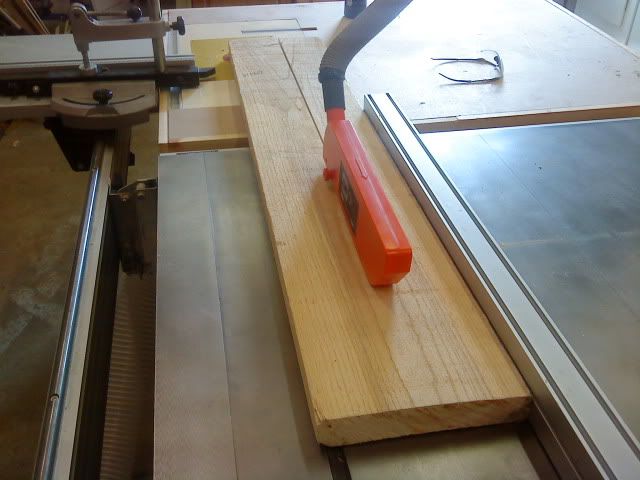
Started off with making the end panels.
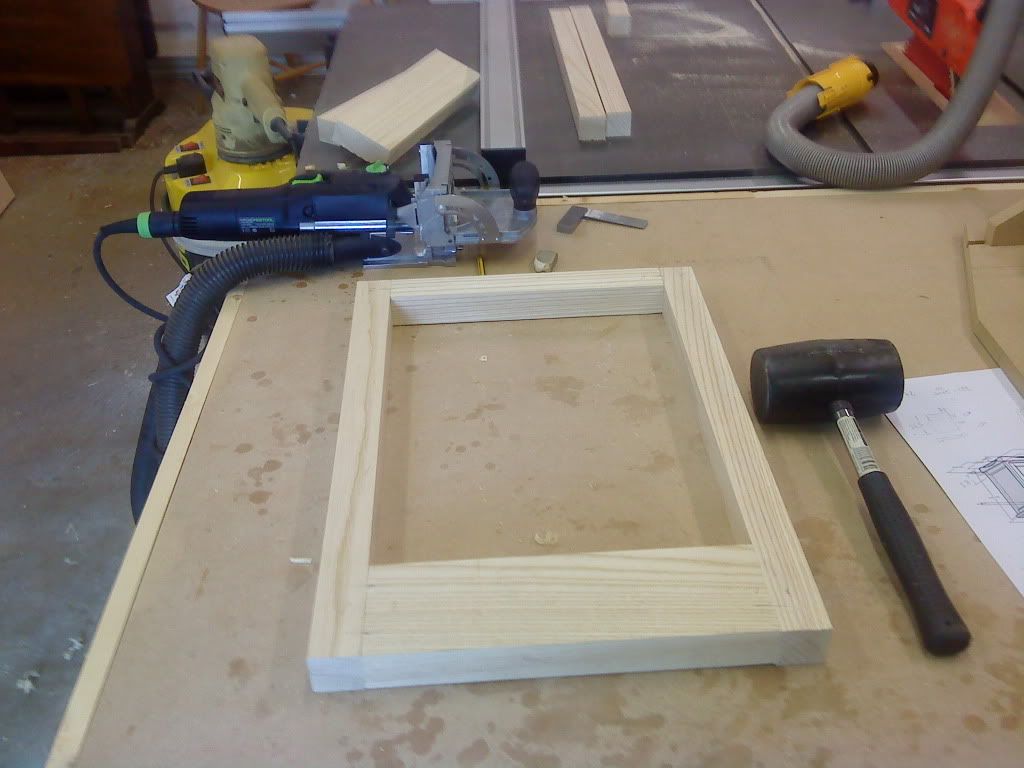
Changed the cutter in the domino, its so easy it sort of screws onto a screw not like a router at all.
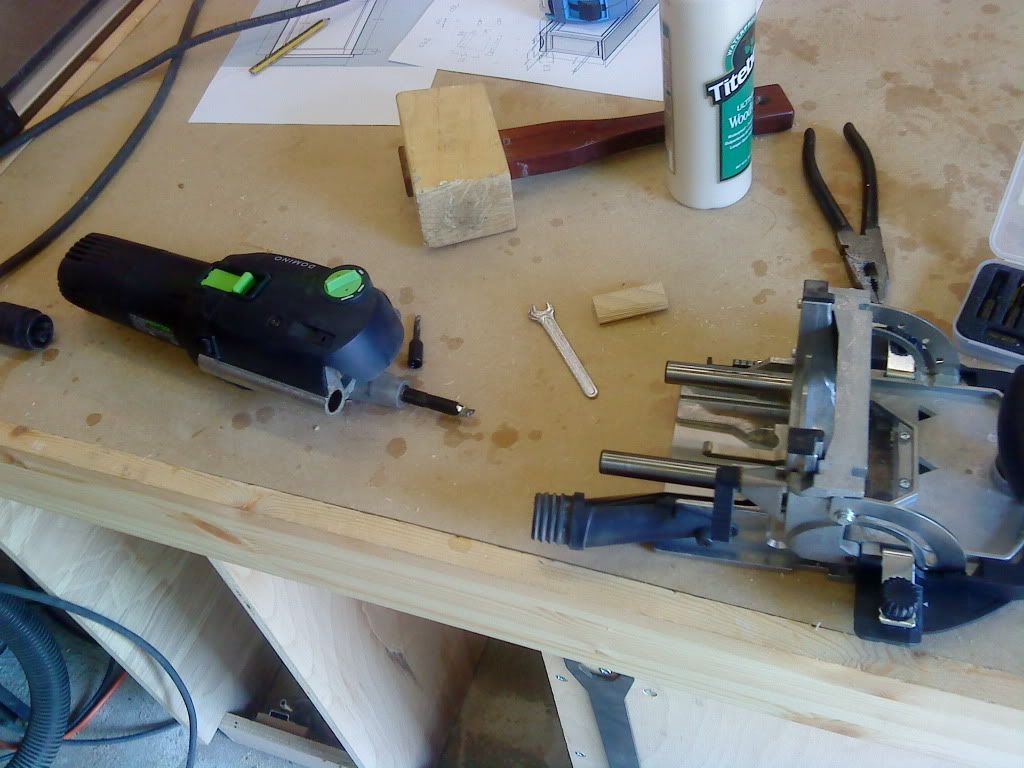
With the larger cutter in it actually seems to be more smooth almost. I guess like using an 8mm shank over a 1/4 inch.
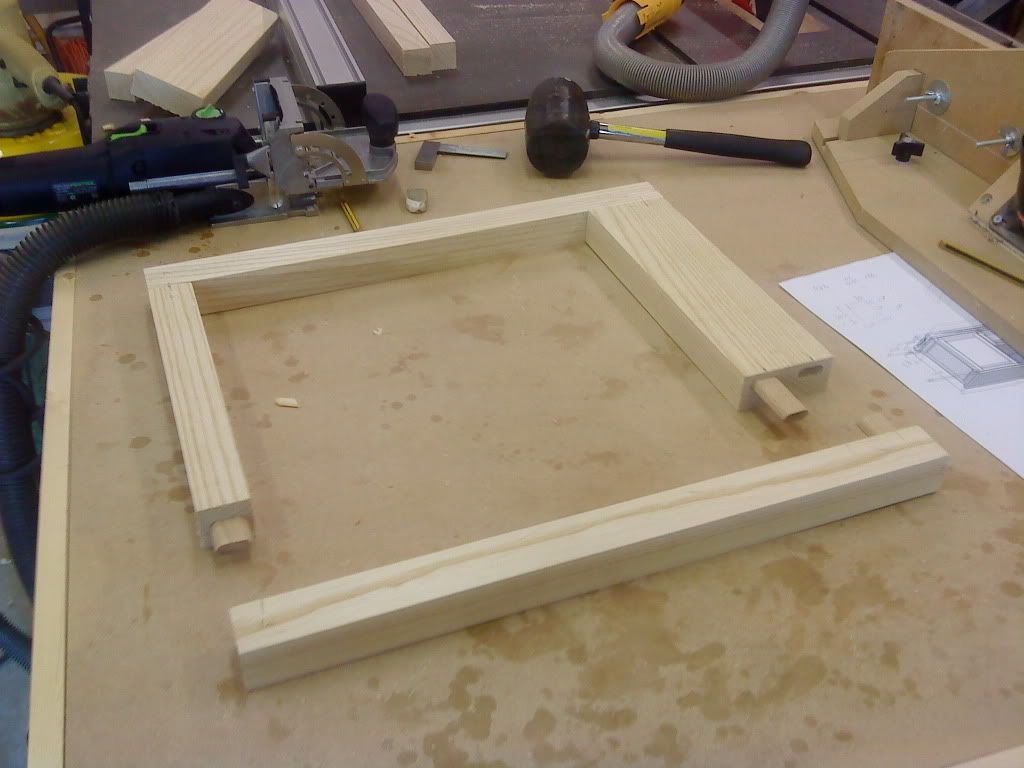
The glued up 4 parts to do make the panels for the frames, wished I had a bandsaw at this point, could have book matched them as the stock was very thick.
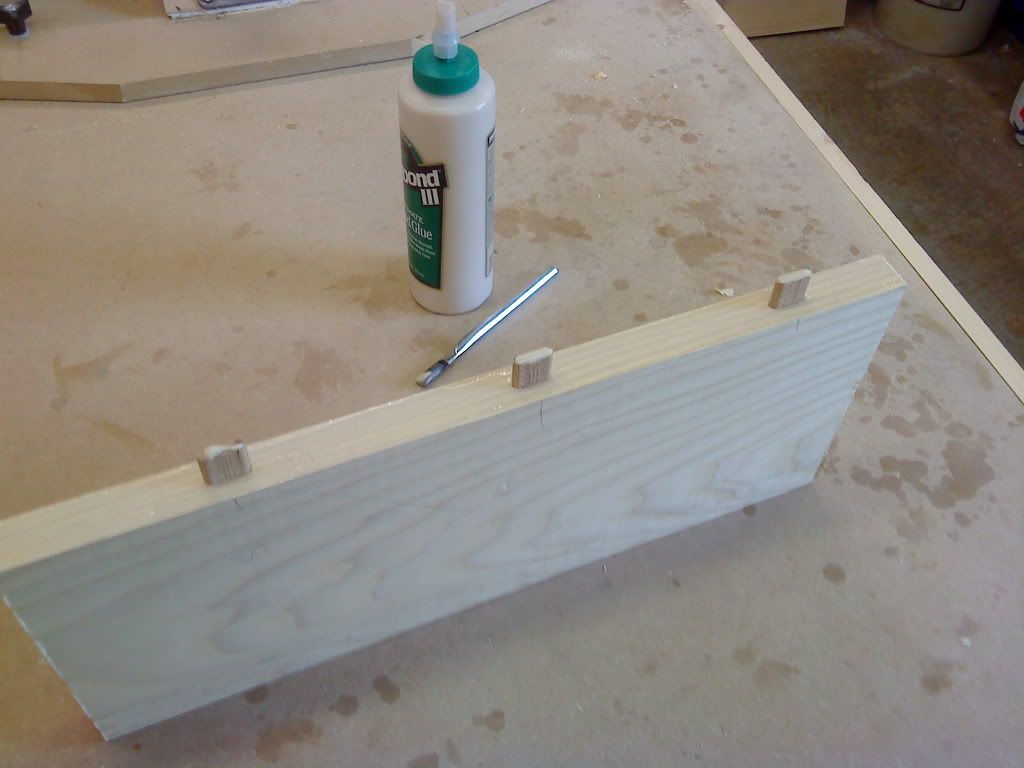
I want it finished by next Wednesday, not including the weekend as I probably won't touch it over then. I do so wish I had a drum sander thou

Target for tomorrow, completed frame, bottom shelf and uprights, ready then for top, door and drawer next week.