WarnerConstCo.
Member
- Joined
- Apr 14, 2008
- Messages
- 4,205
It turns out that my 30" jointer needed the bearings repoured.
First thing to do was buy a hunk of 4140 HTSR shaft to be used as a mandrel. Next, it and the cutter head had to go to my machinists so he could make it match the journals on the head and make me two retaining collars.
Then I poured bearings. I melted out the bottoms first, plugged wick hole an oil return wells, cut some 1/8" wood shims, blackened the shaft and pulled it tight to the top caps (used as a reference) and poured.
Flip over and pour the other bottom. Wait an hour and melt top caps out and repeat the process.
Later I will set the yoke in the machine, open up the wick and oil return holes, cut in some oil grooves, blue the shaft and then scrape the bearings in.
These will last me the rest of my life.
Here are some answers to a few questions I have been asked:
The mandrel is two fold, the cutter head is super freaking heavy and there is a possibility to spring the journals pouring the molten metal on them. I would not want to ruin that cutter block.
The collars were for two reasons, to keep the mandrel in place (I had to flip the shaft end for end to pour the opposite end bearings) and to help seal it. I only had to use some damming putty in a few places (the bluish purple stuff) to keep the babbit in.
I will blue the mandrel journals with high spot dye and spin it in the bearings I will scrape them to fit, 50% contact works. I also have to dig out the wick plugs, drill out the return holes and cut oil grooves.
I will replace the wood shims with paper shims, I can adjust the fit accordingly and remove shims over time as the bearings ware.
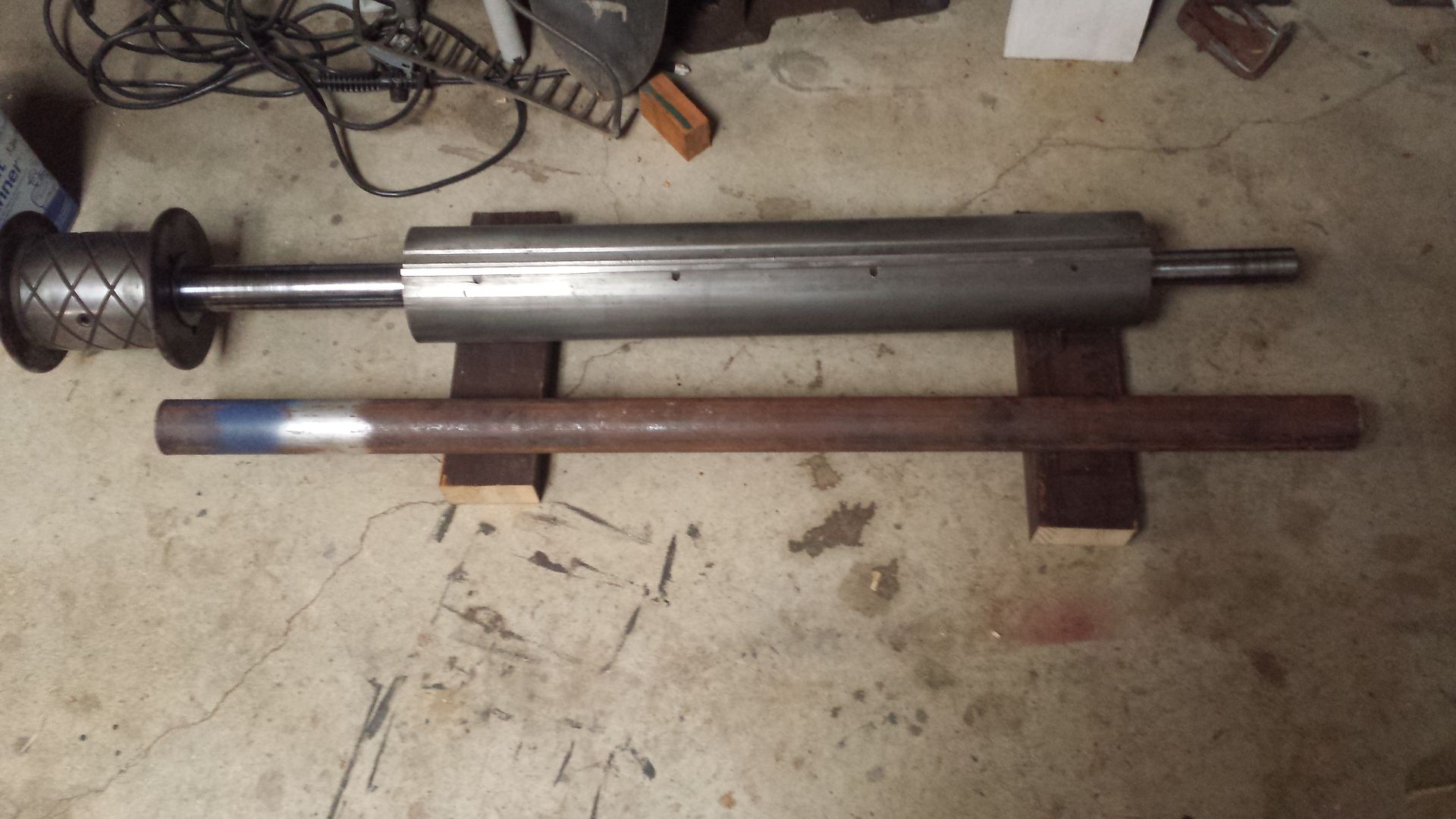
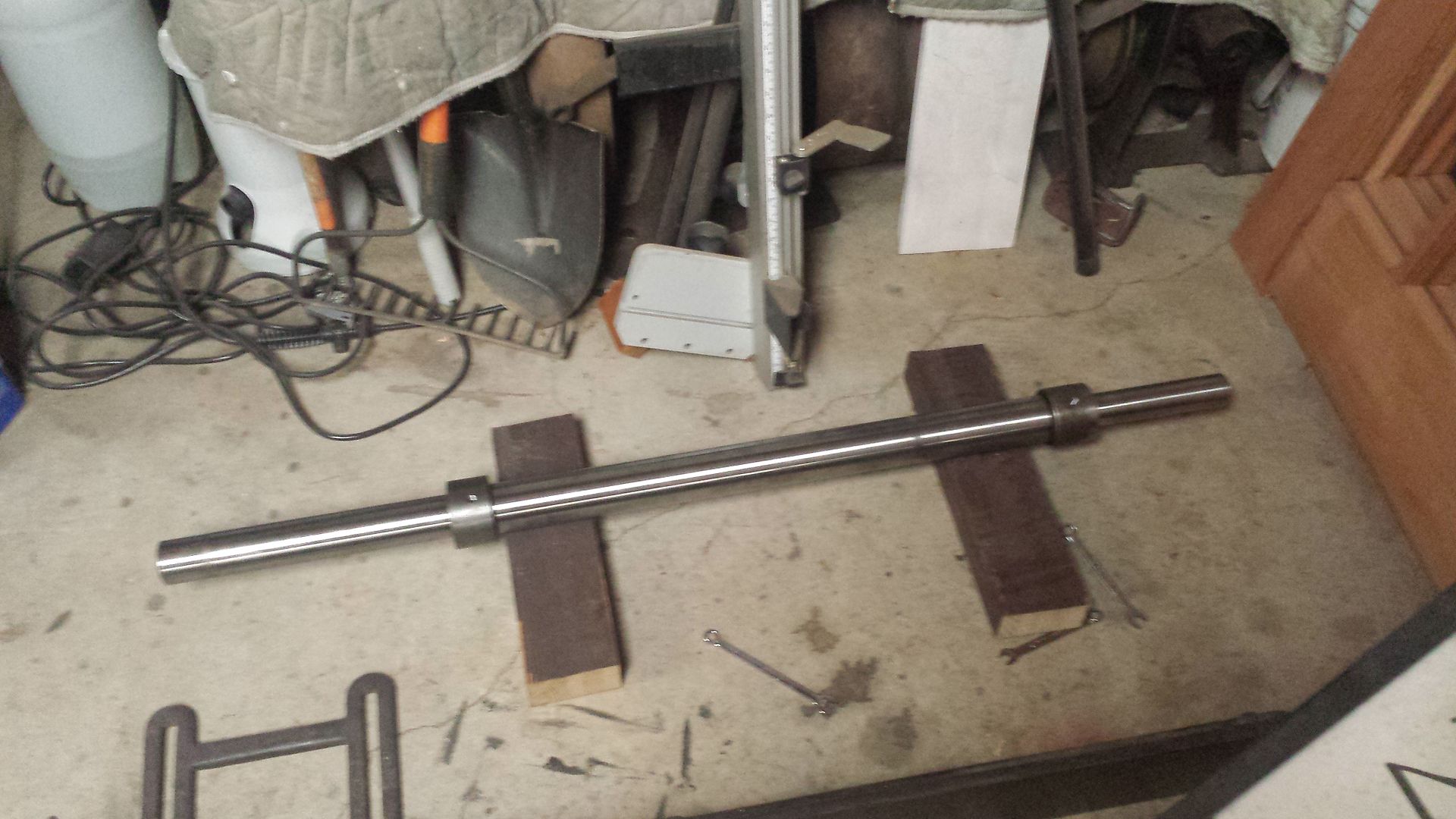
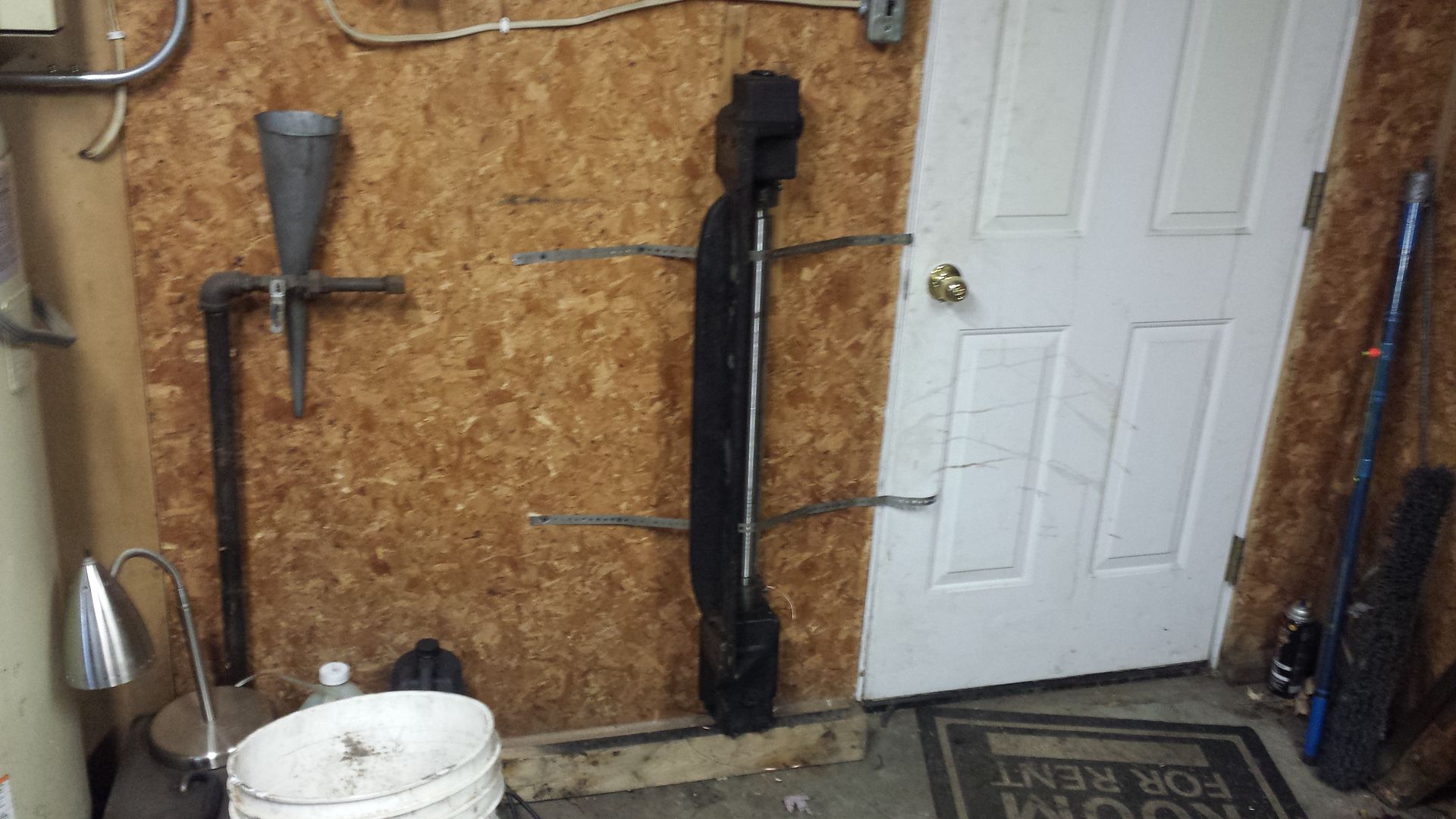
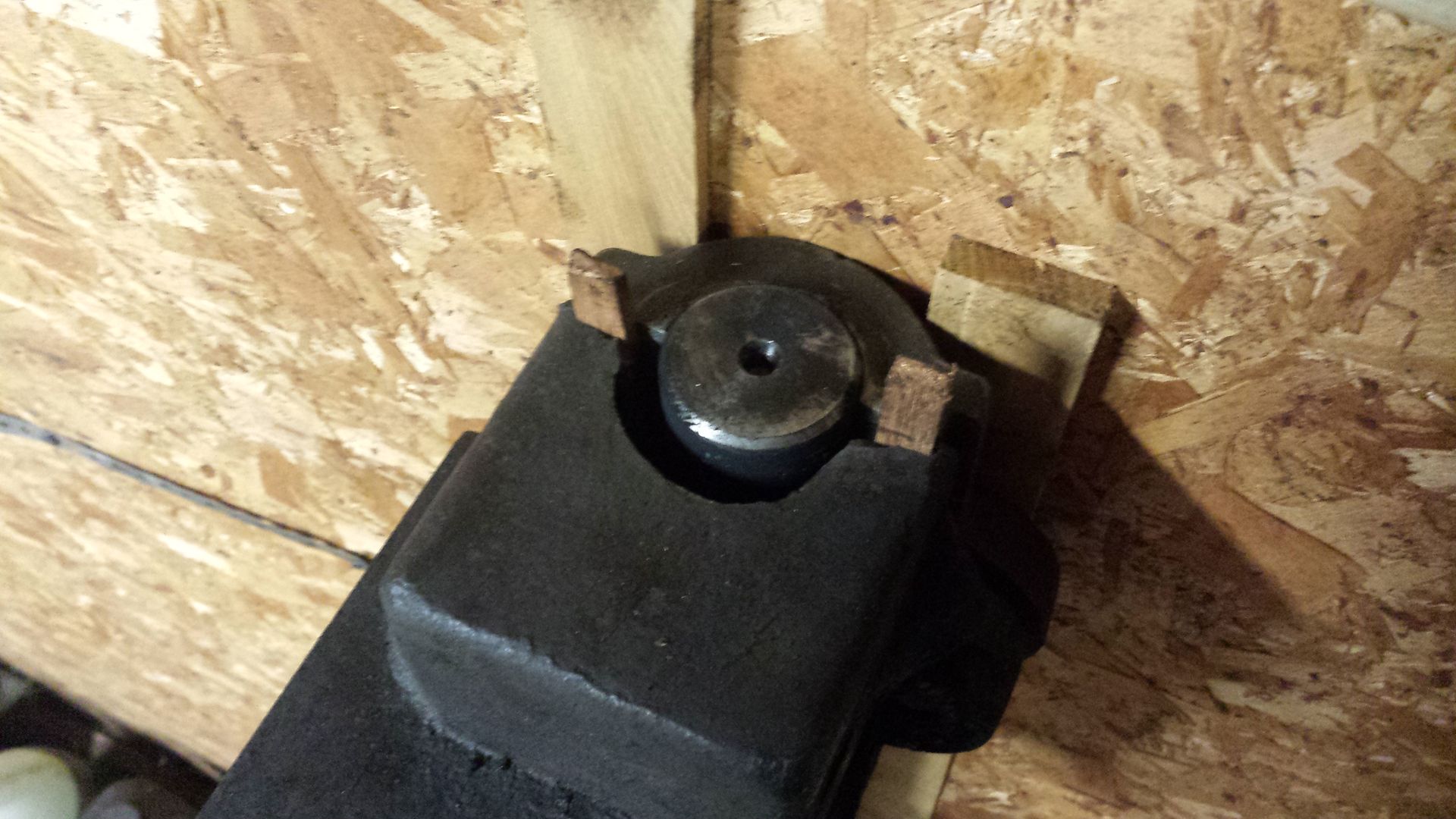
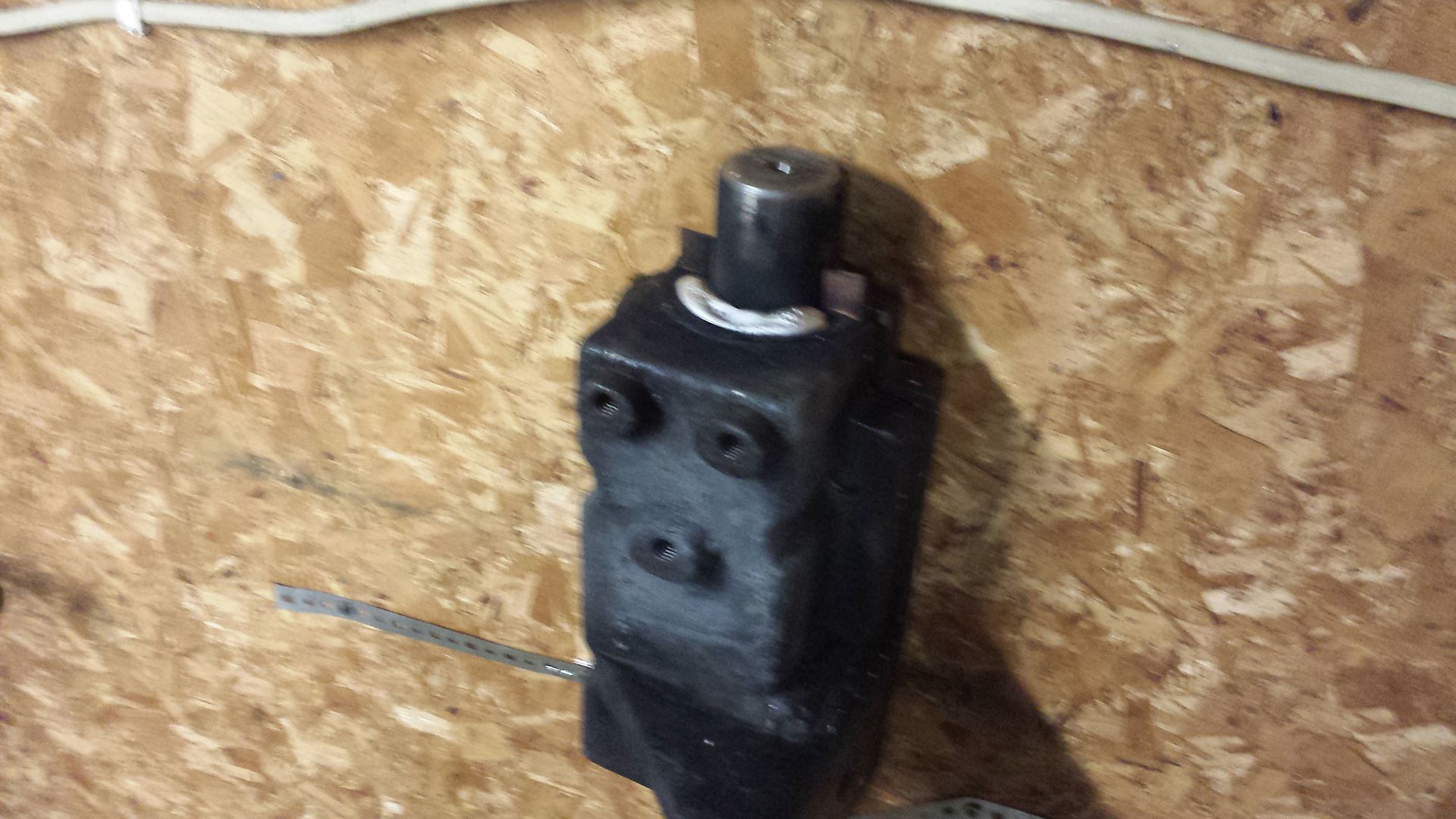
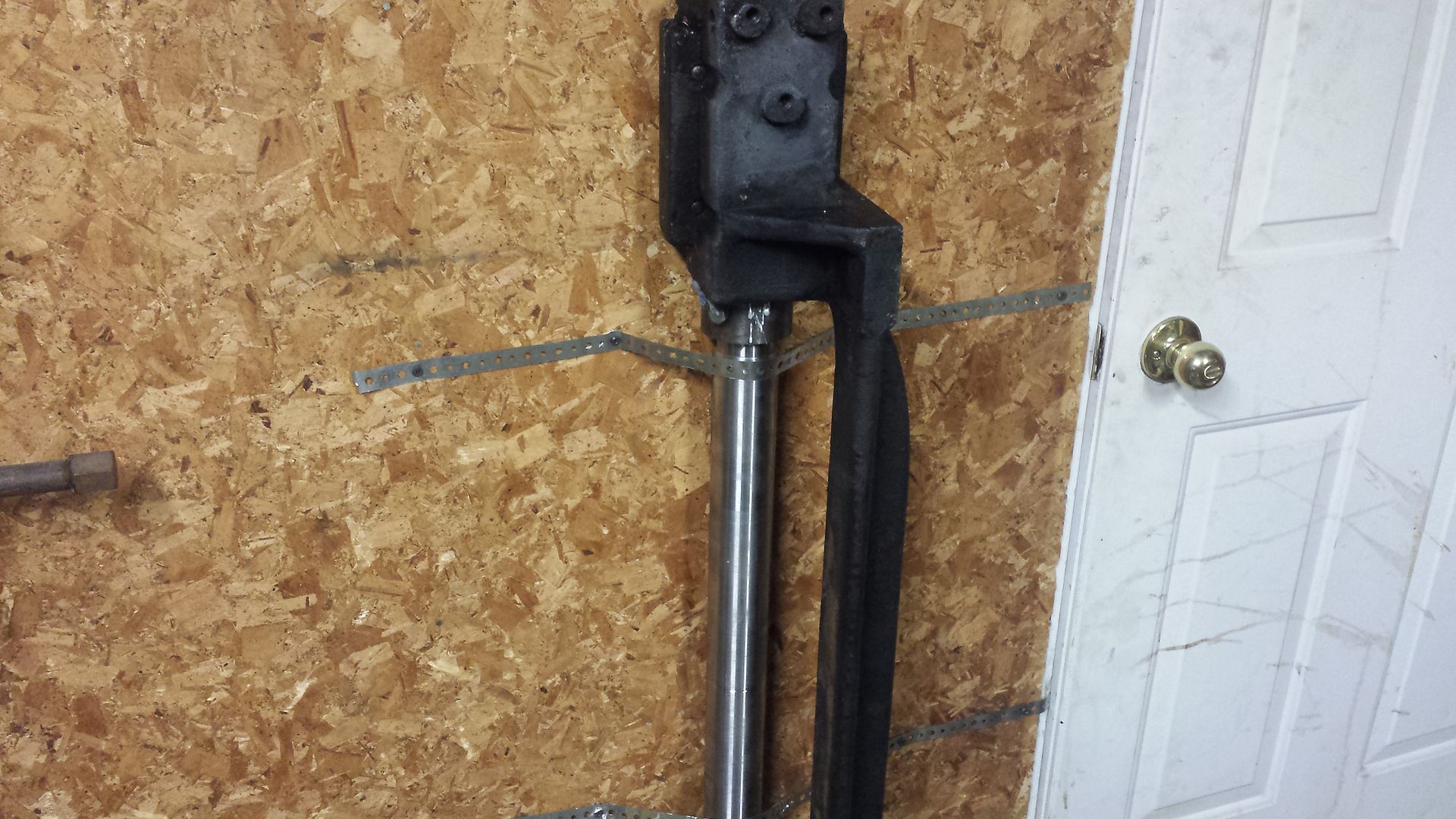
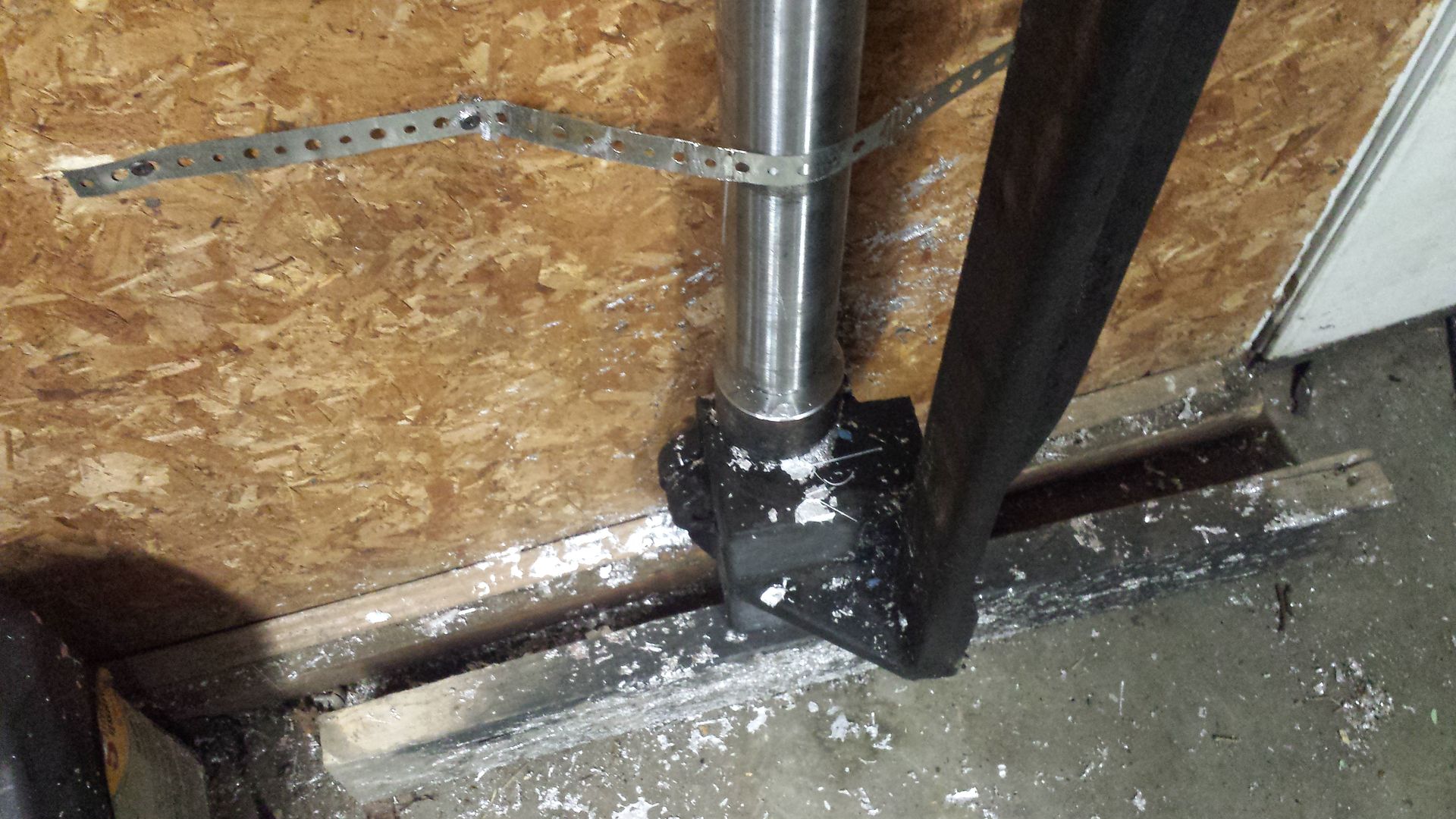
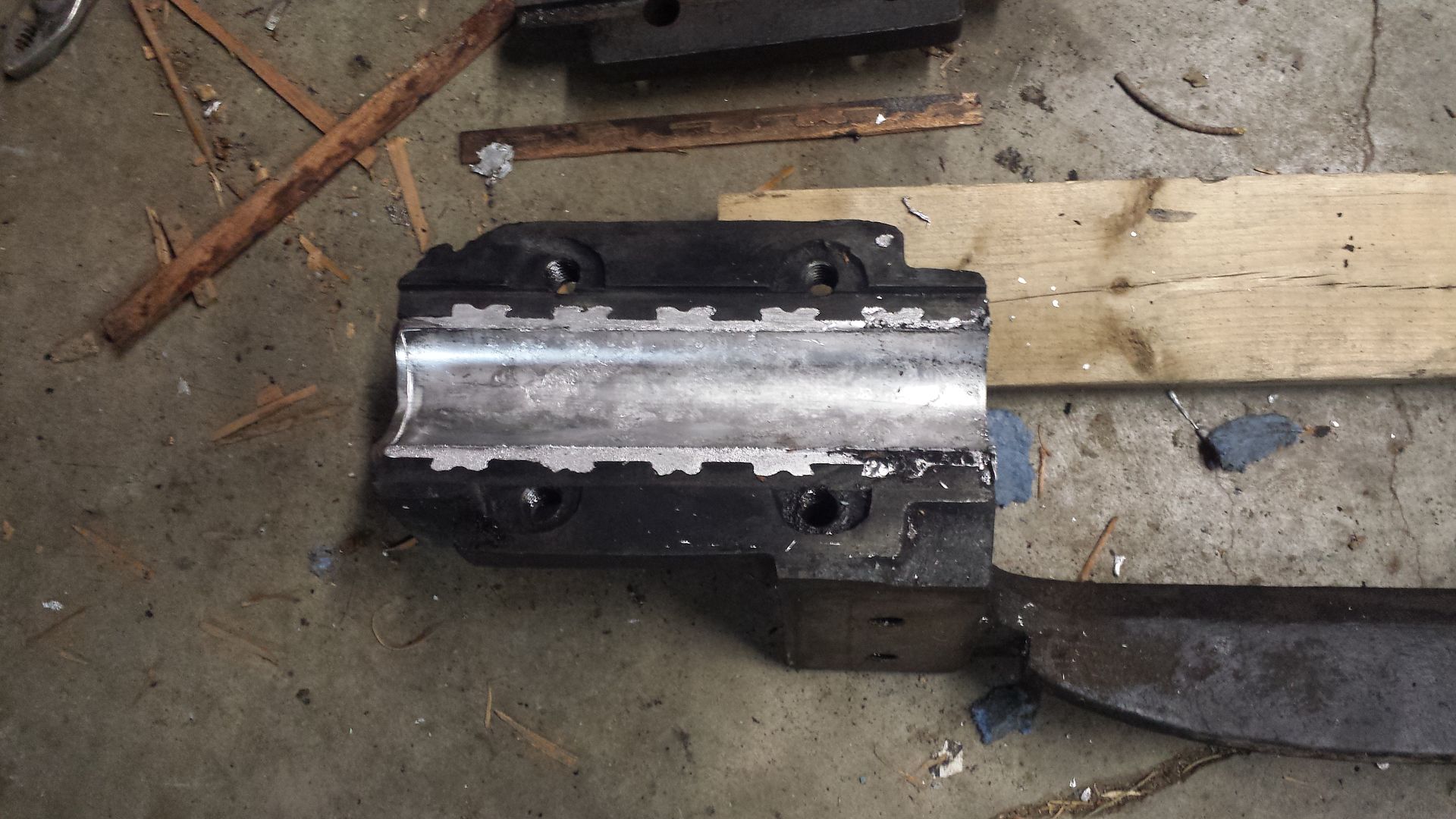
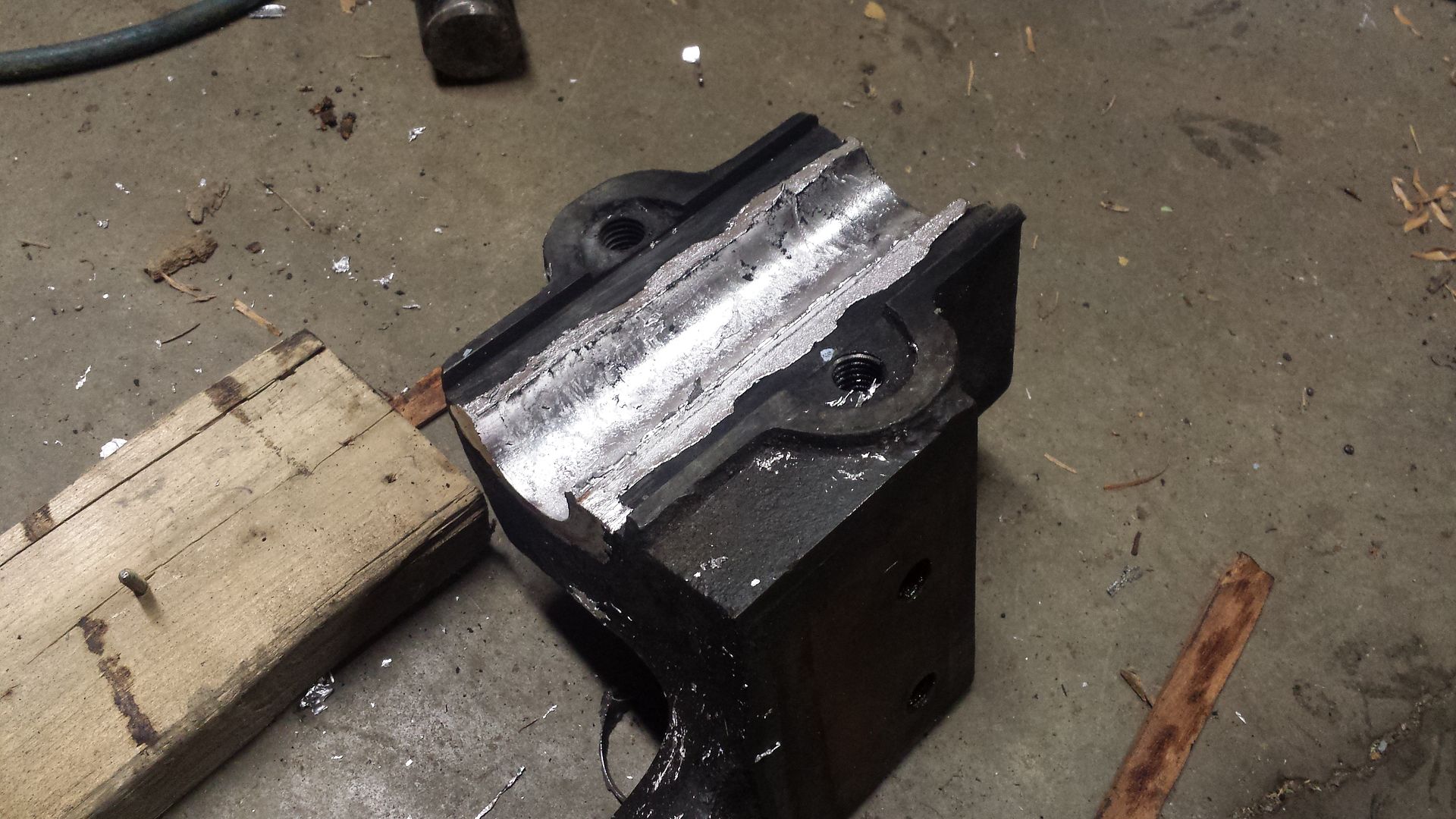
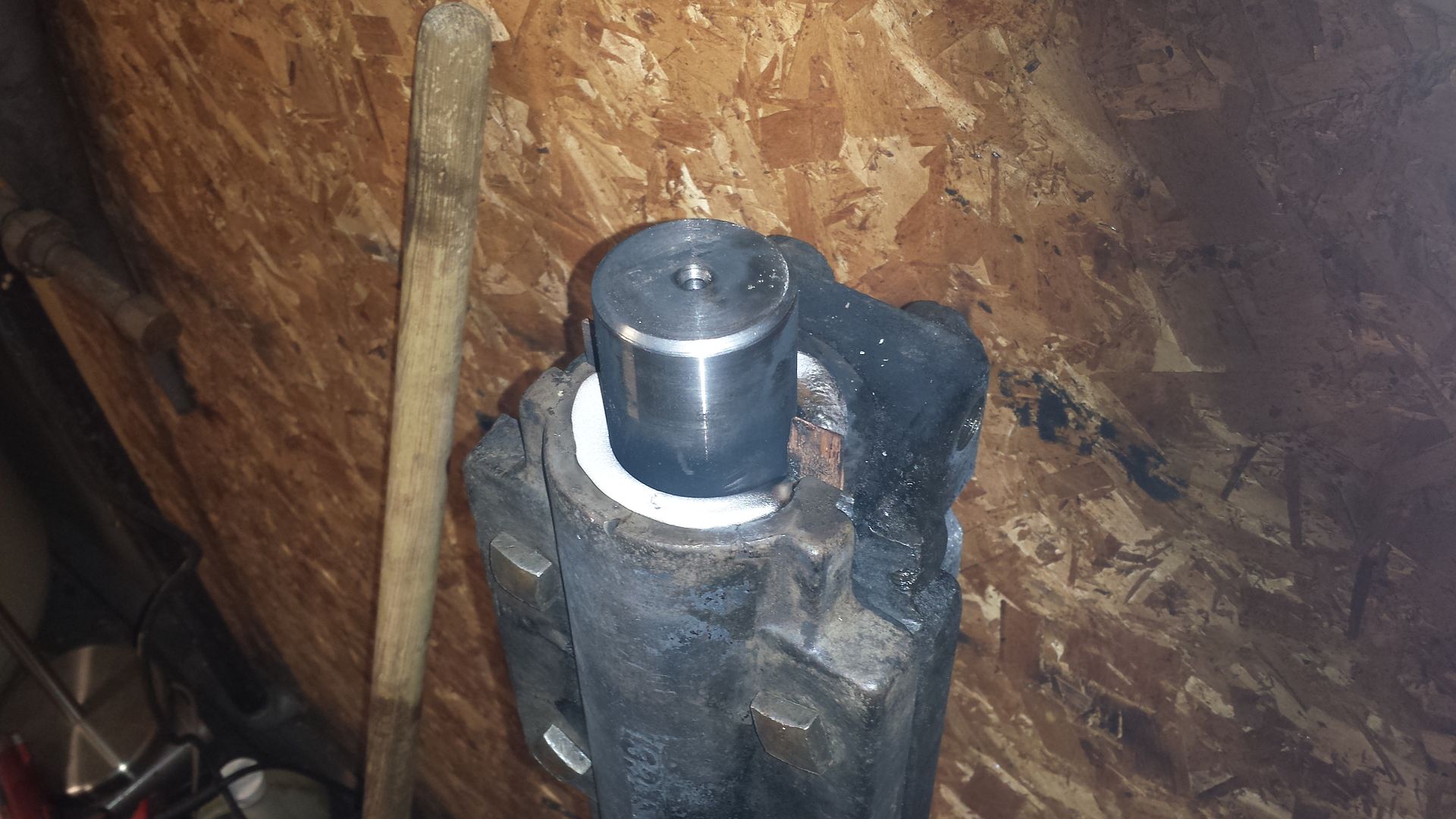
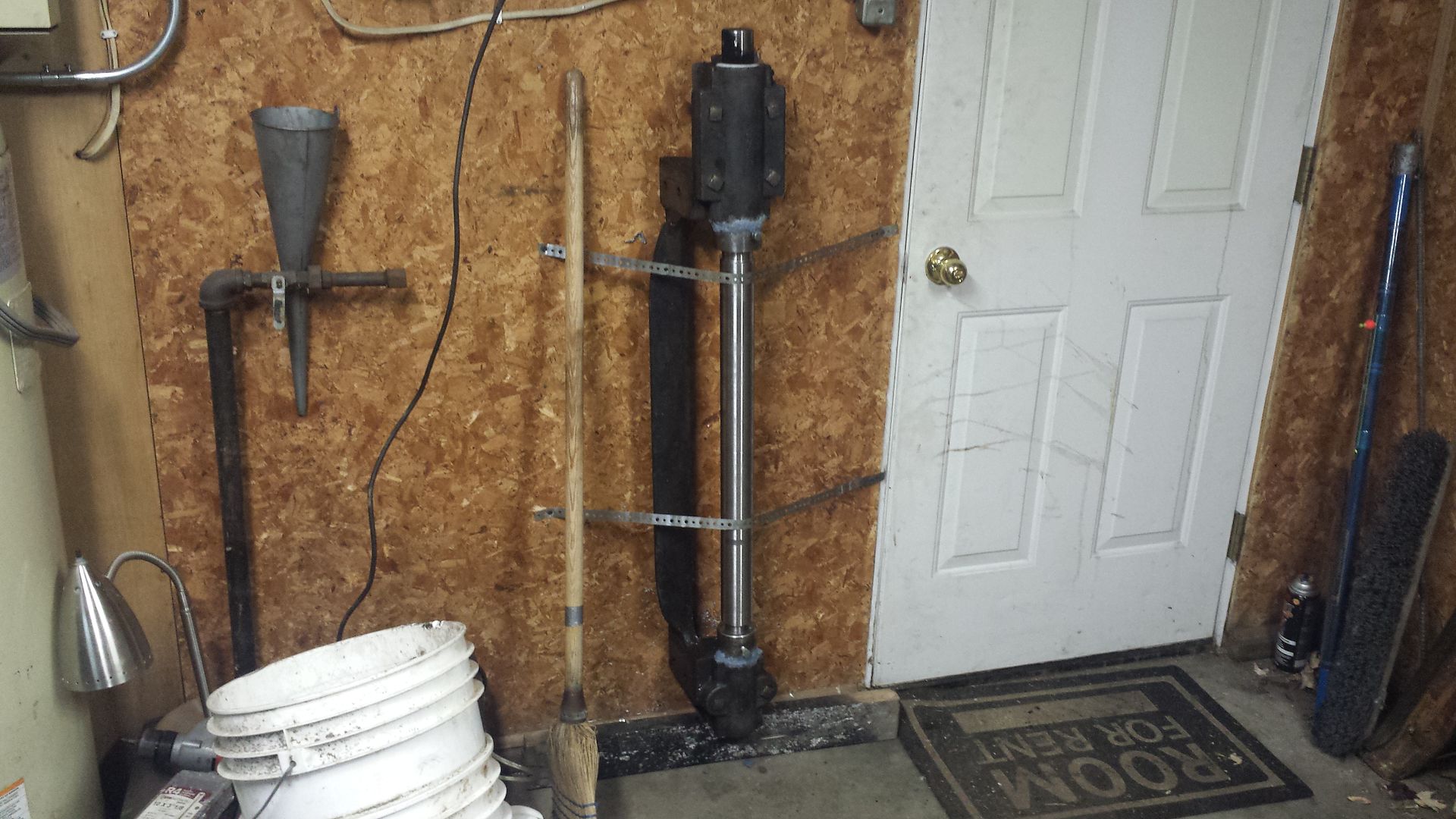
First thing to do was buy a hunk of 4140 HTSR shaft to be used as a mandrel. Next, it and the cutter head had to go to my machinists so he could make it match the journals on the head and make me two retaining collars.
Then I poured bearings. I melted out the bottoms first, plugged wick hole an oil return wells, cut some 1/8" wood shims, blackened the shaft and pulled it tight to the top caps (used as a reference) and poured.
Flip over and pour the other bottom. Wait an hour and melt top caps out and repeat the process.
Later I will set the yoke in the machine, open up the wick and oil return holes, cut in some oil grooves, blue the shaft and then scrape the bearings in.
These will last me the rest of my life.
Here are some answers to a few questions I have been asked:
The mandrel is two fold, the cutter head is super freaking heavy and there is a possibility to spring the journals pouring the molten metal on them. I would not want to ruin that cutter block.
The collars were for two reasons, to keep the mandrel in place (I had to flip the shaft end for end to pour the opposite end bearings) and to help seal it. I only had to use some damming putty in a few places (the bluish purple stuff) to keep the babbit in.
I will blue the mandrel journals with high spot dye and spin it in the bearings I will scrape them to fit, 50% contact works. I also have to dig out the wick plugs, drill out the return holes and cut oil grooves.
I will replace the wood shims with paper shims, I can adjust the fit accordingly and remove shims over time as the bearings ware.
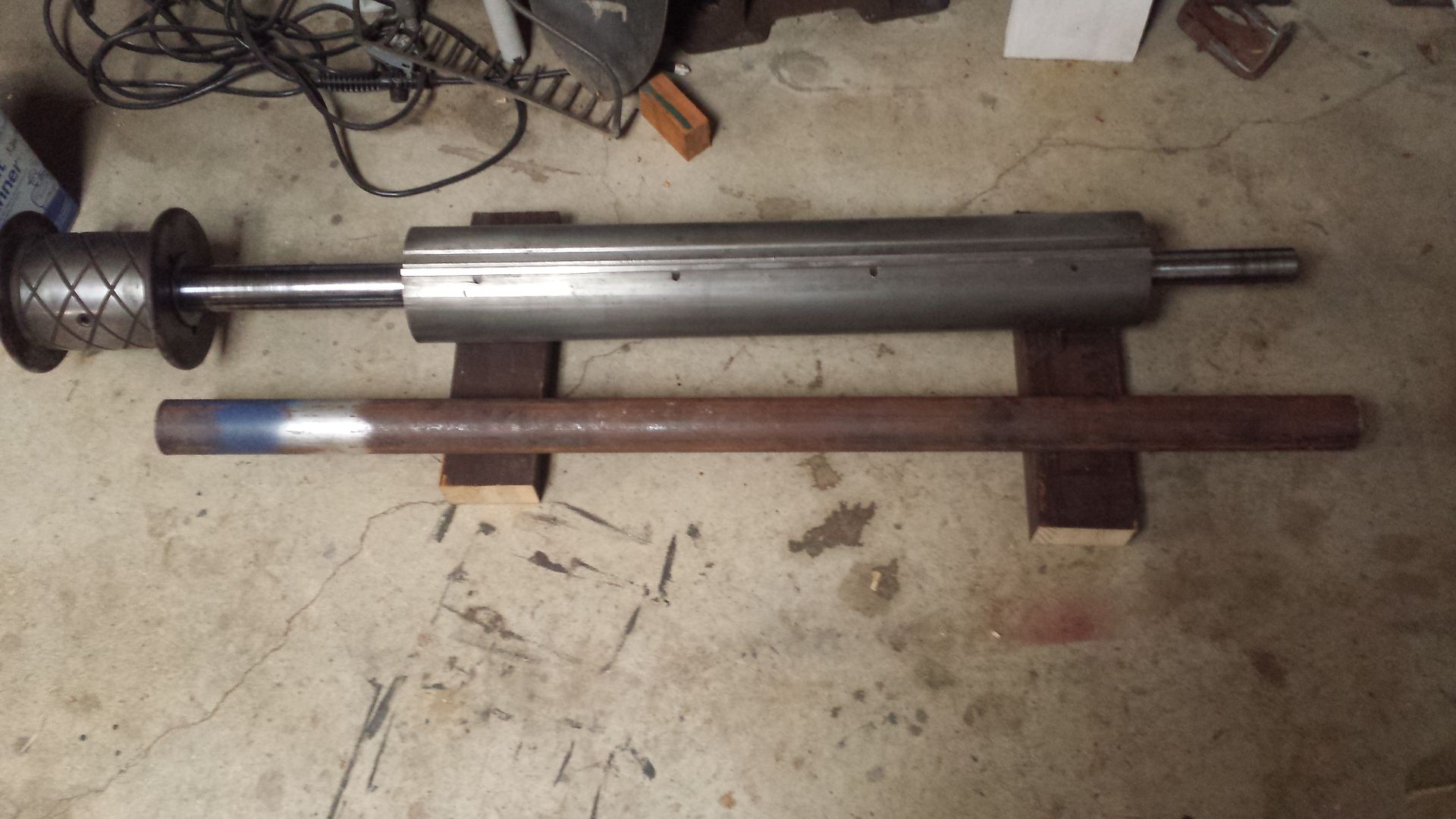
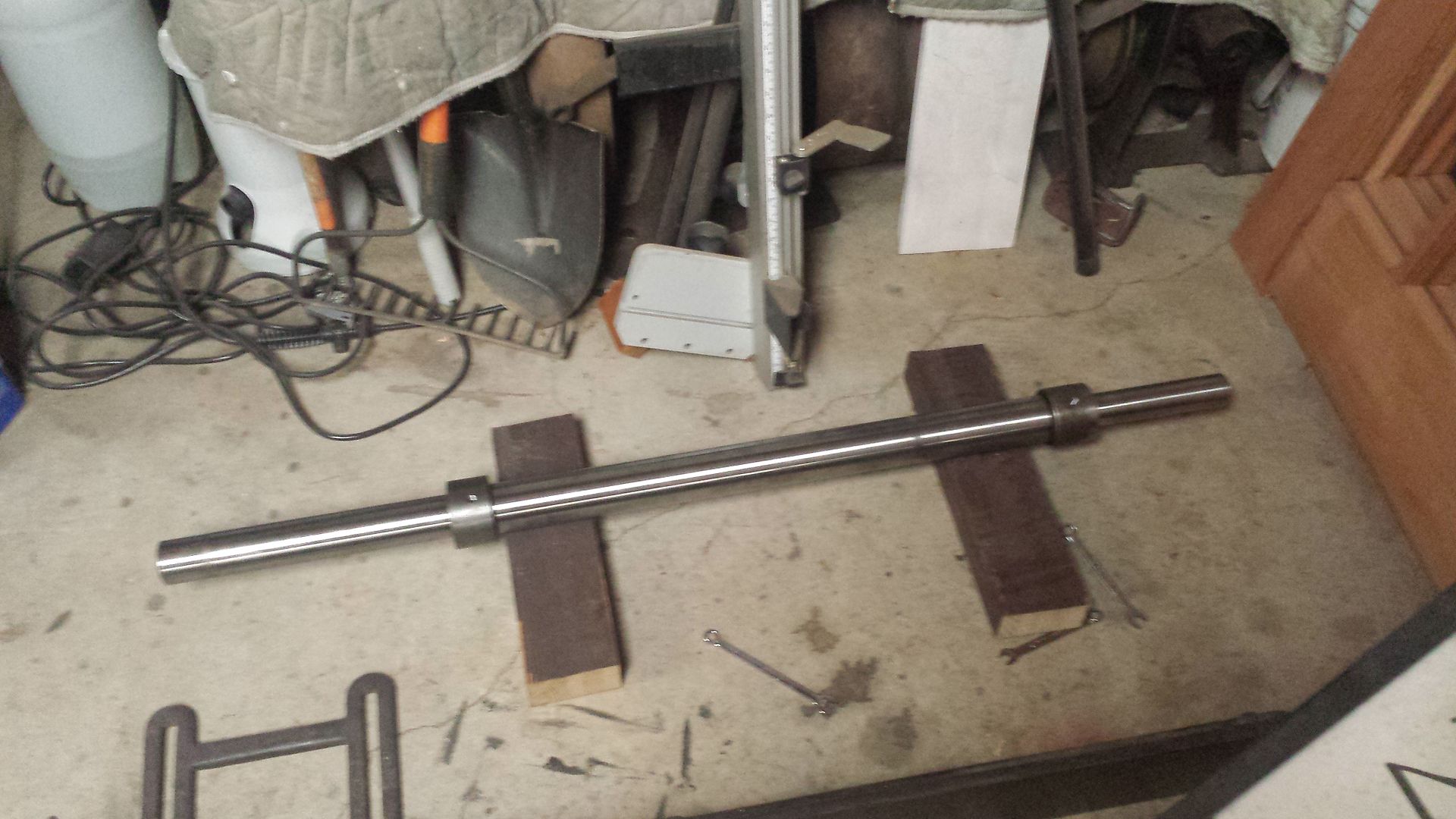
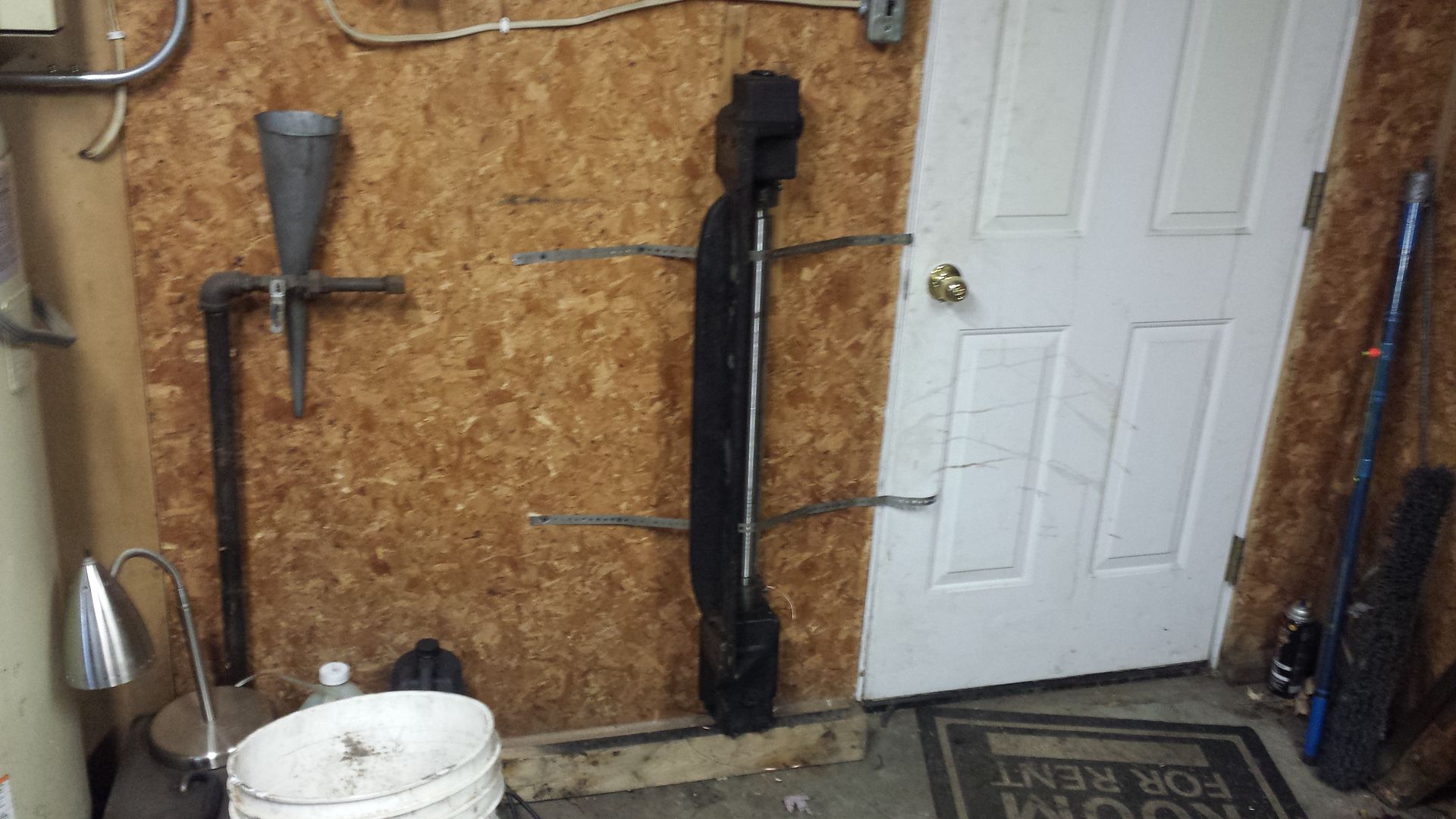
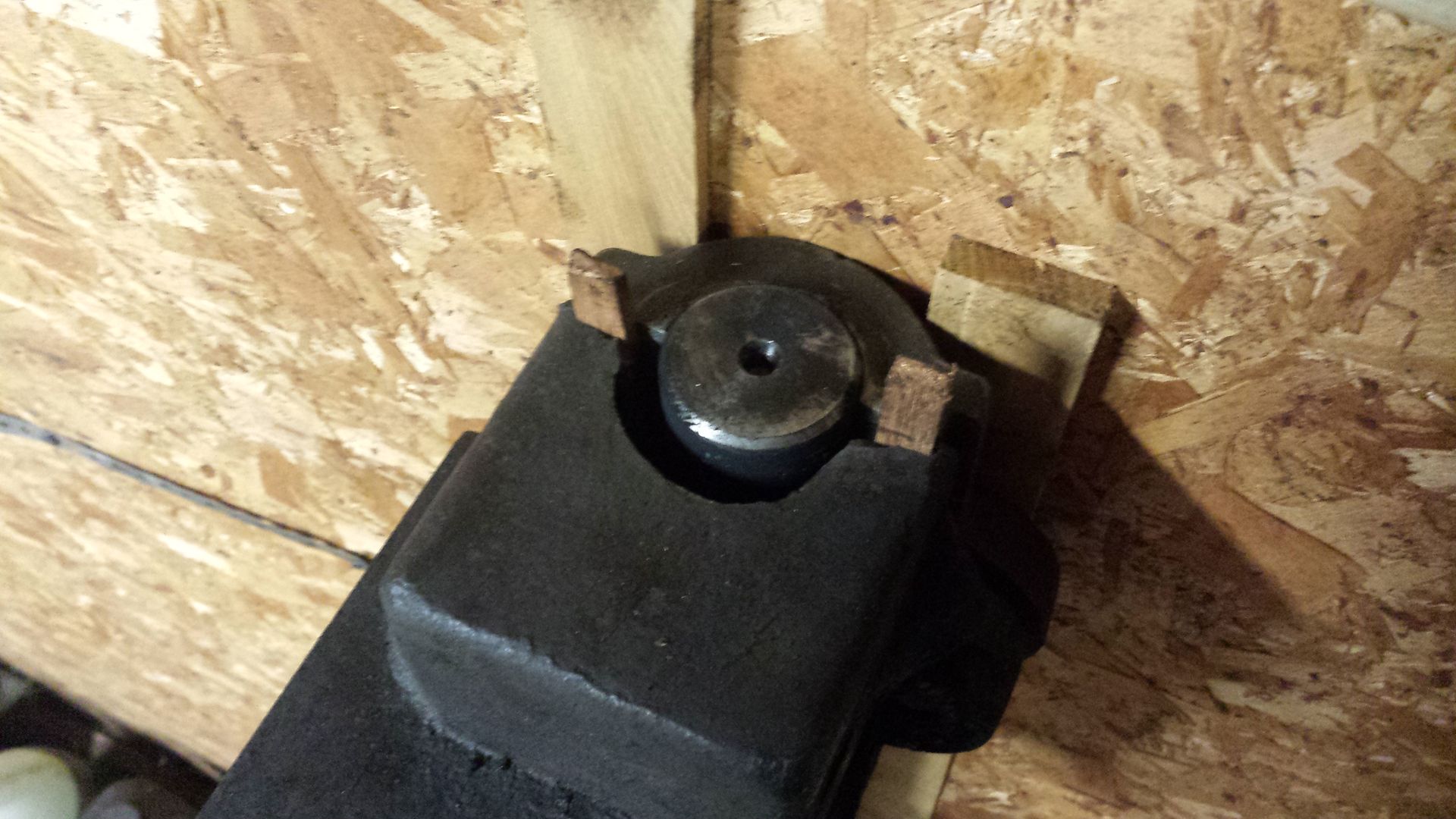
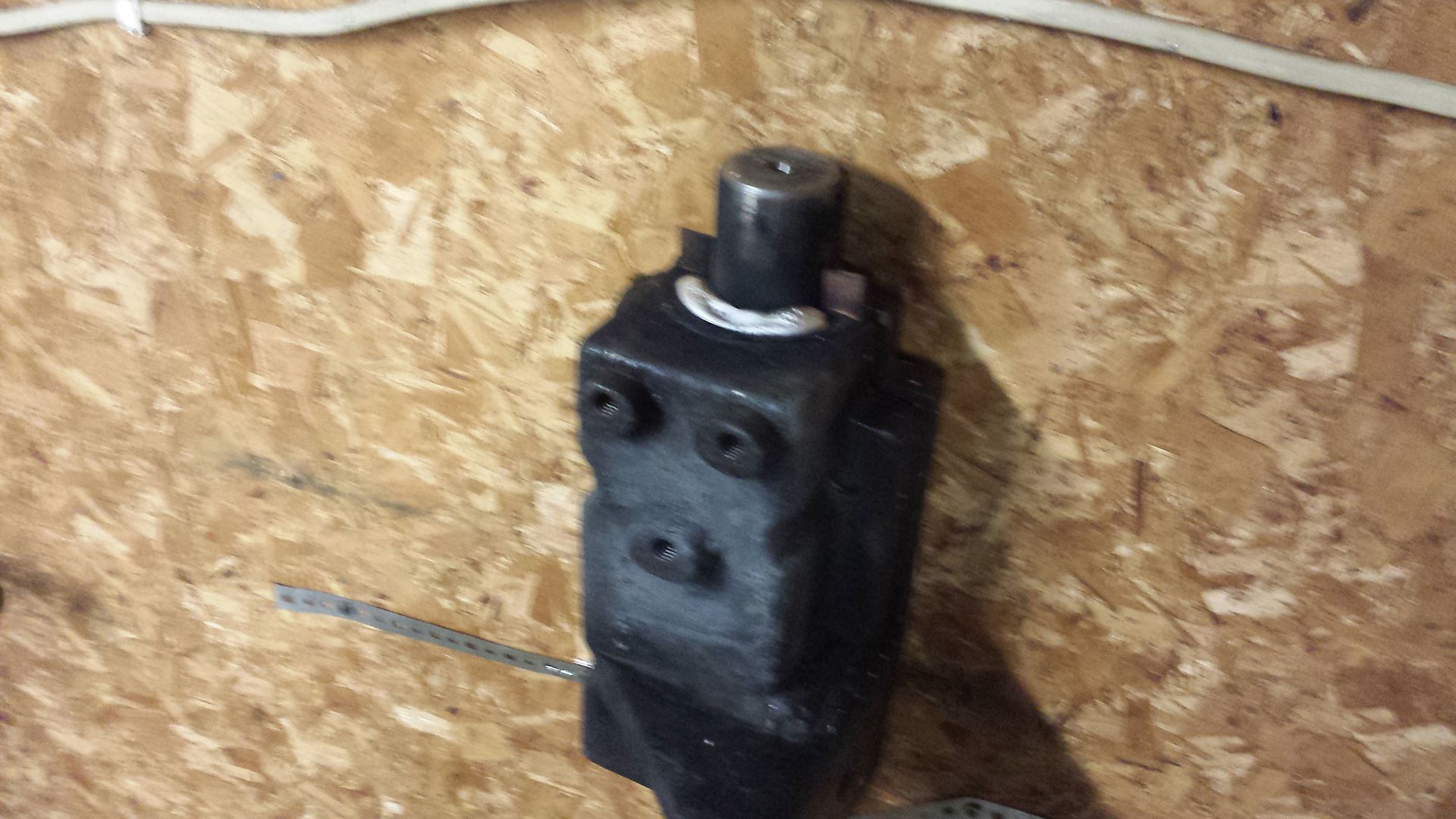
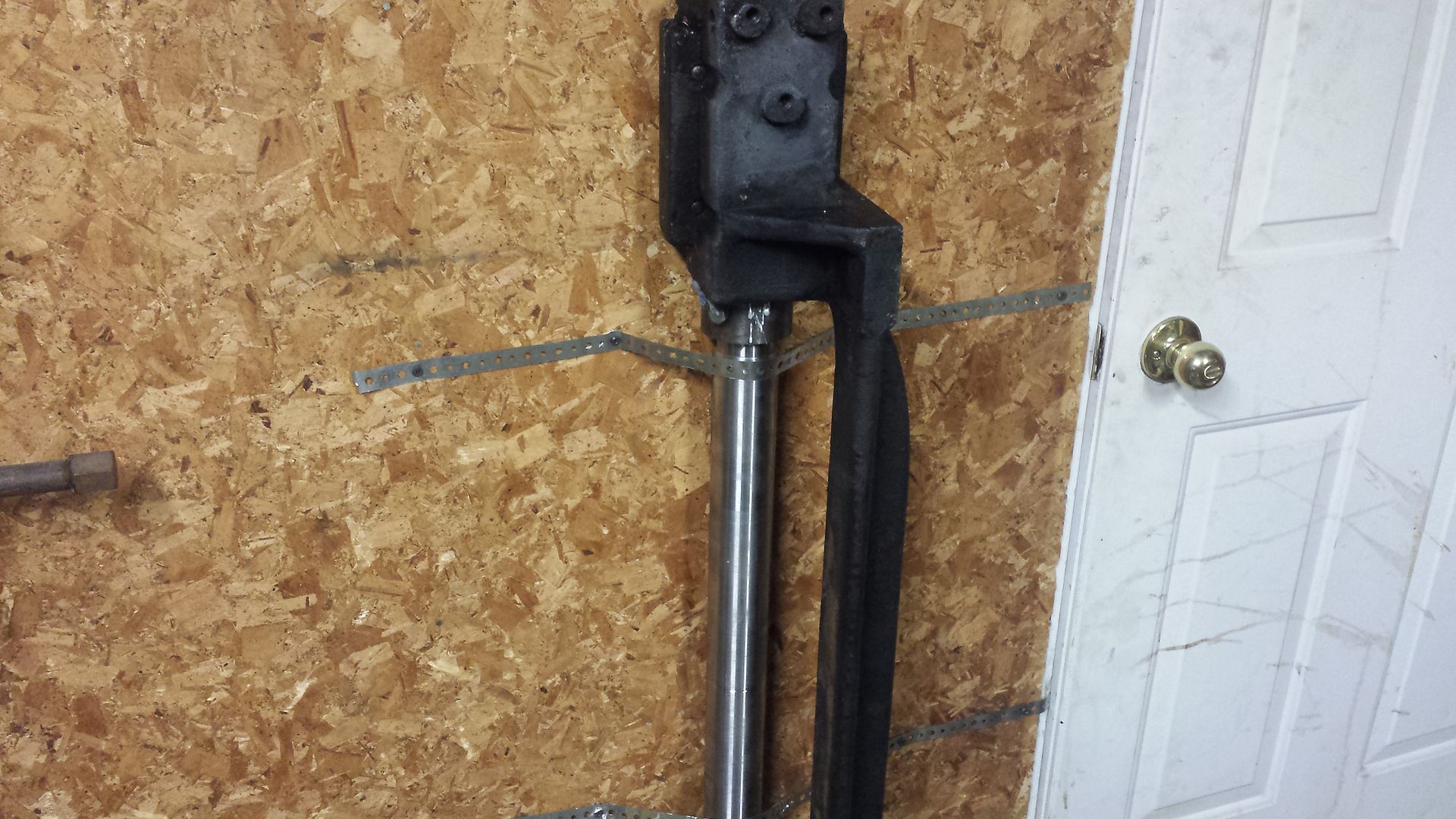
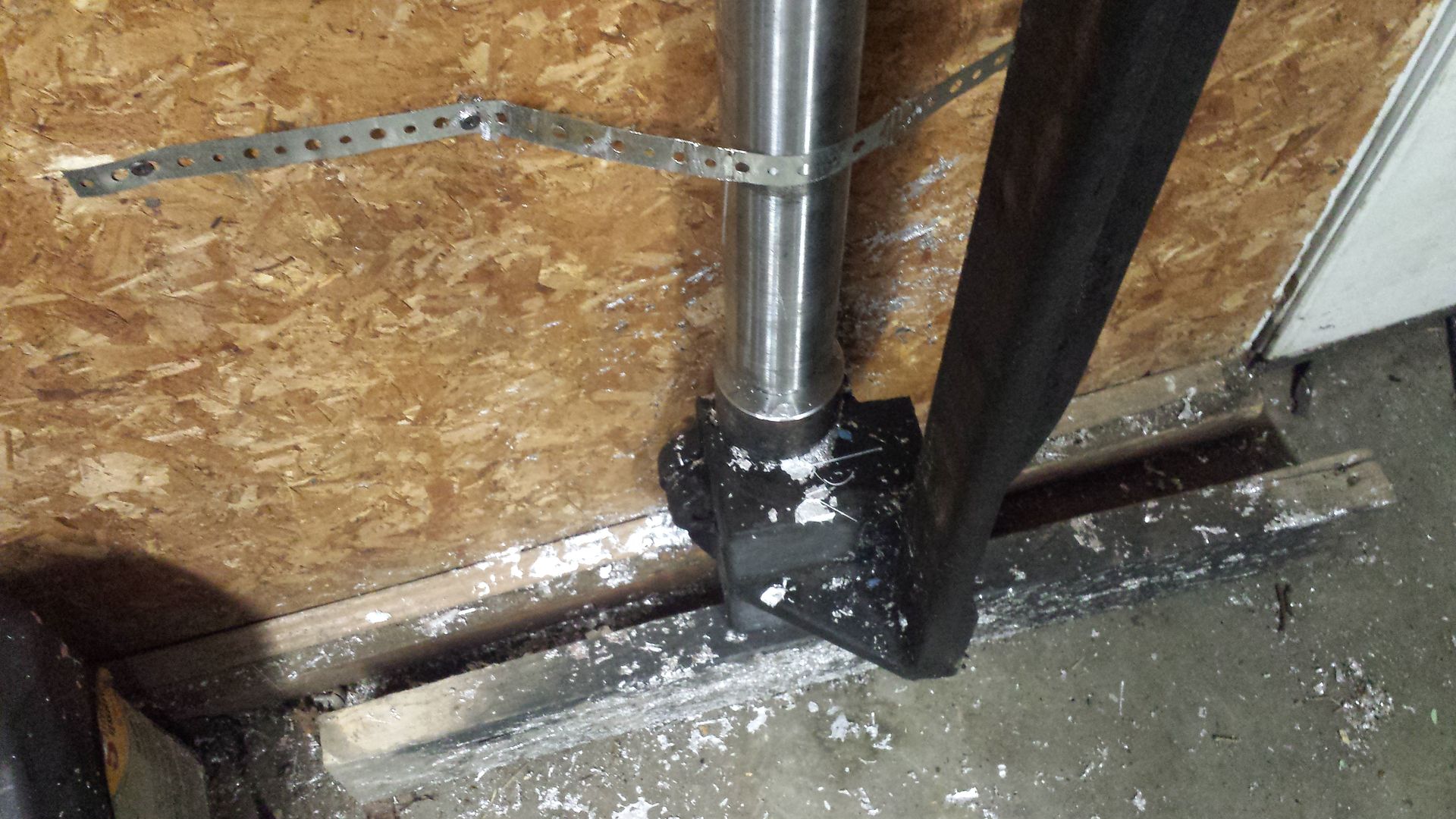
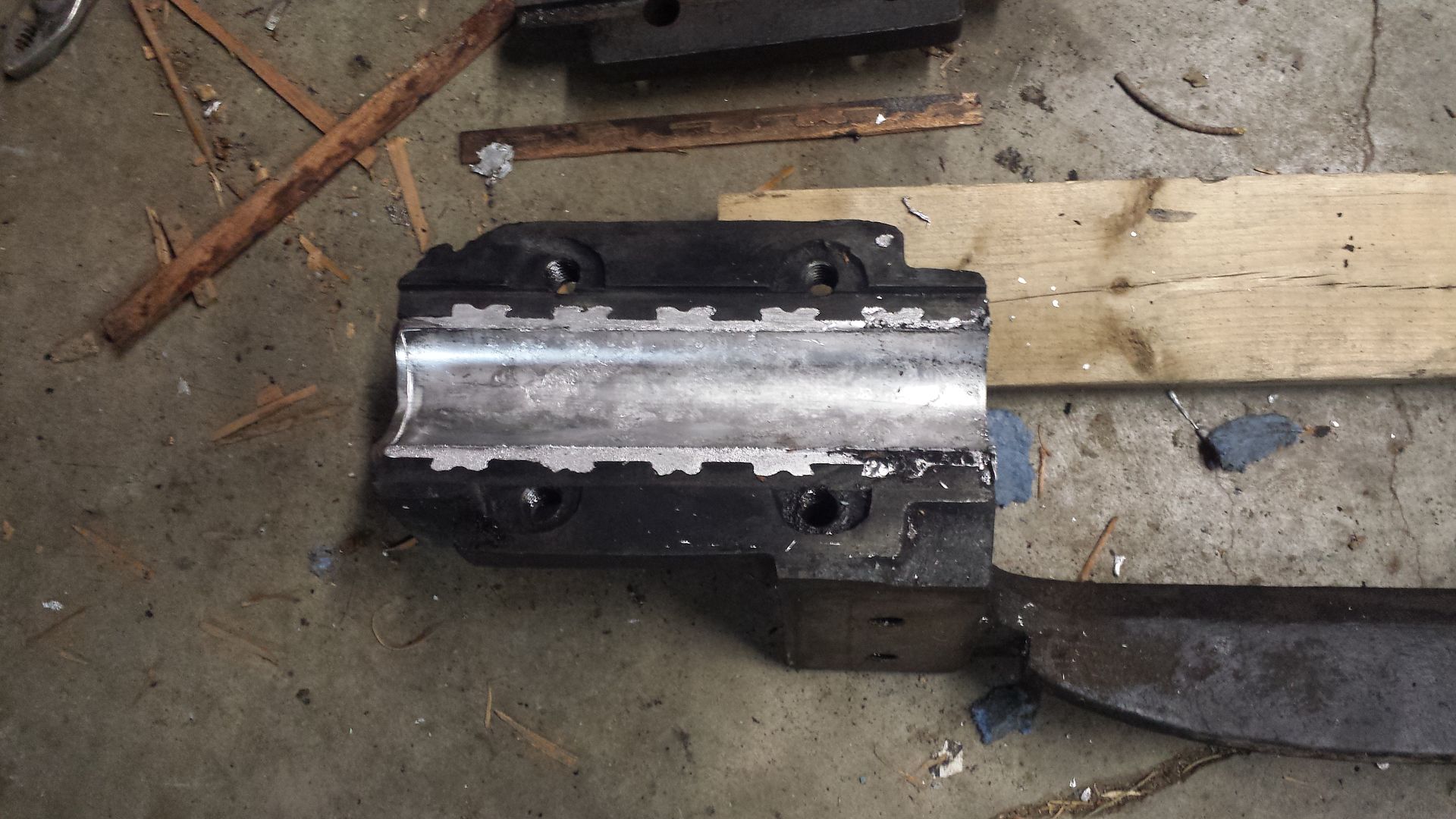
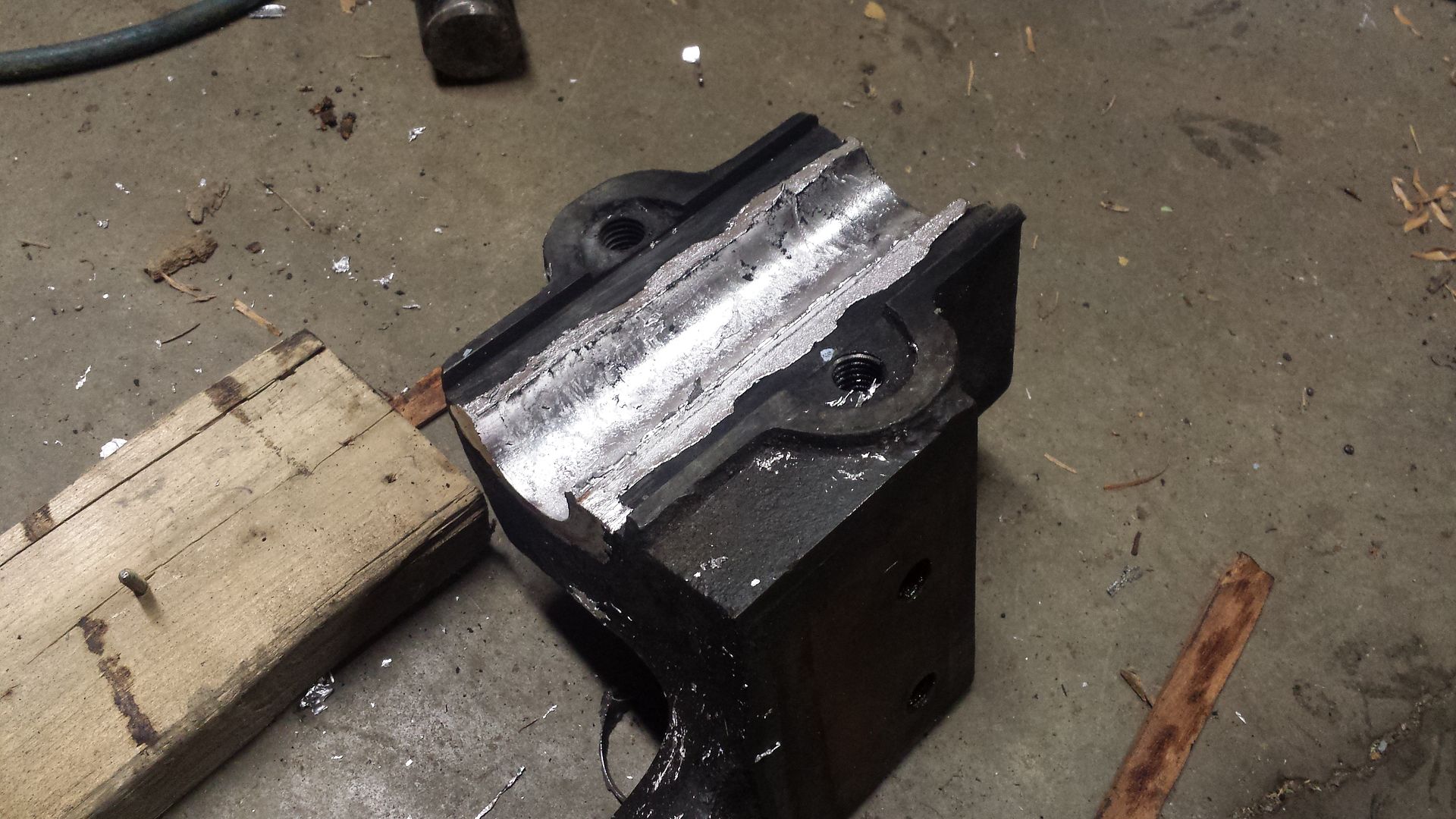
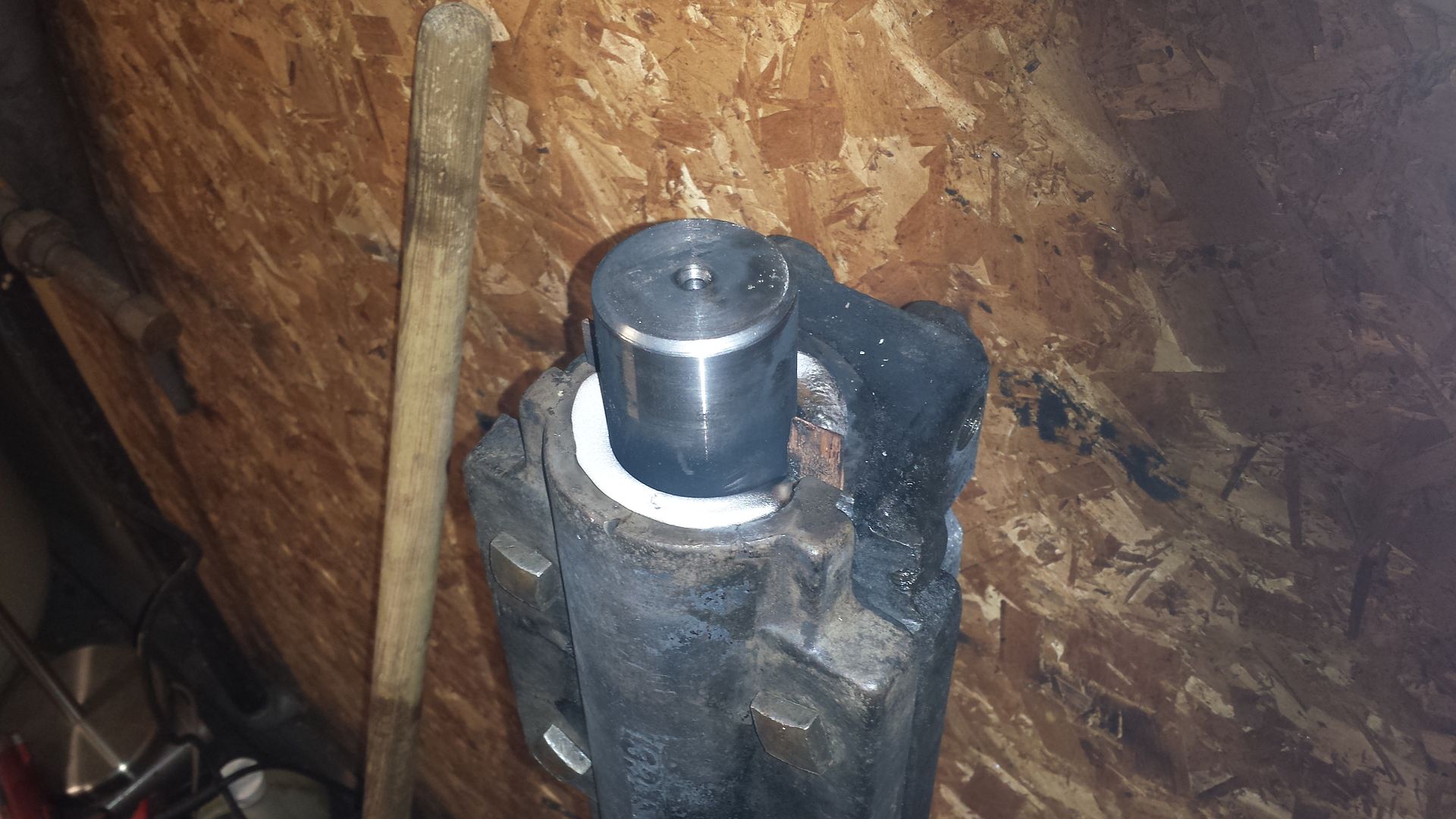
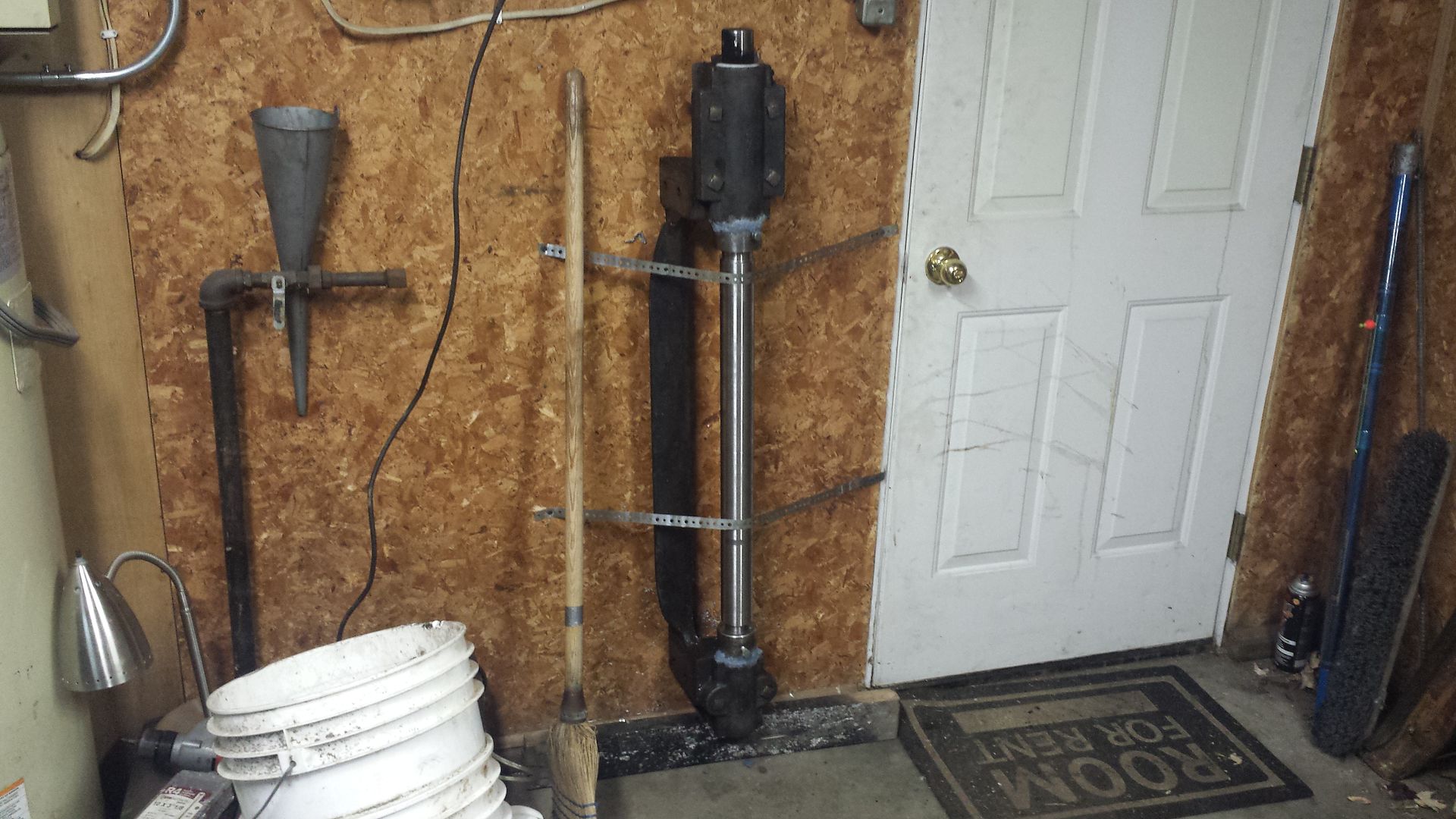