Tom Hummel
Member
- Joined
- Jan 25, 2007
- Messages
- 8
I love my Festool cordless drills and I really appreciate the engineering of the unique Festool chucks. Like others I use square drive Robertson screws along with all the various other types. I have grown to appreciate the accuracy and the speed of the Centrotec chuck. It is so much better than all the other quick change chucks/adapters out there. So this square drive Centrotec void has kept me searching for a better way.
I always assumed that standard 1/4" bits are a little too big to fit in the Centrotec chuck. Not so... the Festool bits simply have the corners knocked off, the flats are the same size as any standard bit. I believe this was posted in an email on the old Festool Yahoo site by Jerry. Aside from that the only significant difference is that the detent is in a different location to allow the shaft of the bit to go all the way inside of the drill.
Experimenting with a 6" squared drive bit and the grinding wheel I was able to produce a crude working version that slipped right into the Centrotec chuck. Once I knew it would work I created the following bits with my Mill/drill. The metal lathe is the perfect tool for this, however I was able to produce nice working versions on my mill with a ball endmill and a straight endmill with my rotary table.
One added benefit with these bits is that the factory detent does not seem to be a problem and as a result my homemade bits fit the offset chuck as well.
I always assumed that standard 1/4" bits are a little too big to fit in the Centrotec chuck. Not so... the Festool bits simply have the corners knocked off, the flats are the same size as any standard bit. I believe this was posted in an email on the old Festool Yahoo site by Jerry. Aside from that the only significant difference is that the detent is in a different location to allow the shaft of the bit to go all the way inside of the drill.
Experimenting with a 6" squared drive bit and the grinding wheel I was able to produce a crude working version that slipped right into the Centrotec chuck. Once I knew it would work I created the following bits with my Mill/drill. The metal lathe is the perfect tool for this, however I was able to produce nice working versions on my mill with a ball endmill and a straight endmill with my rotary table.
One added benefit with these bits is that the factory detent does not seem to be a problem and as a result my homemade bits fit the offset chuck as well.
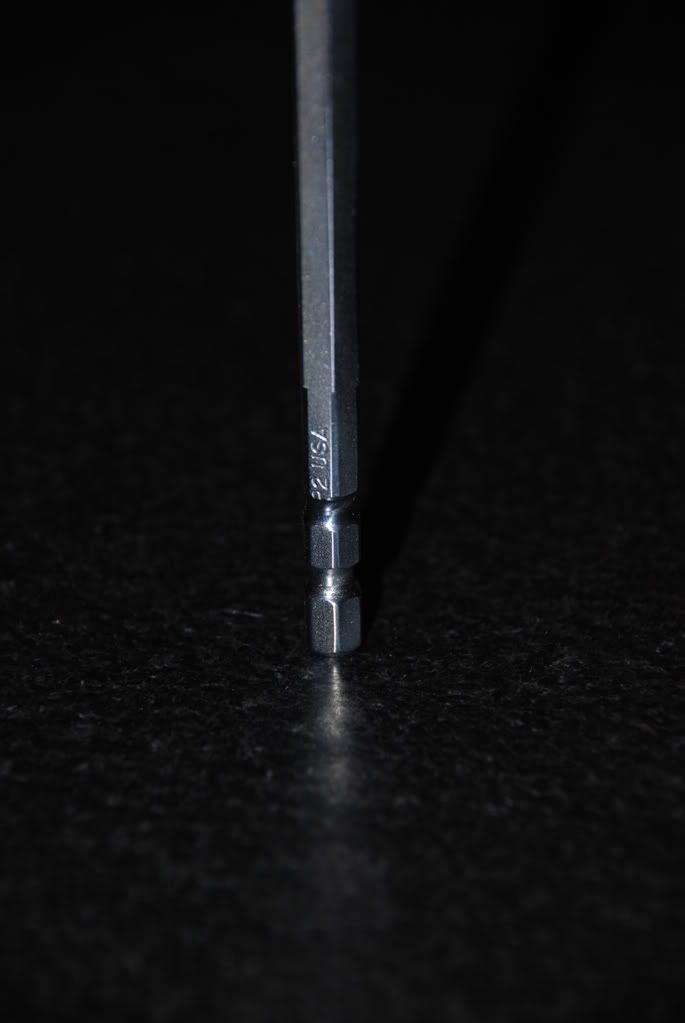
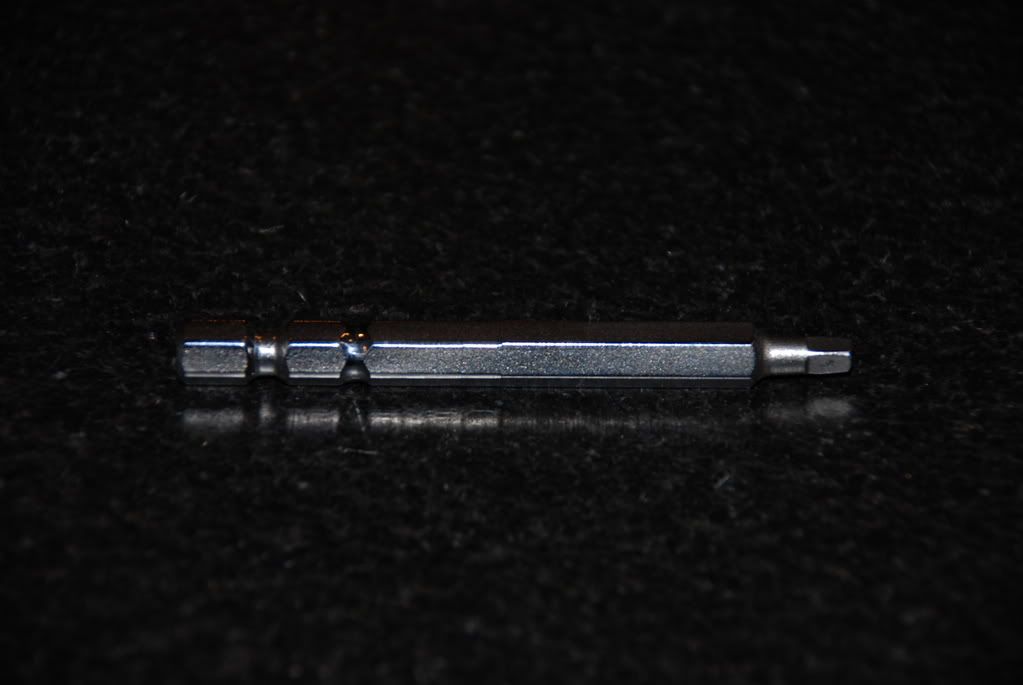