Brice_Arnold
Member
- Joined
- May 22, 2011
- Messages
- 105
I own a small company on the side designing and manufacturing after market parts and tools for the 1/5 scale HPI Baja. Basically a 30 lb R/C car about 2ft long and runs on a glorified weedeater engine capable of producing up an onwards of 7 Hp. These cars start around $1000 and you can easily dump $15,000 into a custom build. I have seen it, I have done it, and I have helped on custom builds. I used to make a driver kit specific to this vehicle. It was basically a 7 piece metric driver kit including the following drivers 1.5mm, 2.0mm, 2.5mm, 3.0mm, 4.0mm, 4.0mm long ball end, and 5.0mm. I made two versions of this kit. A dedicated driver kit and an interchangeable blade kit. The interchangeable blade also had an adapter so that the blades could be used with a power driver. I basically designed a driver from the ground up with every feature that I wanted in a driver. This was my version of the ultimate driver. To help offset the cost of getting these drivers made I did a small run and sold them. I no longer make these kits because they are expensive and there is not much interest from the RC community for these kits. I guess they have a hard time swallowing the $250 price tag. Though they were expensive I never heard of anyone who purchased the product ever regretting the purchase.
Some of the features that I included in my design:
-Tool steel precision ground tip, hard enough to never wear out.
-Because the tips are hard they are brittle and can break if misused. Therefore, they were designed to be replaceable.
-Billet aluminum handle for some added weight. I am a firm believer in the direct correlation in the mass of an item and the inherent quality of said item. I find this to be true with tools, machines, furniture, and stereo equipment.
-A pivoting cap at the base of the handle. This fits in the palm of your hand and allows for rapid screwing while applying pressure to the driver. The cap pivots on a delrin bushing.
-A cross hole so that a breaker bar can be used for stubborn screws
-Color coded drivers so that you can instantly tell what size the driver is.
Even though I no longer sell the driver kits. I still have all the parts sitting around in bins. I was looking at my Toolie (Yes, I actually own one of these rare beauties) wishing I had more than one and a thought occured to me. I could make my own driver kit specific to the Festool products that had all the bits found in the Toolie. From my R/C kit I only had the hex tips. So for the Torx, Phillips, and Slotted tips I found some drivers that I wouldn't miss and chopped off the blades. I made sure that the blades had some kind of treated tip for wear resistance. Once I was finished with my drivers I started playing around with my vacuum former and making a custom insert container to hold the drivers. Due to the size of my vacuum table I could only make a small insert large enough for a shipping box. In the near future I would like to make a larger table so that I can play around with making full size custom systainer inserts. The process is fairly simply and it would be the epitome of custom organization for the Festool accessories that are otherwise not designed to be stored in the systainers with inserts.
So here is what I came up with. Let me know what you think. Part of this is to show of fmy one-night project and part of it is to determine if there is any interest in a dedicated Festool driver kit.
Here the drivers are tucked away neatly into a shipping box.
Here is the second tier in the box
The four hex drivers: 2.5mm, 3.0mm, 4.0mm, 5.0mm
The five additional drivers: Phillips, Slotted, T10, T15, T20
All nine drivers in the kit
Here is the vacuum formed insert that I roughed out
Driver neatly tucked away in the insert.
The following images are some examples of where the drivers might be used
Using the 2.5mm Hex Driver
Using the 3.0mm Hex Driver
Using the T20 Driver
Using the T15 Driver
Using the T10 Driver
Using the 4.0mm Hex Driver
Using the Slotted Driver
Using the Phillips Driver
I guess that is it for know until I start playing around with more custom inserts and getting these drivers into a systainer or ministainer.
Thanks
Some of the features that I included in my design:
-Tool steel precision ground tip, hard enough to never wear out.
-Because the tips are hard they are brittle and can break if misused. Therefore, they were designed to be replaceable.
-Billet aluminum handle for some added weight. I am a firm believer in the direct correlation in the mass of an item and the inherent quality of said item. I find this to be true with tools, machines, furniture, and stereo equipment.
-A pivoting cap at the base of the handle. This fits in the palm of your hand and allows for rapid screwing while applying pressure to the driver. The cap pivots on a delrin bushing.
-A cross hole so that a breaker bar can be used for stubborn screws
-Color coded drivers so that you can instantly tell what size the driver is.
Even though I no longer sell the driver kits. I still have all the parts sitting around in bins. I was looking at my Toolie (Yes, I actually own one of these rare beauties) wishing I had more than one and a thought occured to me. I could make my own driver kit specific to the Festool products that had all the bits found in the Toolie. From my R/C kit I only had the hex tips. So for the Torx, Phillips, and Slotted tips I found some drivers that I wouldn't miss and chopped off the blades. I made sure that the blades had some kind of treated tip for wear resistance. Once I was finished with my drivers I started playing around with my vacuum former and making a custom insert container to hold the drivers. Due to the size of my vacuum table I could only make a small insert large enough for a shipping box. In the near future I would like to make a larger table so that I can play around with making full size custom systainer inserts. The process is fairly simply and it would be the epitome of custom organization for the Festool accessories that are otherwise not designed to be stored in the systainers with inserts.
So here is what I came up with. Let me know what you think. Part of this is to show of fmy one-night project and part of it is to determine if there is any interest in a dedicated Festool driver kit.
Here the drivers are tucked away neatly into a shipping box.
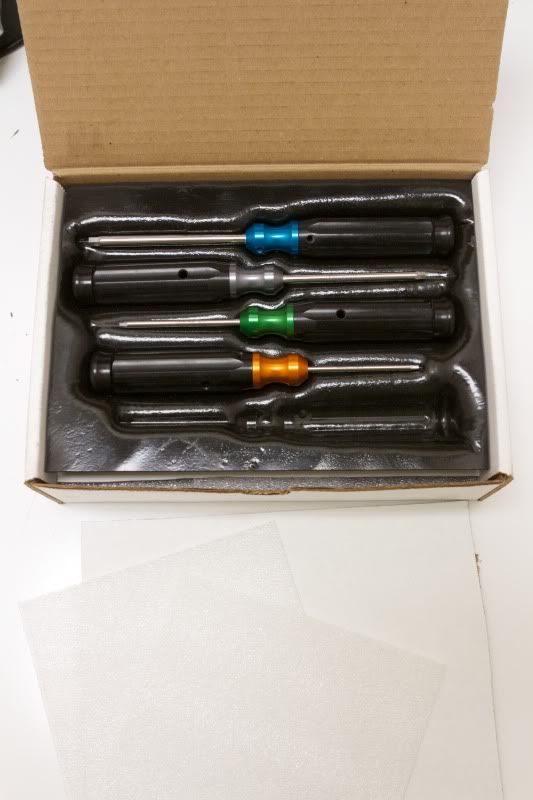
Here is the second tier in the box
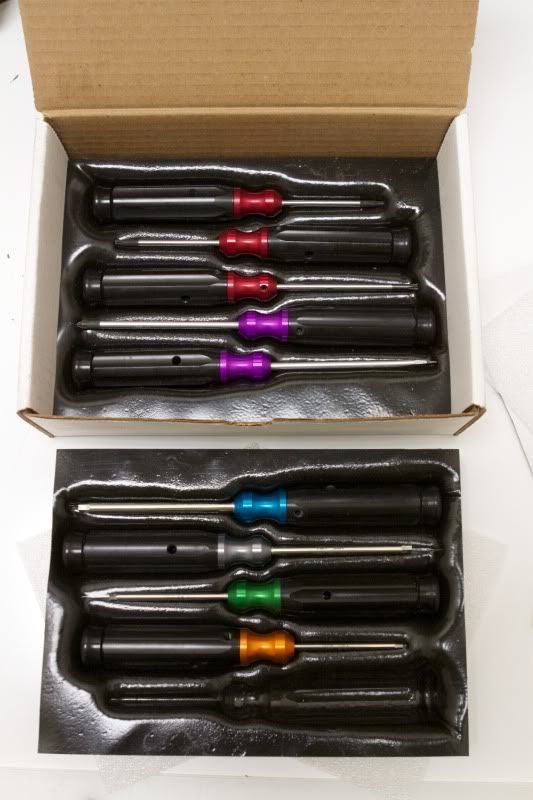
The four hex drivers: 2.5mm, 3.0mm, 4.0mm, 5.0mm
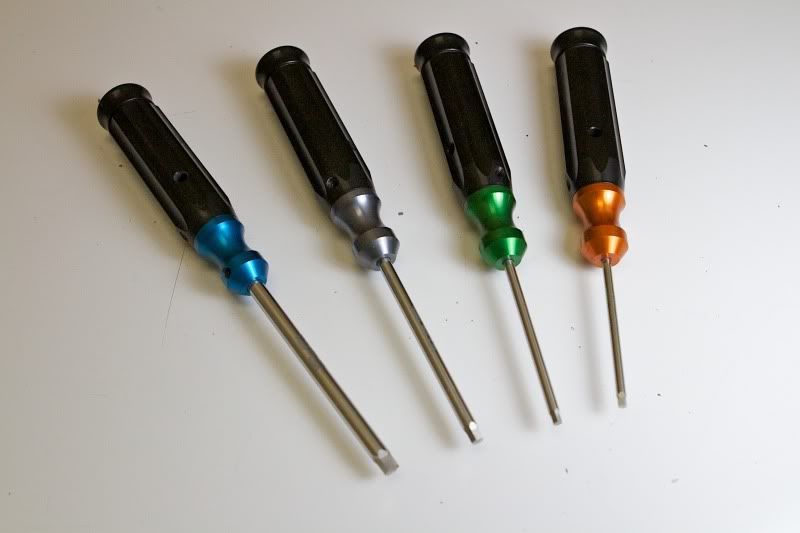
The five additional drivers: Phillips, Slotted, T10, T15, T20
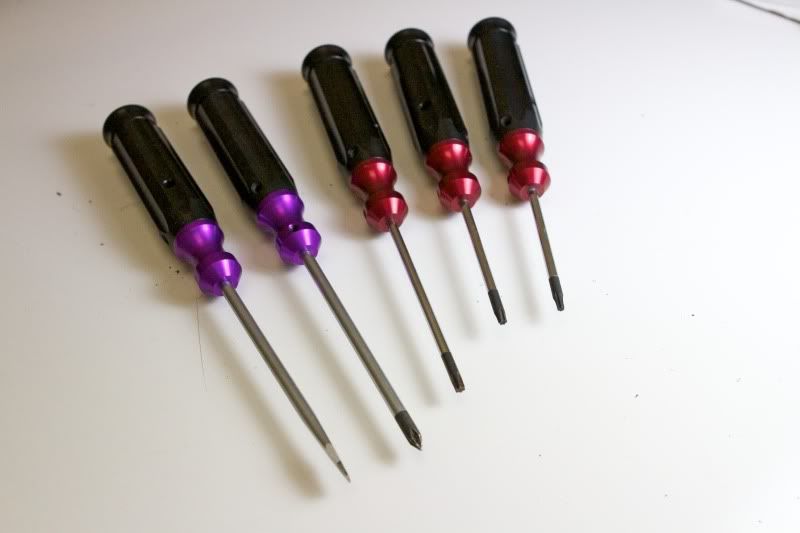
All nine drivers in the kit
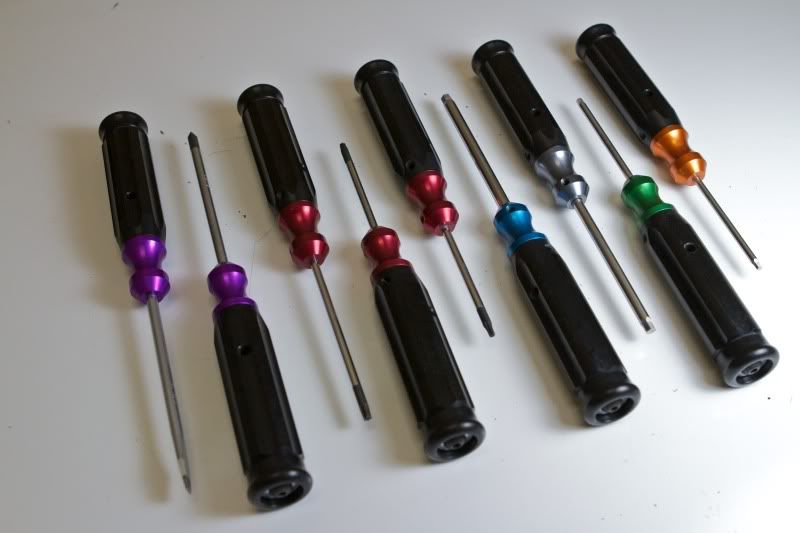
Here is the vacuum formed insert that I roughed out
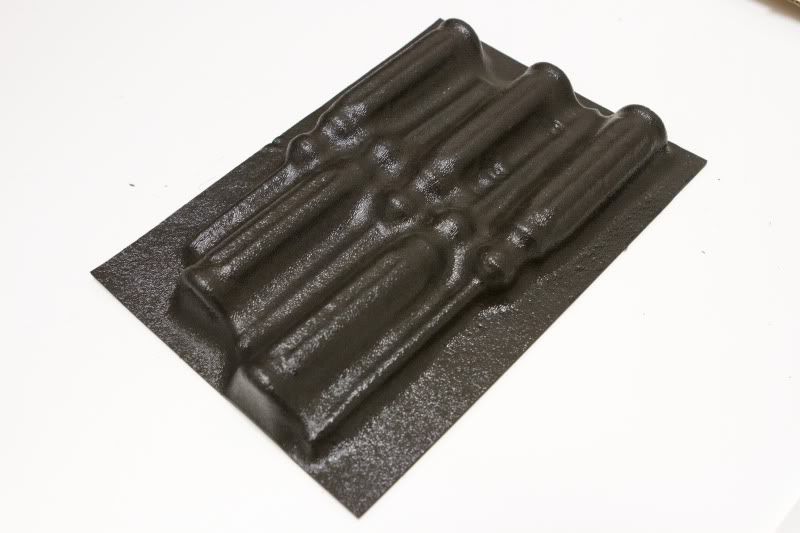
Driver neatly tucked away in the insert.

The following images are some examples of where the drivers might be used
Using the 2.5mm Hex Driver
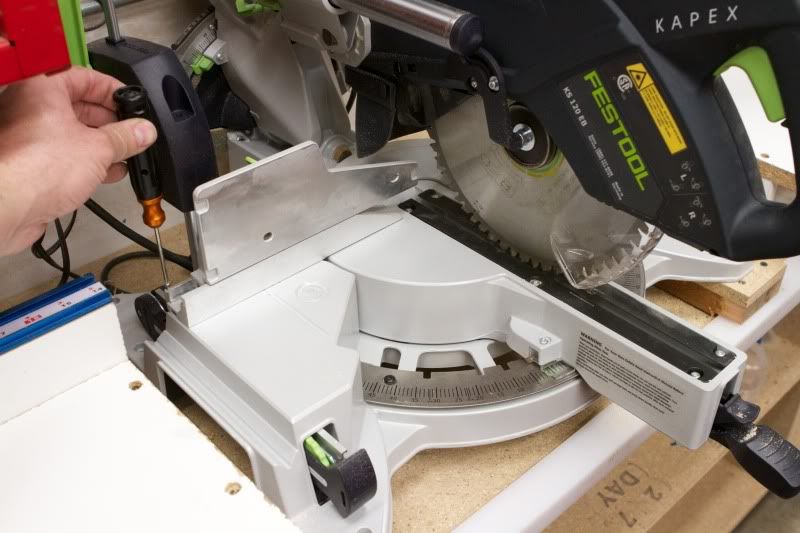
Using the 3.0mm Hex Driver
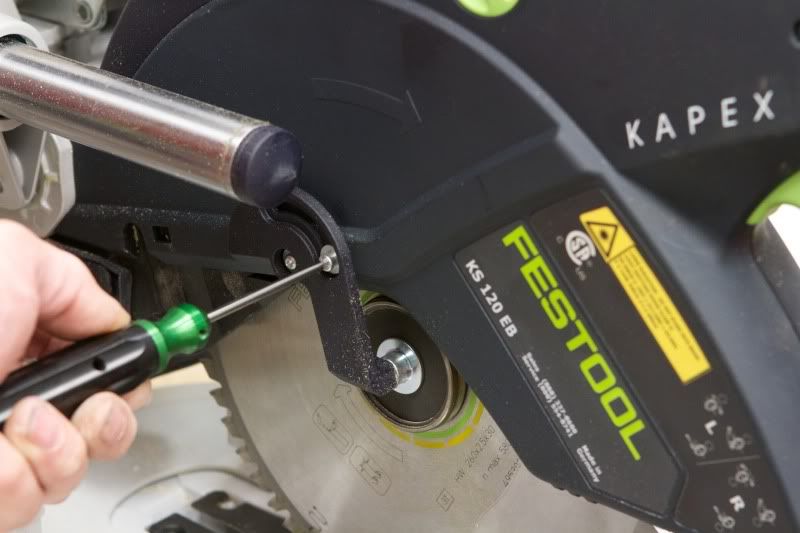
Using the T20 Driver
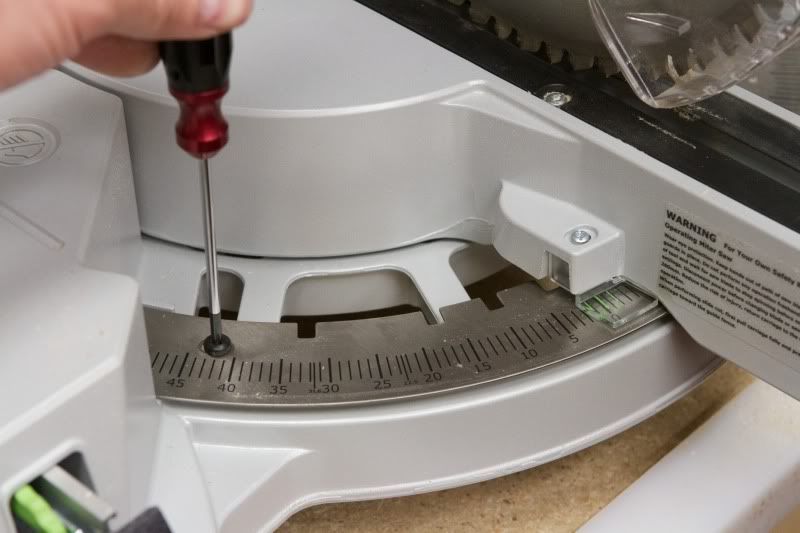
Using the T15 Driver
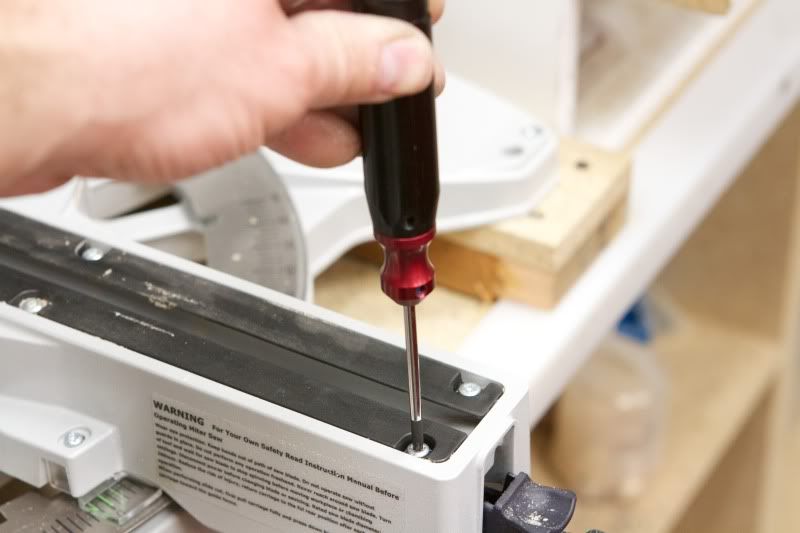
Using the T10 Driver
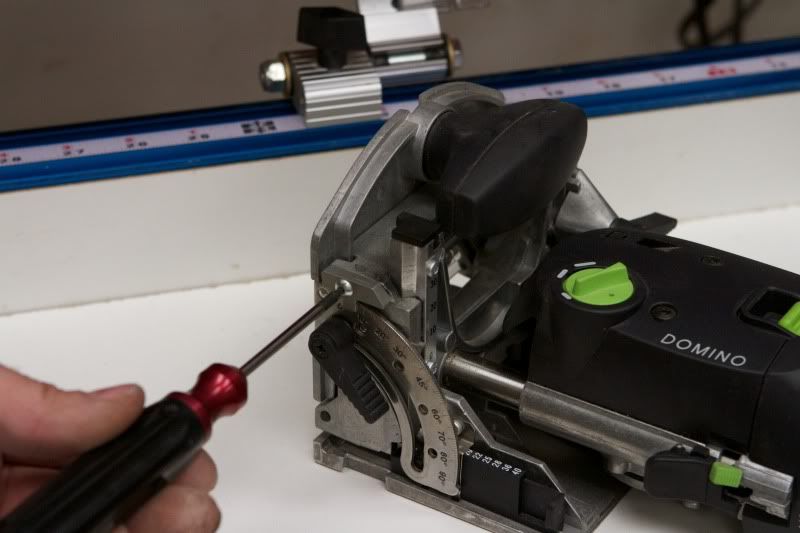
Using the 4.0mm Hex Driver
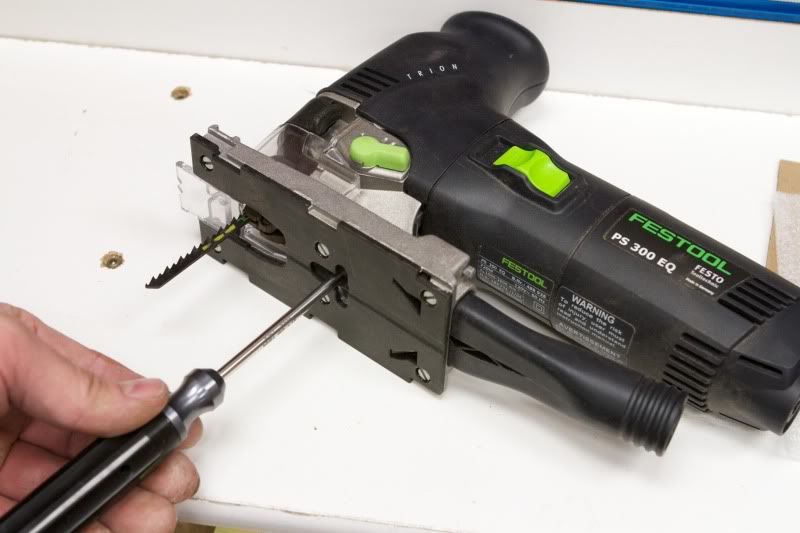
Using the Slotted Driver
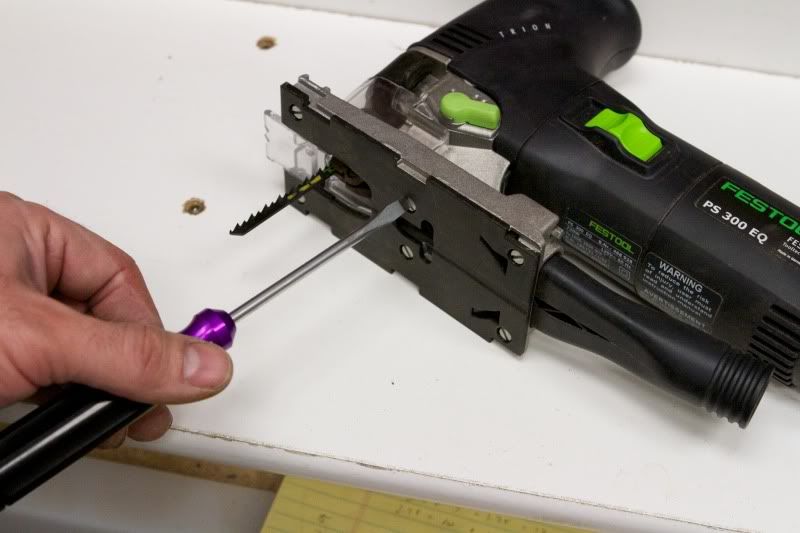
Using the Phillips Driver
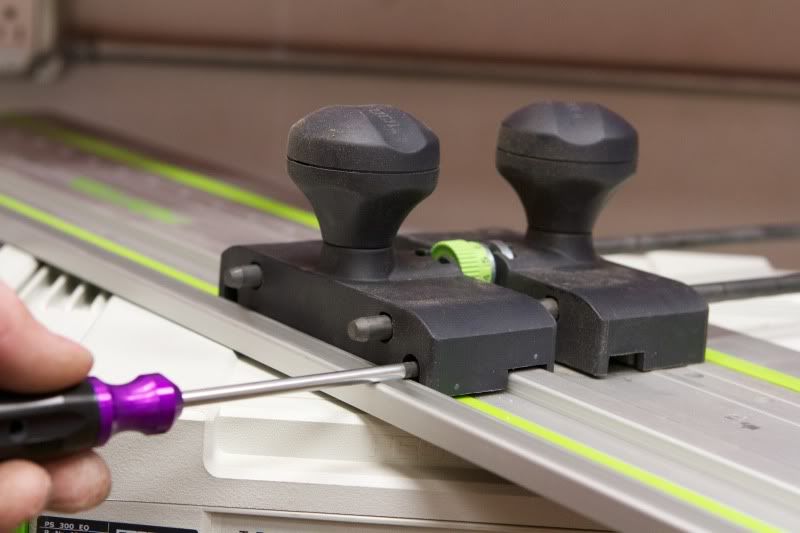
I guess that is it for know until I start playing around with more custom inserts and getting these drivers into a systainer or ministainer.
Thanks