As I continue organizing my shop, moving things from the garage down into the basement, storage becomes a higher priority. The shop is only 11' x 17', so it's tight but doable. I finally moved my workbench into it this week and now find it would be nice to have more items downstairs and avoid running up to the garage to retrieve things.
I took some ideas from Frank Howarth's videos on his office cleat wall and decided that would be great for the shop. I wanted to avoid simply screwing things here and there on walls, changing my mind and leaving holes everywhere. I've used up a bunch of scrap plywood I've had from previous projects and built the first wall section. It's simply 1/2" plywood with 3/4" French cleats. The 1/2" ply is screwed to the wall studs. All the hangers are 3/4" plywood. The intent is to easily move things around as needed.
First off: clamps. Although I don't own a ton of clamps, the ones that I have are where ever I can fit them in the garage. The pipe clamps are the only ones actually hanging, the remainder are placed under benches. All the clamp hangers came from ideas found on a Woodcraft website. Each holder accommodates six clamps. The pipe clamps and others I own can remain hanging in the garage for now.
Next up: Woodpeckers tools. The only item that has ever been hanging in its holder is the 1281. Everything else has been under the workbench. I simply attached French cleats to the back of the Woodpecker fixtures and made dowel hangers for the TS-3 and TS-6 and the rulers.
This is only wall storage location #1. I intend to build a lot more of these and right now, it's holding clamps and Woodpeckers gear. I anticipate that this area will be used for all clamps, the Woodpeckers gear will get moved over the workbench. This took only a few hours to put together and as I need holders, it's easy to knock one together. This section is all of 28" x 48".
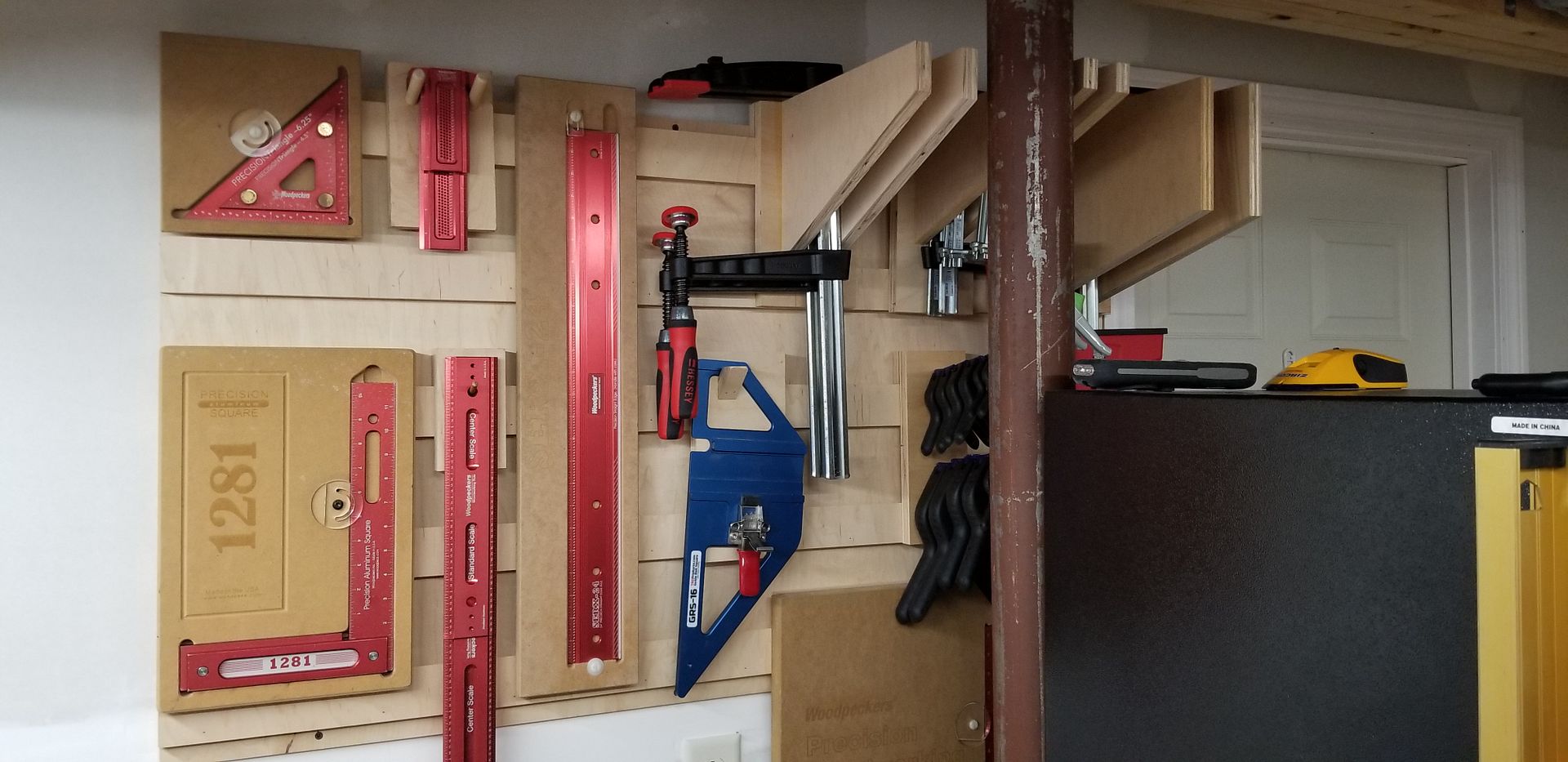
And from the other side -
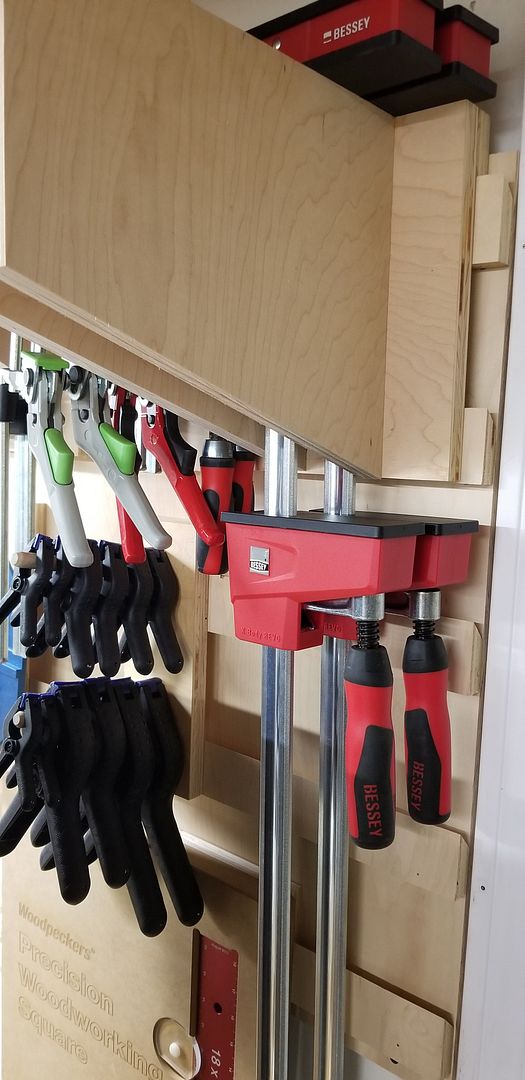
I'm amazed at how useful this system has already turned out to be. I intend to build some storage containers, bins, whatever. All depends on what is needed and how much scrap ply I have on hand.
Regards,
-Dom
I took some ideas from Frank Howarth's videos on his office cleat wall and decided that would be great for the shop. I wanted to avoid simply screwing things here and there on walls, changing my mind and leaving holes everywhere. I've used up a bunch of scrap plywood I've had from previous projects and built the first wall section. It's simply 1/2" plywood with 3/4" French cleats. The 1/2" ply is screwed to the wall studs. All the hangers are 3/4" plywood. The intent is to easily move things around as needed.
First off: clamps. Although I don't own a ton of clamps, the ones that I have are where ever I can fit them in the garage. The pipe clamps are the only ones actually hanging, the remainder are placed under benches. All the clamp hangers came from ideas found on a Woodcraft website. Each holder accommodates six clamps. The pipe clamps and others I own can remain hanging in the garage for now.
Next up: Woodpeckers tools. The only item that has ever been hanging in its holder is the 1281. Everything else has been under the workbench. I simply attached French cleats to the back of the Woodpecker fixtures and made dowel hangers for the TS-3 and TS-6 and the rulers.
This is only wall storage location #1. I intend to build a lot more of these and right now, it's holding clamps and Woodpeckers gear. I anticipate that this area will be used for all clamps, the Woodpeckers gear will get moved over the workbench. This took only a few hours to put together and as I need holders, it's easy to knock one together. This section is all of 28" x 48".
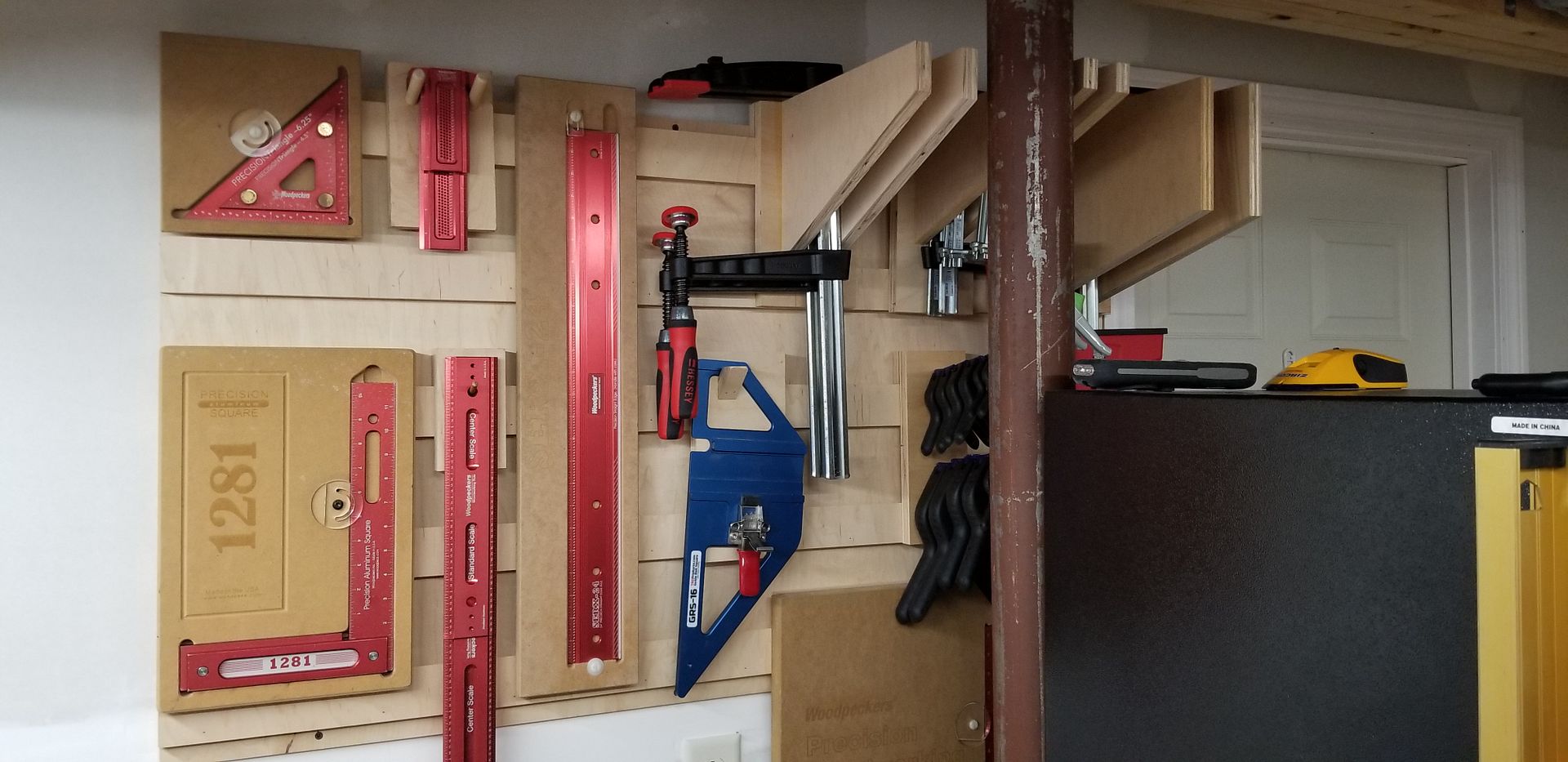
And from the other side -
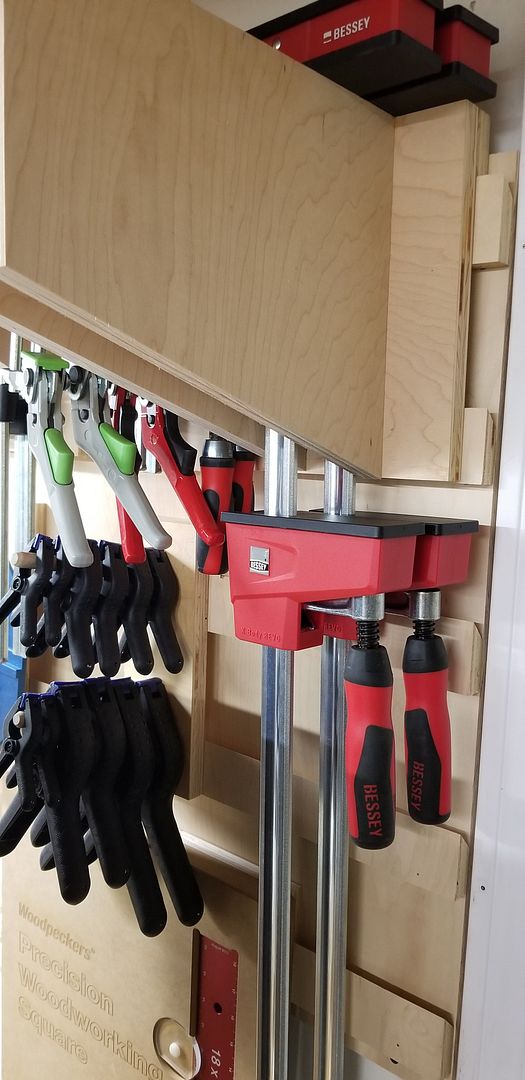
I'm amazed at how useful this system has already turned out to be. I intend to build some storage containers, bins, whatever. All depends on what is needed and how much scrap ply I have on hand.
Regards,
-Dom