Bugsysiegals
Member
- Joined
- Mar 19, 2016
- Messages
- 909
I see the TSO GRS-16 PE shown attached to the guide rail on a MFT/3 table to square the guide rail which is cool but they do not have the parallel guide rail connected in the images. Can it be connected so that in addition to square cuts on the MFT/3 you have a fence with rule?
This seems huge as you don’t need the fence to be square to the table, tightened down in a way so it has no deflection, and can produce perfectly measured square cuts immediately even if you decide to slide the guide rail Left/Right to make a new zero clearance in the MFT/3 table.
This seems huge as you don’t need the fence to be square to the table, tightened down in a way so it has no deflection, and can produce perfectly measured square cuts immediately even if you decide to slide the guide rail Left/Right to make a new zero clearance in the MFT/3 table.
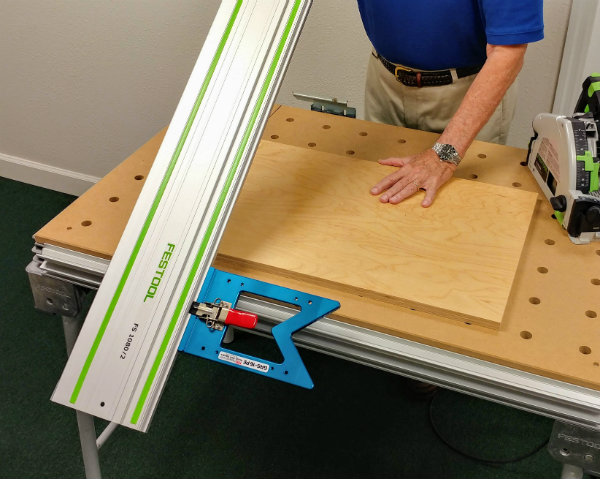
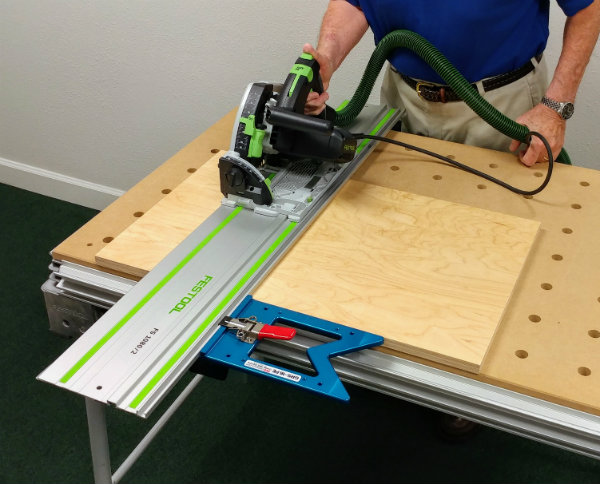