sebcbien
Member
- Joined
- Aug 5, 2014
- Messages
- 49
Hello, I had to joint 2m long stock and only had a small jointer.
I searched the web and found the kind of jig to joint on the table saw like this one:
I scratched my head a little more and bought a long aluminium rectangular tube like this one:
It's strong and doesn't bend easily.
I made 3 holes in it and clamped to my CS 70 fence.
Now I have a longer reference fence and I can joint 2m long stock the easy way.
I made some tests and it works very well.
Maybe I miss something because I didn' find this trick anywhere on internet.
any objection on this solution ?
View attachment 1
I searched the web and found the kind of jig to joint on the table saw like this one:
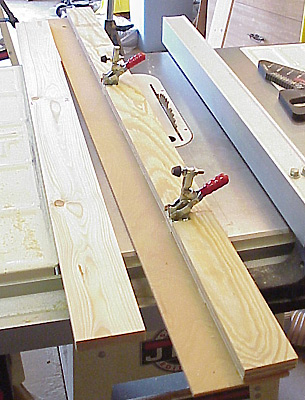
I scratched my head a little more and bought a long aluminium rectangular tube like this one:

It's strong and doesn't bend easily.
I made 3 holes in it and clamped to my CS 70 fence.
Now I have a longer reference fence and I can joint 2m long stock the easy way.
I made some tests and it works very well.
Maybe I miss something because I didn' find this trick anywhere on internet.
any objection on this solution ?
View attachment 1