And in the interest of full disclosure and transparency, I also spent the weekend fixing my 3 domino boo boos....
My biggest complaint about the domino is that it makes easy to work too fast and make "stupid mistakes", or as Coach Mctaggert used to tell us in high school "mental errors".....
On two of the legs, I made domino cuts that should have been on the narrow setting, but forgot to change if from "wide". Pictures below show my approach to fixing that (not crucial, but these were the "positioning" dominos that make glue up easier for alignment.
I also managed to START cutting on one leg when I forgot to change the depth from 1/2" to 1 3/8"....

. I had originally decide to make that location for my custom nameplate to be installed, then remembered "I'm a luthier, damnit! I can fix that like an inlay and make it almost invisible!" So.... I measured the opening and modeled a domino inlay to those exact dimensions, then I duplicated to total of 9, and wrote a CAM program in Fusion 360 where each was cut with increasing and decreasing "stock to leave" values, incrementing .001 Inch (.03 mm) at a time. One of those had to be a tight fit! I numbered them after they were cut as to which was which, and used the drum sander to sand away the backing stock, turns out that the .001" offset (total of 2 thousandths under) was the one (which is my basic rule of thumb on inlay fits unless they're very complicated. Pictures below!
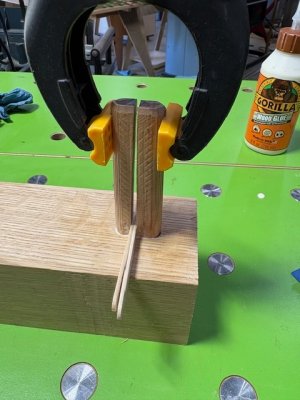
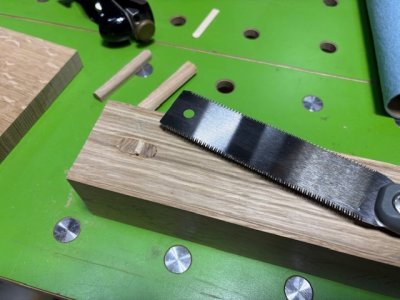
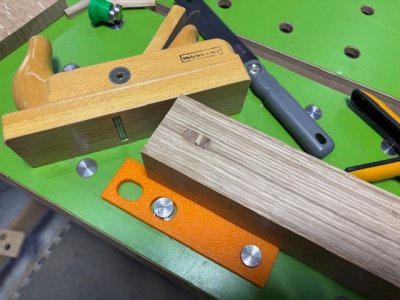
