derekcohen
Member
- Joined
- Jun 22, 2008
- Messages
- 963
I have been happy in the past to use a block plane to chamfer edges. I once built a bevel up chamfer plane, but it required resetting the depth of cut each time, and it just became too much work.
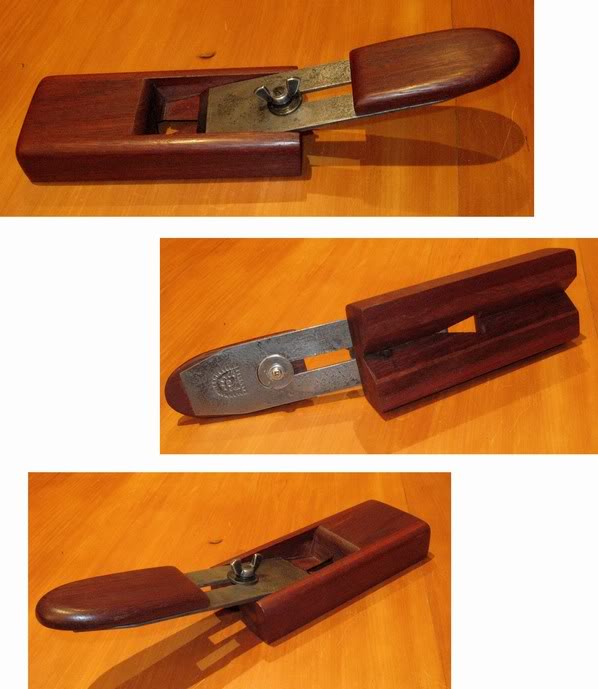
Then I purchased a well-used Japanese chamfer plane. This has an adjustable carriage for the blade. The adjustable carriage slides side-to-side to offer a fresh edge once the used edges dulls.
Mine lacked the chipbreaker (I made one from wood) and the carriage was loose (so I added a shim), and it all worked reasonably well to form even chamfers on show edges. I cannot say that I was in love with it - it felt a little Heath Robinson, and I knew that I needed to either restore it properly or accept its quirks.
On a bit of a whim, I decided to purchase a chamfer plane made by my old New Zealand friend, Philip Marcou. And I am so glad that I did so as it is easy to use, reliable, and produces a great chamfer. His is based on the Japanese design but somewhat cheaper. From Pirana Tool in NZ: https://piranhatools.co.nz/products/philip-marcou-chamfering-plane Morre details in this link.
110mm in length, with a blade with of 18.5mm and 3mm thick (although I did find the original blade too short for my liking, and made another that was about 10mm longer) ...
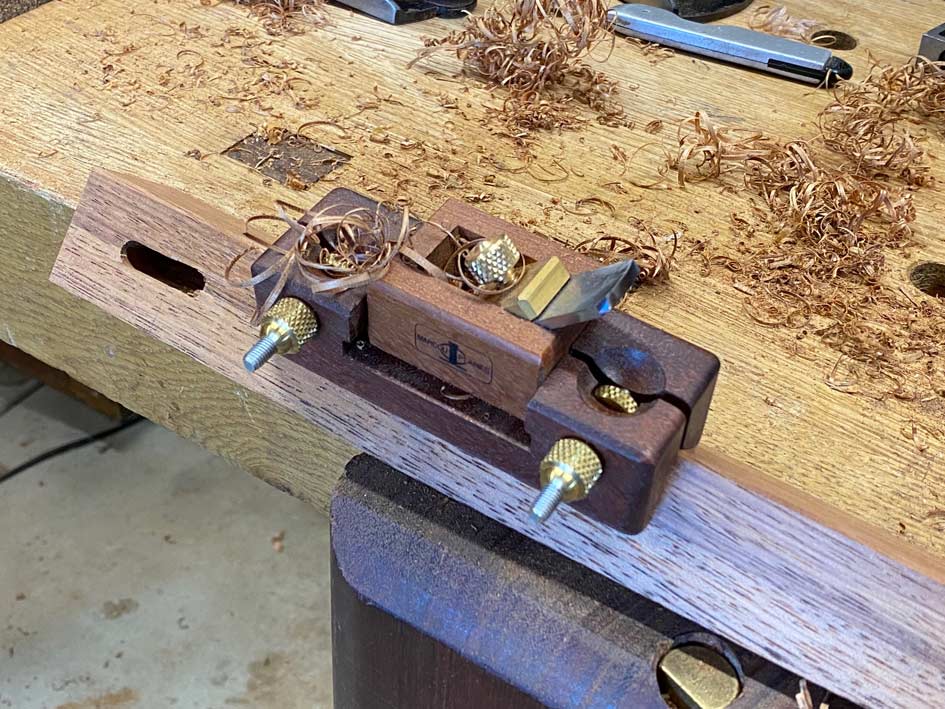
Here it is against the Japanese version. You can see how compact the Marcou is ...
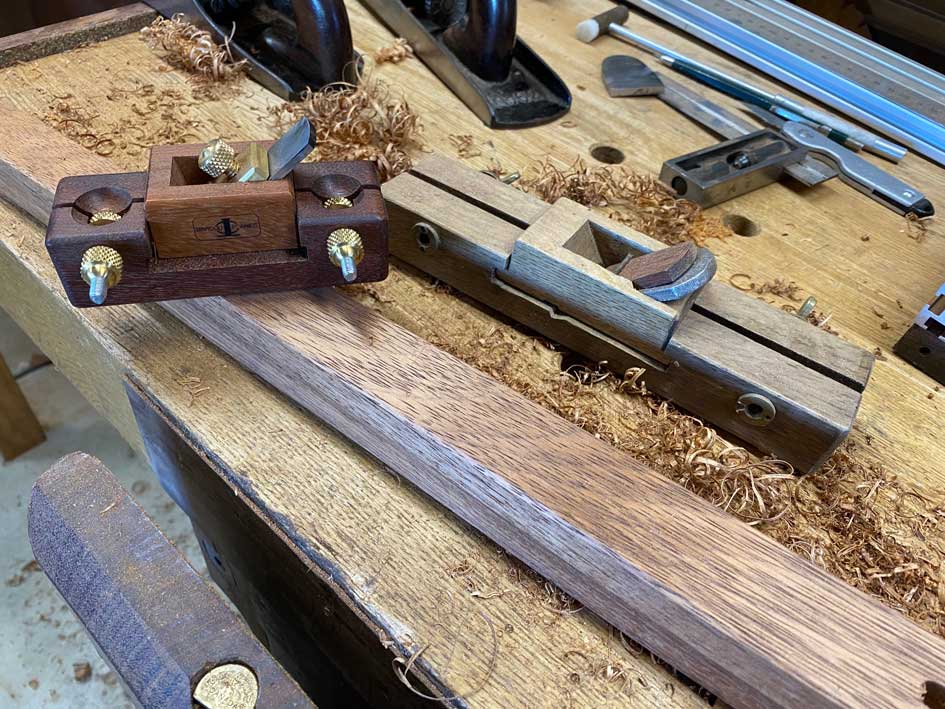
It worked flawlessly and the small size just nestles nicely in the palm. It cuts to depth and then stops cutting, which ensures all chamfers are exactly the same.
Twelve legs ...
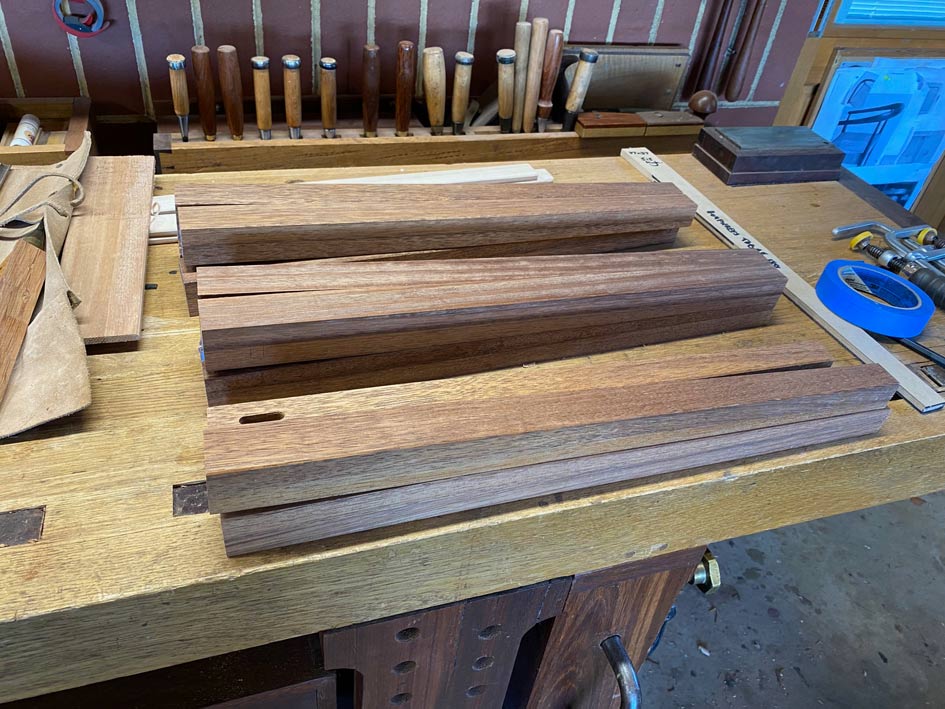
... for three bedside tables (in progress) ...
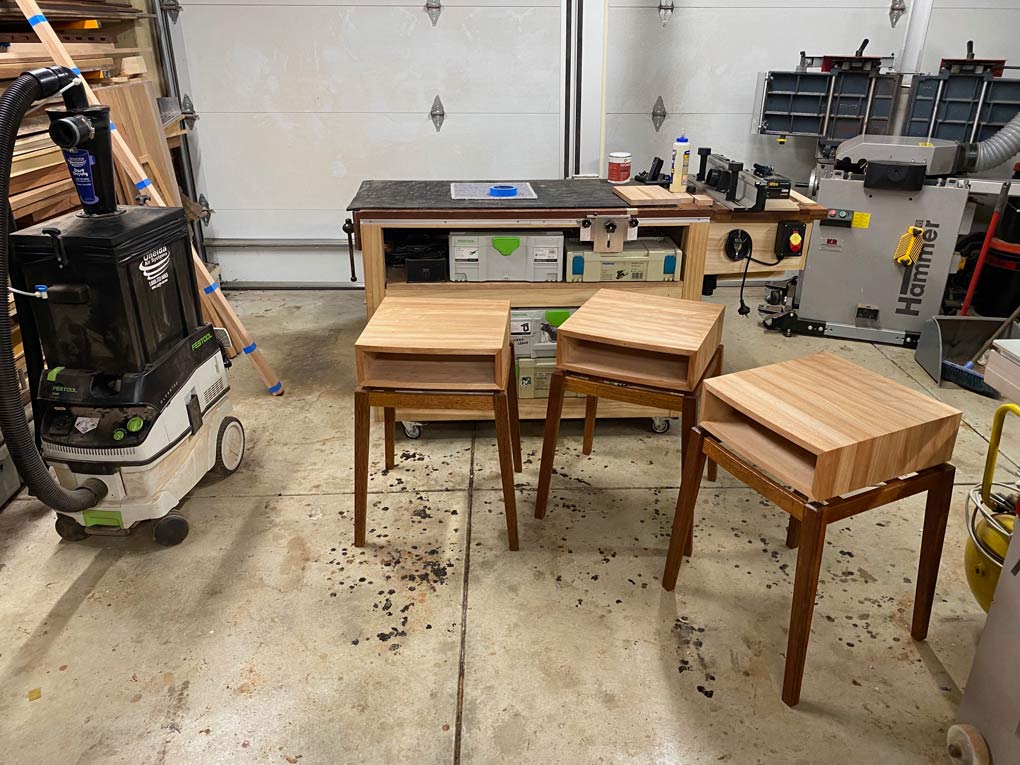
Regards from Perth
Derek
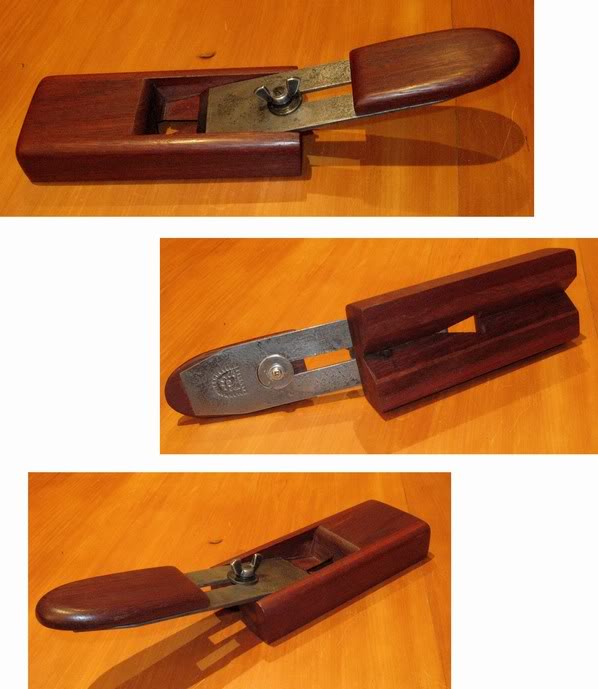
Then I purchased a well-used Japanese chamfer plane. This has an adjustable carriage for the blade. The adjustable carriage slides side-to-side to offer a fresh edge once the used edges dulls.
Mine lacked the chipbreaker (I made one from wood) and the carriage was loose (so I added a shim), and it all worked reasonably well to form even chamfers on show edges. I cannot say that I was in love with it - it felt a little Heath Robinson, and I knew that I needed to either restore it properly or accept its quirks.
On a bit of a whim, I decided to purchase a chamfer plane made by my old New Zealand friend, Philip Marcou. And I am so glad that I did so as it is easy to use, reliable, and produces a great chamfer. His is based on the Japanese design but somewhat cheaper. From Pirana Tool in NZ: https://piranhatools.co.nz/products/philip-marcou-chamfering-plane Morre details in this link.
110mm in length, with a blade with of 18.5mm and 3mm thick (although I did find the original blade too short for my liking, and made another that was about 10mm longer) ...
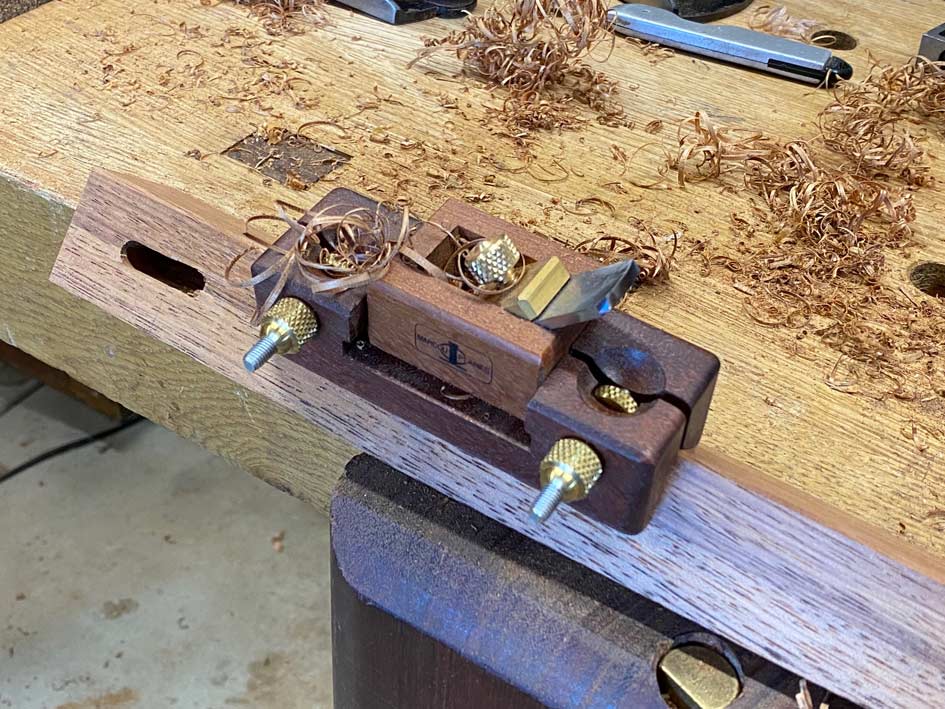
Here it is against the Japanese version. You can see how compact the Marcou is ...
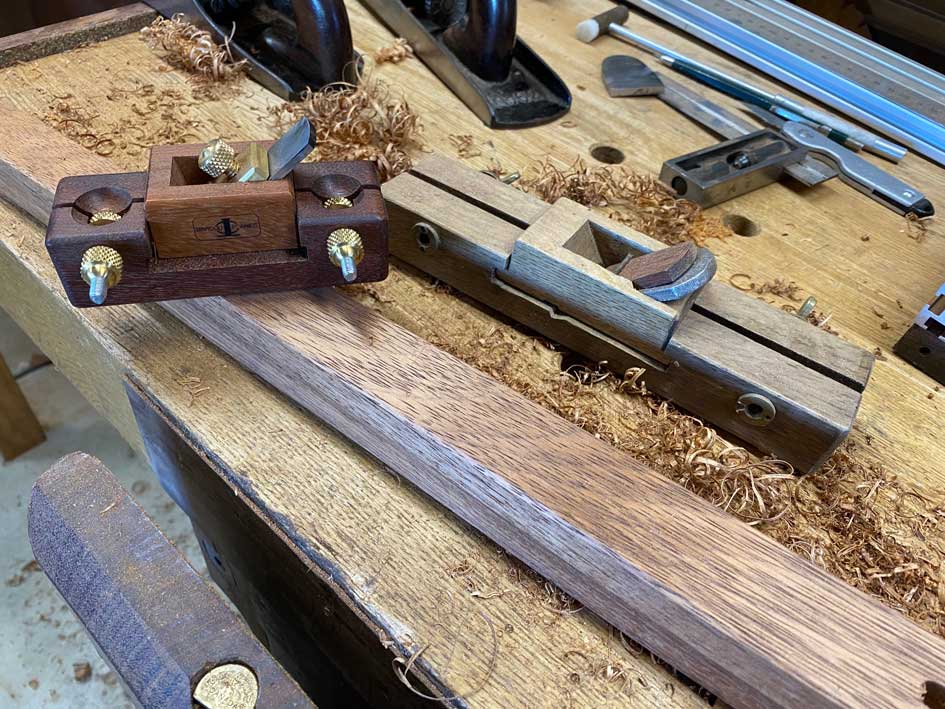
It worked flawlessly and the small size just nestles nicely in the palm. It cuts to depth and then stops cutting, which ensures all chamfers are exactly the same.
Twelve legs ...
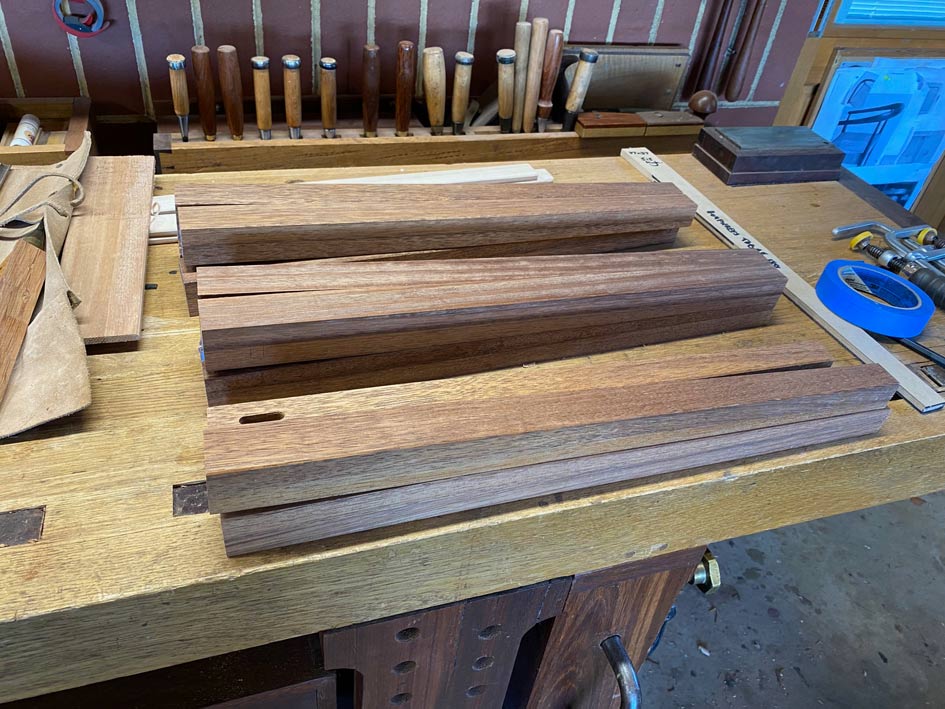
... for three bedside tables (in progress) ...
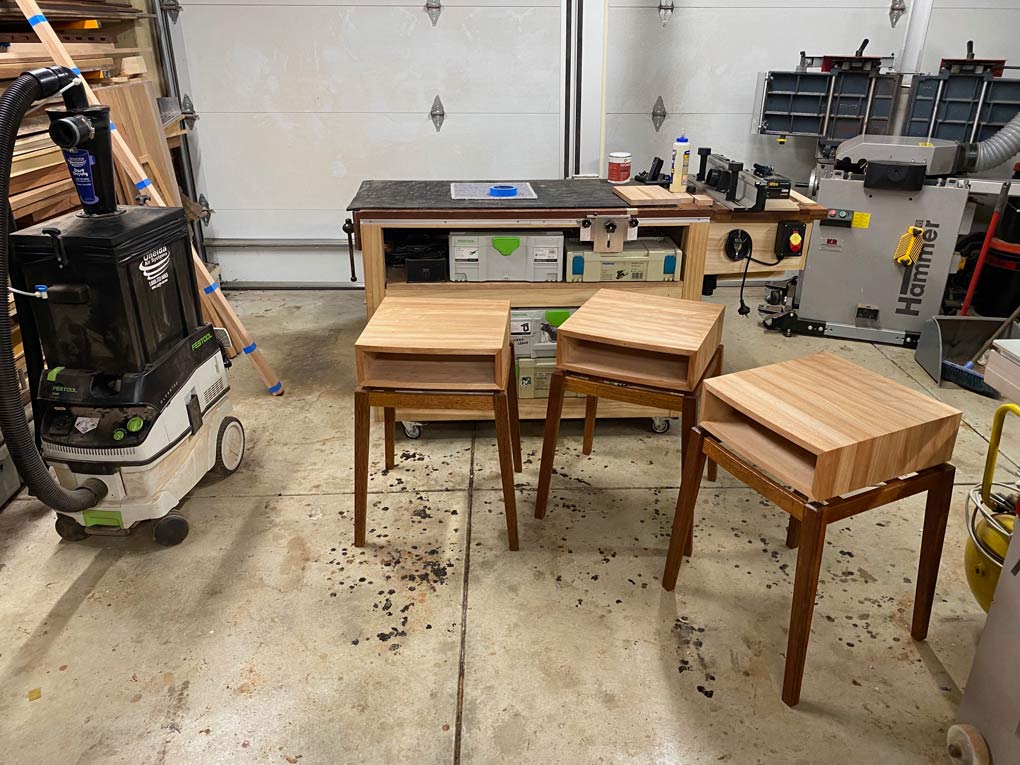
Regards from Perth
Derek