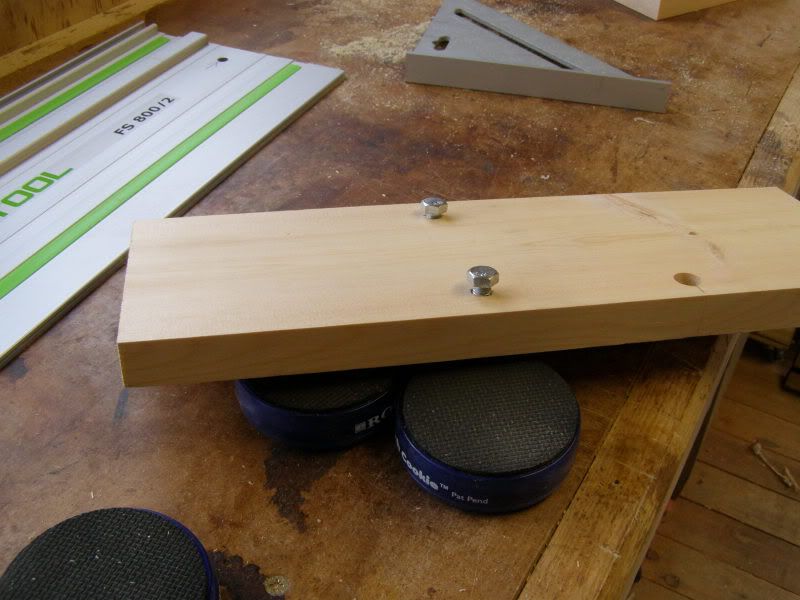
Ok it's a 6x1" pine PAR with two M8x30 bolts. Obviously the bolt holes where put in square to the face.
The arrows show which direction the saw cuts in,for us beginners, helps when rails upside down. I've got arrows on both sides of all my rails.
For us daft ones. [tongue]
So loosen bolts slide jig bolts into bottom of rail, square as below and just nip up bolts so as non slip foam tape grips jig and you're ready to go.
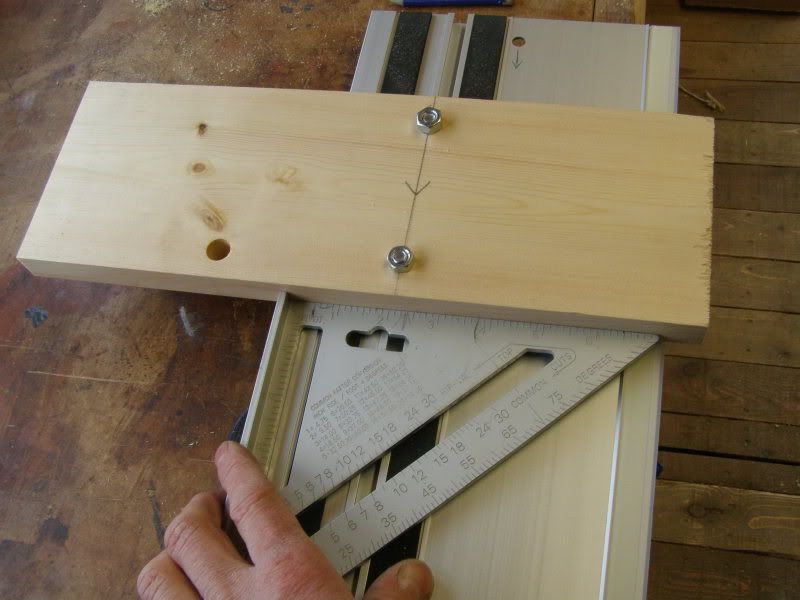
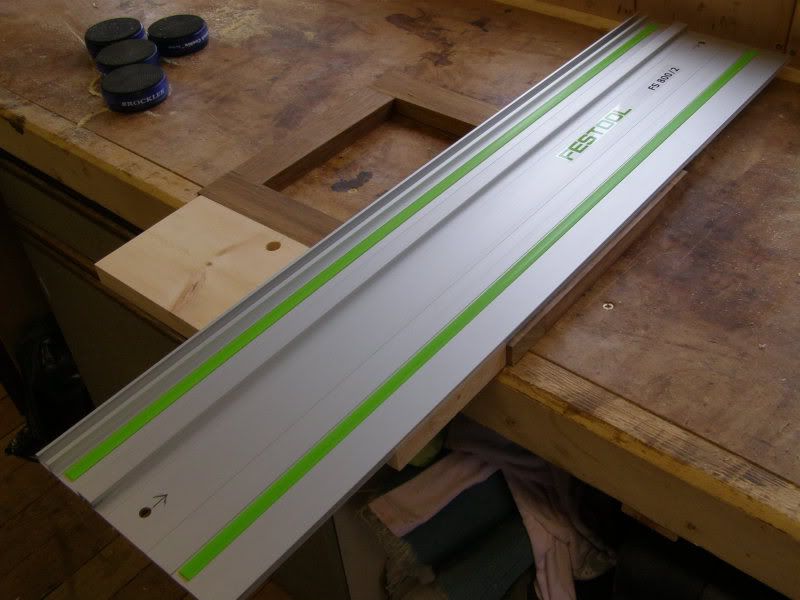
And it's custom built to fit in the box with the saw. [tongue]
I've used the jig quite a bit on site last week, really came into it's own and stayed 100% square even after a few knocks.
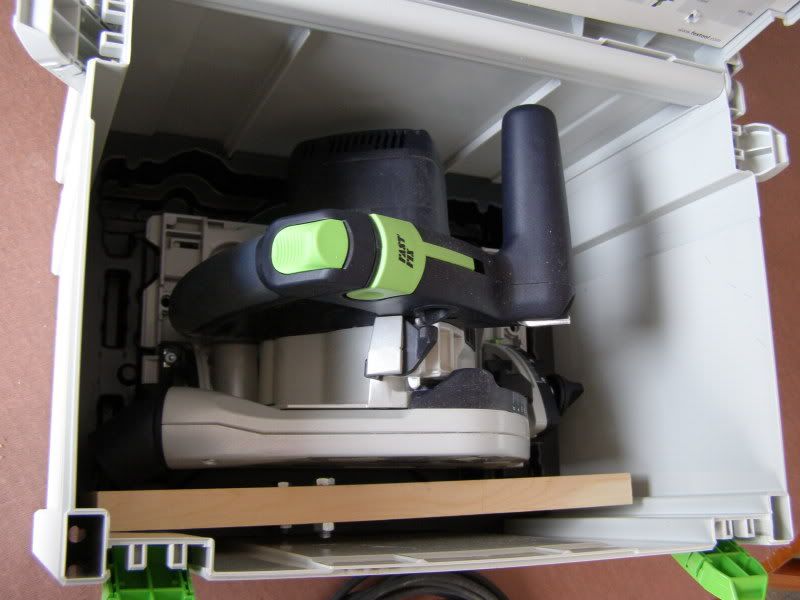
Improvements can definitely be made, I'm thinking 45 deg bolt hole maybe variable and definitely a longer ones for repeat parallel cuts with stops.