Brice_Arnold
Member
- Joined
- May 22, 2011
- Messages
- 105
Short story long; I was trying to use my Festool routers with my Leigh dovetail jig and was running in to a couple of problems. I tried using both an OF 1010 router and an OF 1400 router with the Leigh jig and ran into problems with both routers. In the past I have used Dewalt routers for the Leigh jig without issue.
The first was with the guide busing. You have to be able to center the guide busing with respect to the router bit. You can not do this with the guide busing adapters for both Festool routers. This relation is fixed and they are not even close to being centered (visible with the naked eye). I tried capturing the misalignment with my point-and-shoot.
The other issue I had with the festool routers is that the bottoms are not "flat" there are features/inserts that are at different elevations to the base. When you try using these routers with the Leigh jig, the router rocks around and gets snagged on the dovetail template fingers. This makes for a poor dovetail joint on the Leigh jig.
Here are some images of the OEM Festool bases
OF 1010
OF 1400
I don't know if Festool has a solution for these issues, and a quick search did not yield optional base plates. I decided to design my own base plate that would take a standard Porter Cable style guide bushing, be mostly monolithic and flat, and offer oversized counter bored mounting holes for alignment of the guide busing to the router bit. The hardest part in this little project was reverse engineering the hole pattern on the bottom of the Festool routers. The pattern on the OF 1010 seems random. The pattern on the OF 1400 was at least rectangular. My material of choice was 6mm Lexan (polycarbonate). This is durable material and not as brittle as acrylic.
Here is what I came up with. Simple yet effective.
OF 1010
OF 1400
The OF 1400 also has a center ring for the quick release Festool guide bushings. I had to machine a pocket in the base plate to clear this feature
Here are the base plates installed with a guide bushing.
OF 1010
OF 1400
Hopefully this weekend I can try out these routers on the Leigh dovetail jig with better success.
Thanks for looking
The first was with the guide busing. You have to be able to center the guide busing with respect to the router bit. You can not do this with the guide busing adapters for both Festool routers. This relation is fixed and they are not even close to being centered (visible with the naked eye). I tried capturing the misalignment with my point-and-shoot.
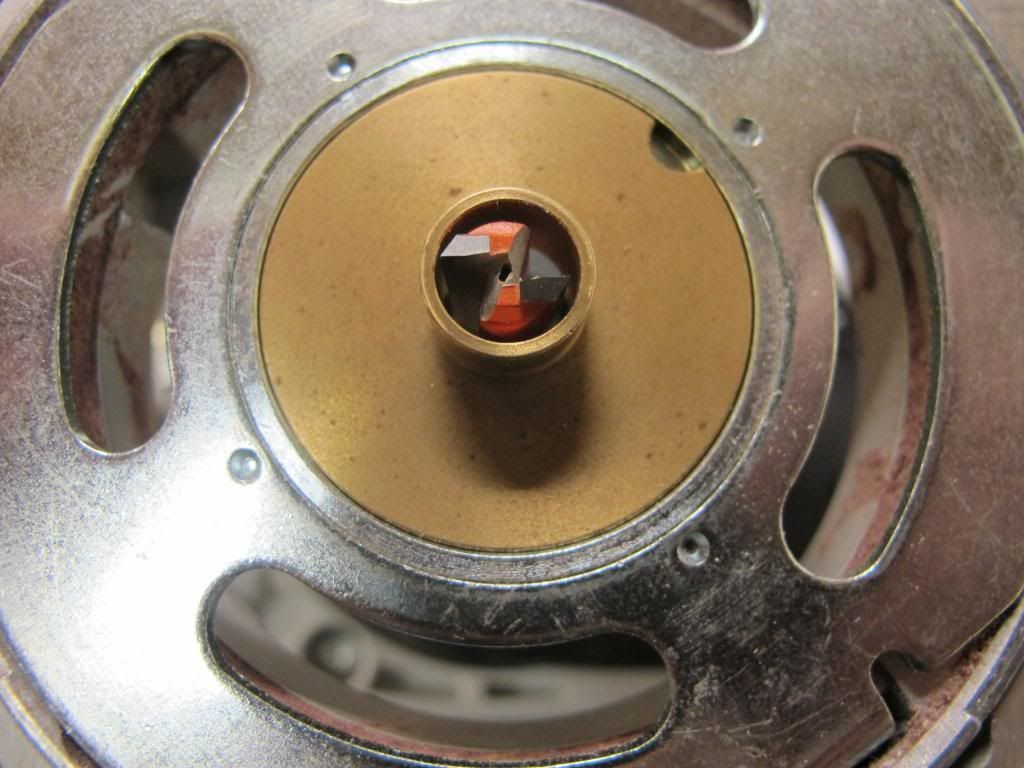
The other issue I had with the festool routers is that the bottoms are not "flat" there are features/inserts that are at different elevations to the base. When you try using these routers with the Leigh jig, the router rocks around and gets snagged on the dovetail template fingers. This makes for a poor dovetail joint on the Leigh jig.
Here are some images of the OEM Festool bases
OF 1010
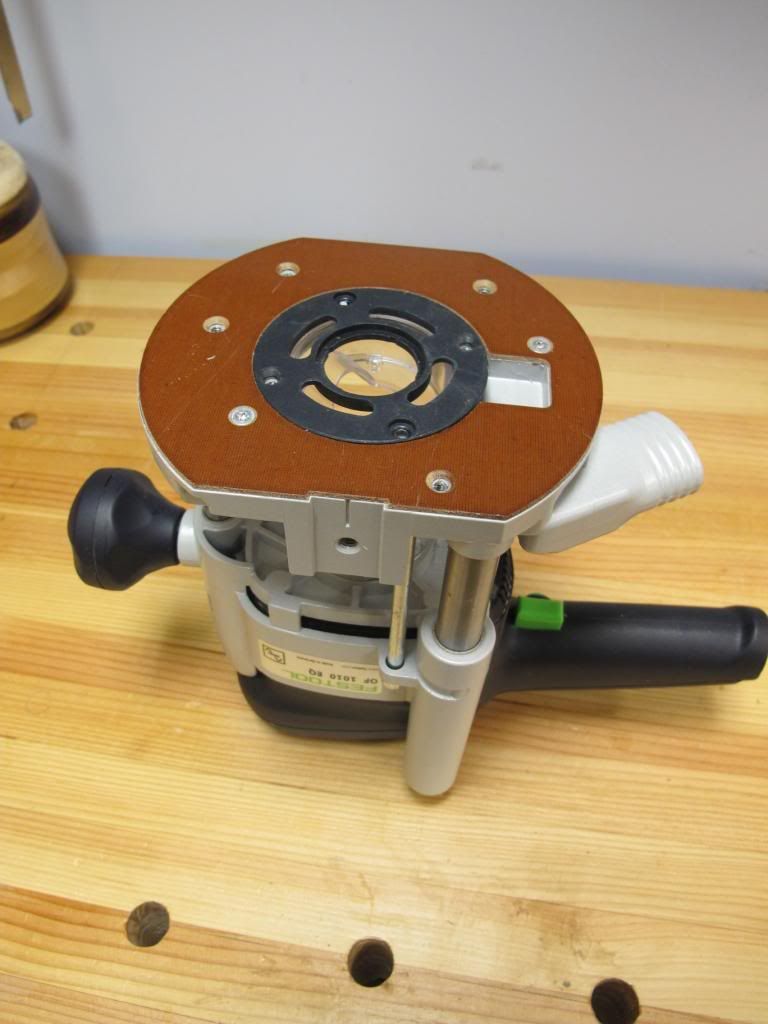
OF 1400
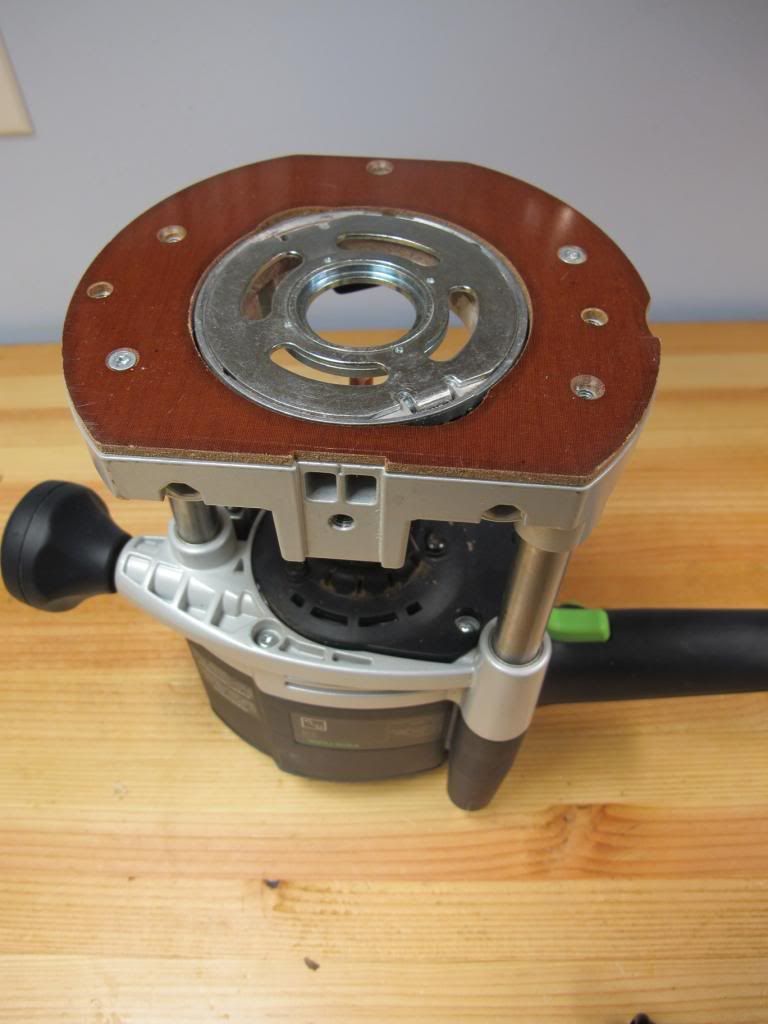
I don't know if Festool has a solution for these issues, and a quick search did not yield optional base plates. I decided to design my own base plate that would take a standard Porter Cable style guide bushing, be mostly monolithic and flat, and offer oversized counter bored mounting holes for alignment of the guide busing to the router bit. The hardest part in this little project was reverse engineering the hole pattern on the bottom of the Festool routers. The pattern on the OF 1010 seems random. The pattern on the OF 1400 was at least rectangular. My material of choice was 6mm Lexan (polycarbonate). This is durable material and not as brittle as acrylic.
Here is what I came up with. Simple yet effective.
OF 1010
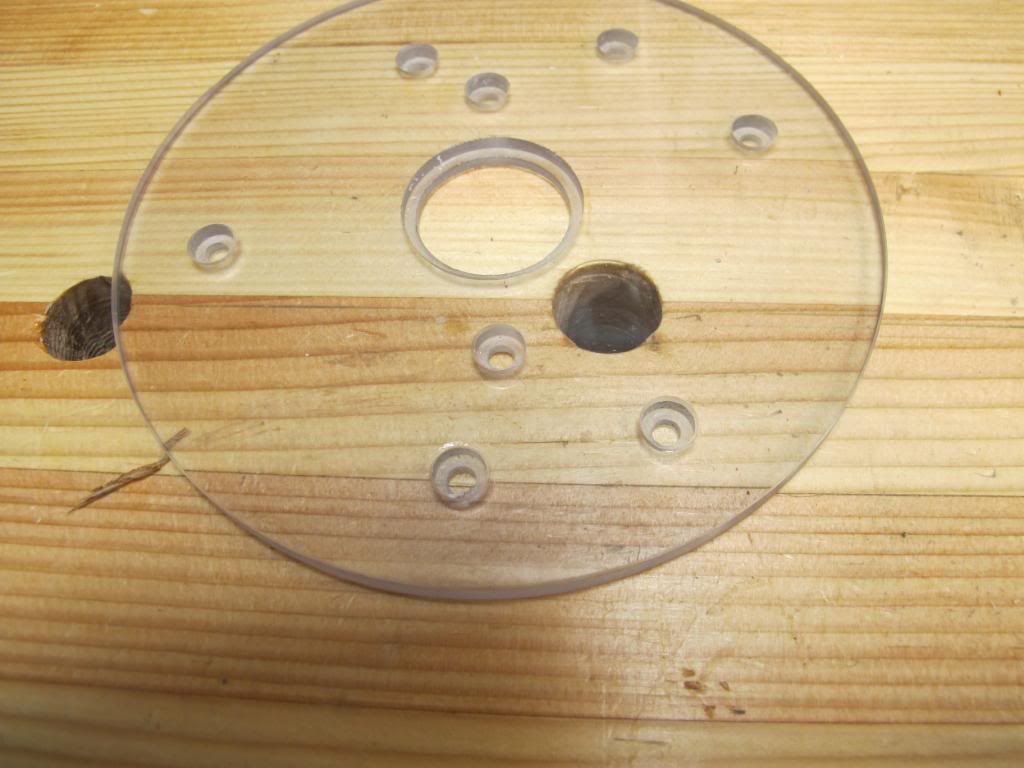
OF 1400
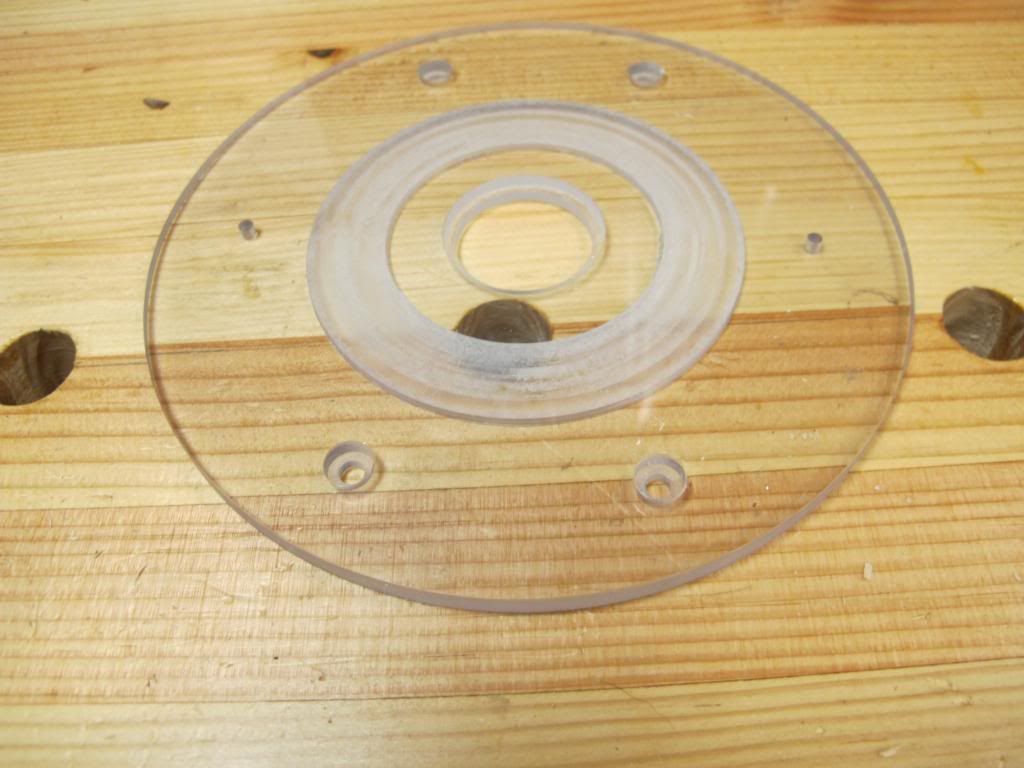
The OF 1400 also has a center ring for the quick release Festool guide bushings. I had to machine a pocket in the base plate to clear this feature
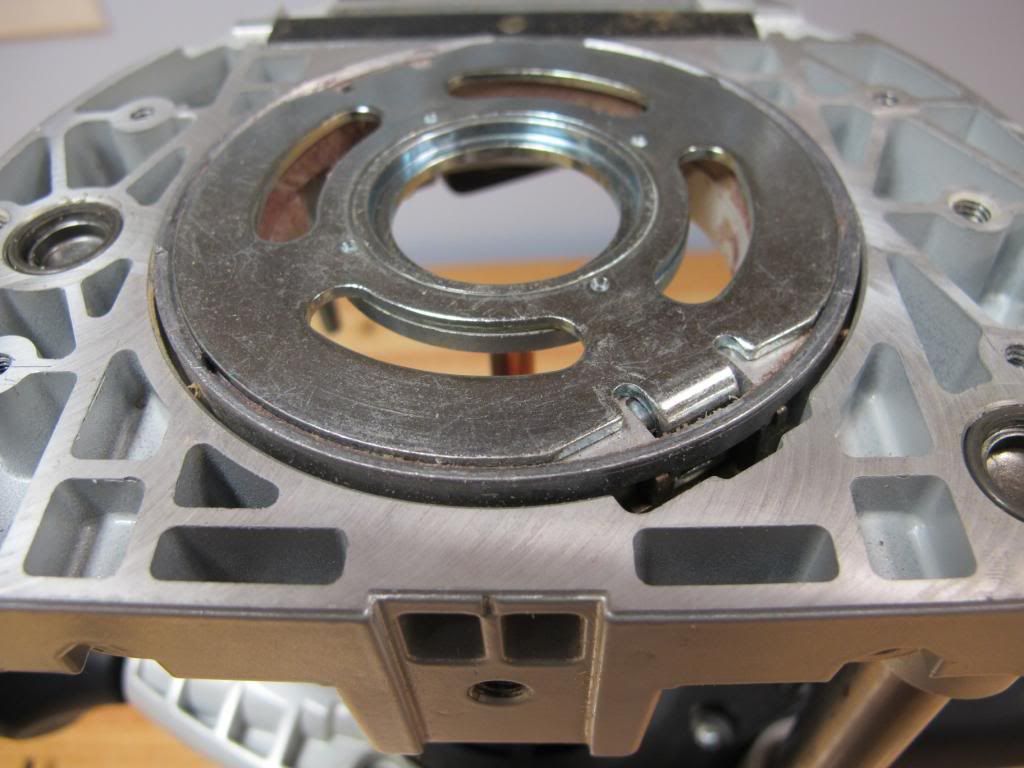
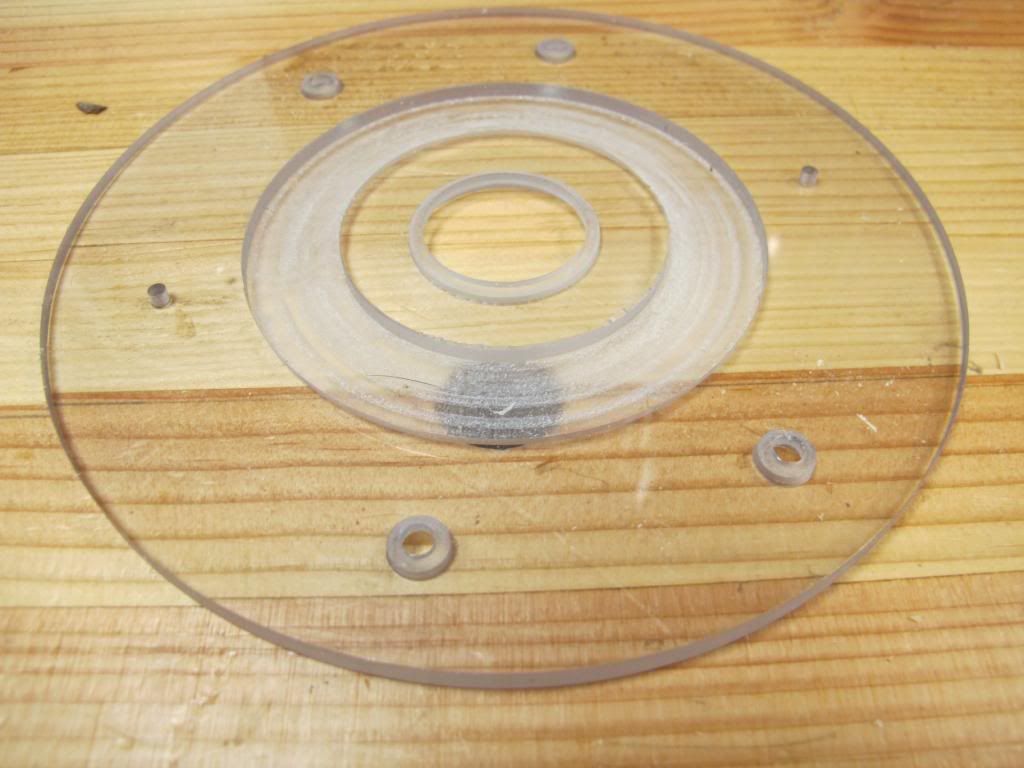
Here are the base plates installed with a guide bushing.
OF 1010
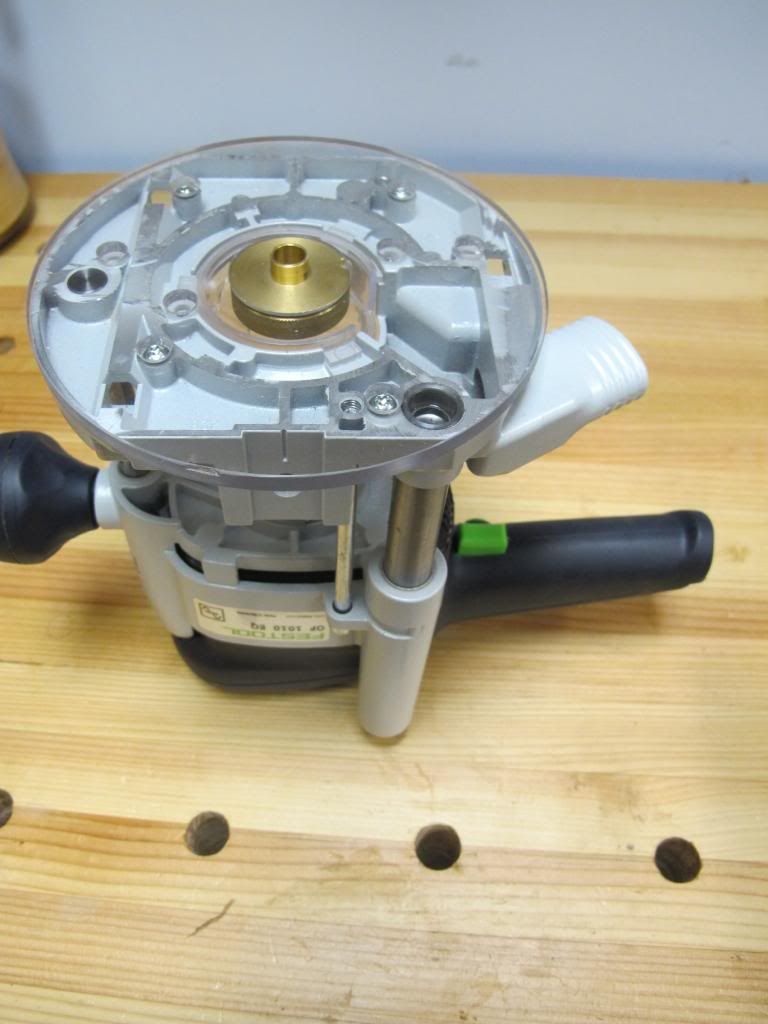
OF 1400
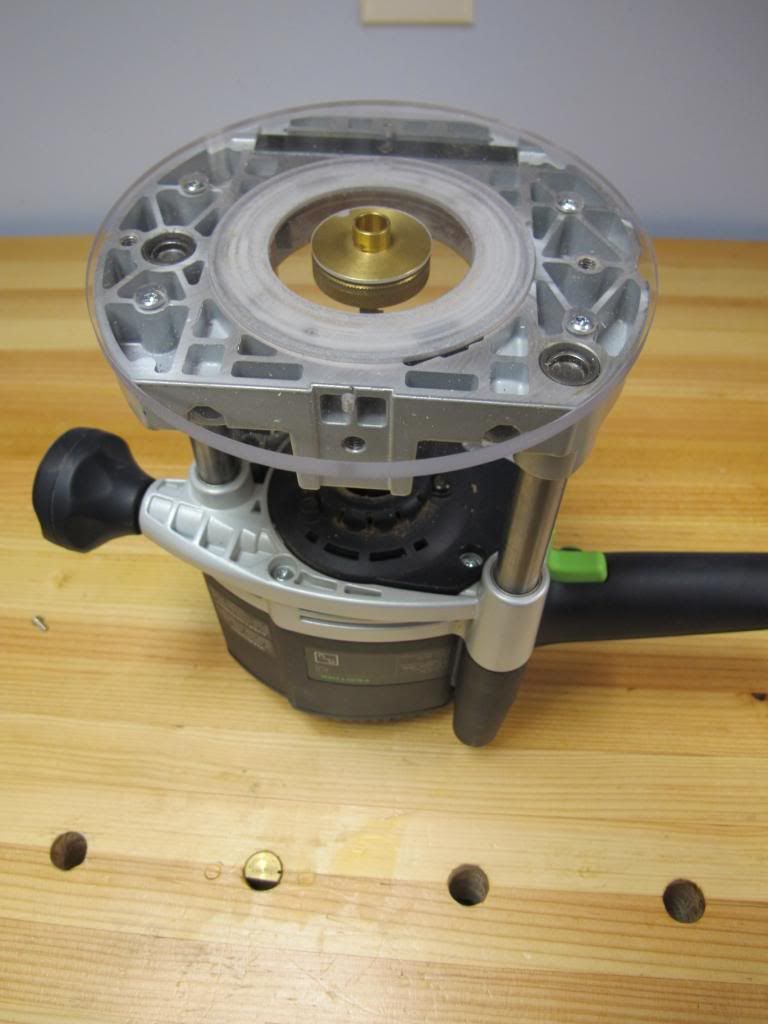
Hopefully this weekend I can try out these routers on the Leigh dovetail jig with better success.
Thanks for looking