Thanks, Hans!
The hoisting frame was made from construction timber that I used to shore up the stairs to my basement so they could take the load of the equipment and three or four people at the same time. The architect who designed the house told me each tread was rated at 400KG, but he couldn't remember what the maximum limit for the stairway was. I didn't want to take any chances, so I made a T-brace for each of the 12 treads that helped transfer the load to the floor. I also made a set of three graduated risers so a 1.5 square meter sheet of 19mm plywood could cover four treads at a time and make a large platform to rest the equipment while the chain hoist was repositioned during each move down the stairs. The chain hoist was attached to the upper level stair treads and didn't need any additional bracing.
I don't have any images of the bracing, but this is an image of the graduated risers with a smaller piece of plywood. The larger plywood covered four treads and made a stable platform to take the weight of any piece of equipment.
I used clamps and hinged bracing on each riser to minimize the risk of racking. It worked well, and while testing it without the plywood cover, I could not make the risers move no matter how jiggy I got with it. The bottoms of the risers have non-skid rubber sheets glued to them, so once in place, they do not slide around.
My immediate projects are mostly for my shop. These include finishing up the miter saw workstation (parts on order), building a router table (already in progress and parts on order), installing a Belfast sink in another room of the basement as part of my sharpening station, and making holders for my chisels, planes, saws, and other woodworking hand tools. I have some of the tools on the wall-mounted OSB, but have since bought more and need to redo the layout.
The hoisting frame was made from construction timber that I used to shore up the stairs to my basement so they could take the load of the equipment and three or four people at the same time. The architect who designed the house told me each tread was rated at 400KG, but he couldn't remember what the maximum limit for the stairway was. I didn't want to take any chances, so I made a T-brace for each of the 12 treads that helped transfer the load to the floor. I also made a set of three graduated risers so a 1.5 square meter sheet of 19mm plywood could cover four treads at a time and make a large platform to rest the equipment while the chain hoist was repositioned during each move down the stairs. The chain hoist was attached to the upper level stair treads and didn't need any additional bracing.
I don't have any images of the bracing, but this is an image of the graduated risers with a smaller piece of plywood. The larger plywood covered four treads and made a stable platform to take the weight of any piece of equipment.
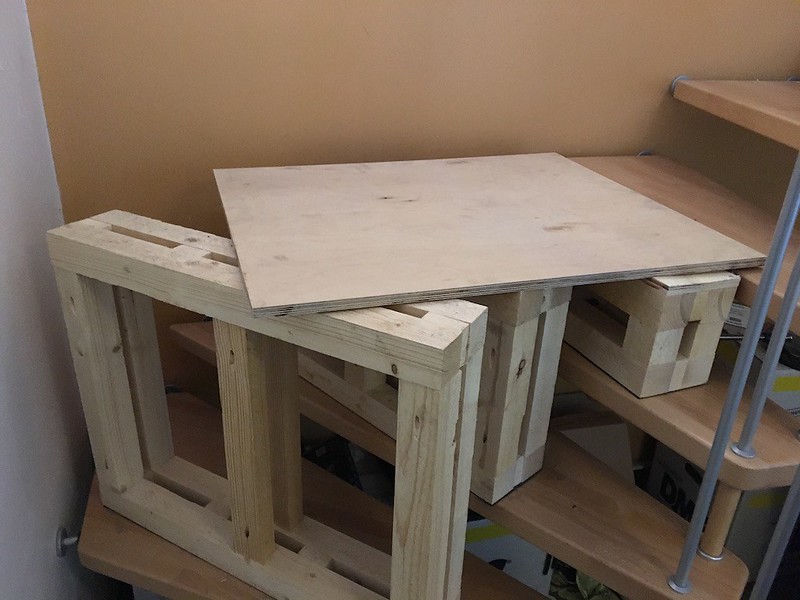
I used clamps and hinged bracing on each riser to minimize the risk of racking. It worked well, and while testing it without the plywood cover, I could not make the risers move no matter how jiggy I got with it. The bottoms of the risers have non-skid rubber sheets glued to them, so once in place, they do not slide around.

My immediate projects are mostly for my shop. These include finishing up the miter saw workstation (parts on order), building a router table (already in progress and parts on order), installing a Belfast sink in another room of the basement as part of my sharpening station, and making holders for my chisels, planes, saws, and other woodworking hand tools. I have some of the tools on the wall-mounted OSB, but have since bought more and need to redo the layout.