I finally found a reasonably priced spiral bit for drilling 25/32 holes. I love the 25/32 hole size because there is much less slop when using the parf and qwas dogs. I started with the freud 20mm bit but again, I had slop that would be fine for most but I dont like it. Then I went with the whiteside 1/2 in shank 25/32 double flute bit. This works great but It takes forever to drill a bunch of holes and burns alot if I try to speed up the plunge. So Finally I found the perfect bit for me.
Price is affordable and they shipped it next day. I will probably get a couple more bits from them.
The bit works like a charm. Faster, cleaner and cleans chips out better. I have noticed that the holes are a little tighter than even the 25/32 double flute whiteside bit. Probably due to the better cleaning out of the holes while routing. The dogs still fit and slide in and out fine, but for me and my system, now life is good. I am going to make a 4' X8' or a 5'X10' MFT table very soon using 80/20 rails. I am trying to reduce having to use my tablesaw by about 90%. That way I can regain some shop space that I had reserved for outfeed while cutting large sheets by myself. I never really felt safe doing that. With this setup, I will be good to go.
I almost ordered the 4 flute bit but then I realized it was 3/4 shank and didnt cut the center.
MSC Industrial 25/32 Milling bit
Price is affordable and they shipped it next day. I will probably get a couple more bits from them.
The bit works like a charm. Faster, cleaner and cleans chips out better. I have noticed that the holes are a little tighter than even the 25/32 double flute whiteside bit. Probably due to the better cleaning out of the holes while routing. The dogs still fit and slide in and out fine, but for me and my system, now life is good. I am going to make a 4' X8' or a 5'X10' MFT table very soon using 80/20 rails. I am trying to reduce having to use my tablesaw by about 90%. That way I can regain some shop space that I had reserved for outfeed while cutting large sheets by myself. I never really felt safe doing that. With this setup, I will be good to go.
I almost ordered the 4 flute bit but then I realized it was 3/4 shank and didnt cut the center.
MSC Industrial 25/32 Milling bit
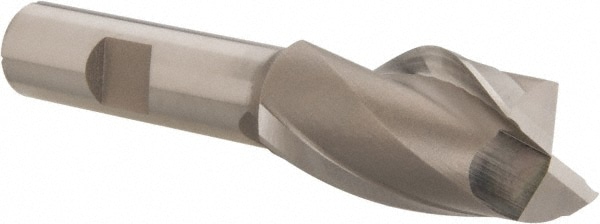