derekcohen
Member
- Joined
- Jun 22, 2008
- Messages
- 956
I sort of collect ... and use ... Kiyohisa chisels. I purchased a set of slicks about 12 years ago, which were a 3 year wait. I was lucky - soon after this there was a 6 year waiting list. Unfortunately, they are now no longer being made as Watanabe Kiyoei has been very ill for some time.
So Yamashita writes about Watanabe:https://www.japan-tool.com/nomi/Kiyohisa_Oiire/Kiyohisa_Oiire.html
There are better nomi than Kiyohisa, that is, blades which hold a longer edge, but using these always makes me smile.
I wanted some of the oire nomi - bench chisels - however they have become collector's tools and incredibly expensive. There are some silly prices on eBay. Not sure if they are actually sold at the asking money. I've been lucky, and managed to pick up a few - and new! - for very reasonable amounts.
A few weeks ago I purchased a 30mm oire nomi on eBay. It was going quite cheaply, mainly because it was 30 years old and used. It arrived yesterday, and I was disappointed. It had not been looked after. Yes, the blade was worn, but there is a lot of meat left, and it said to me that it was used well. It was smaller than expected, but not the issue on its own. It was the handle, now about 3/4" to 1" shorter than the original .. and this made it too small for my hand.
The advert in the auction did not represent the state of the chisel accurately. I could have sent it back, but the cost of doing so was prohibitive (what has happened to US shipping costs!!!). The Seller was really a good guy. We talked about it. In the end he refunded part of the purchase price (making it even cheaper), and I decided to renovate the chisel. Perhaps restore some of it past glory?
This is going to be one of those articles with LOTS of photos - all you wanted to know about dismantling and rebuilding an oire nomi
Here is the chisel when it arrived, alongside a 24mm Kiyohisa oire nomi (on the left), which is new ...
So ... we need to make a new handle. I have some US White Oak, which is the closest wood to the Japanese White Oak used by Watanabe among the others in my collection. That will have to do ... I can always make another handle if this does not work out.
First step is to remove the handle. These chisels are constructed with a tang and a socket. How do you get them apart? The answer is to rap the handle on a hard surface ...
Just keep tapping. It will come apart ... eventually.
Take note - the tag is square, as is the mortice ...
Next: remove the ferrule. It comes off the opposite way it went on! I had an idea to make a tool to do this from a short section of aluminium tube - hammered the end flat ....
... then popped the handle inside, and tapped the end down ...
... and off came the ferrule ...
Now we go over to the lathe. The White Oak has been turned into a cylinder, and the length of the handle marked from the 24mm Kiyohisa. I have orientated the wood until the grain runs as straight as possible ...
The other measurements that are needed are the diameter of the handle, and the start and end of the tenon ...
The tenon is turned from the latter measurements ...
Next, clean the inside of the ferrule. It is rusty.
It needs to slip on firmly, and sit flush with the end of the tenon ...
Drill out most of the mortice ...
... and then mark and chisel out an exact fit for the tang ...
The fit is as good as I could hope for - a little force drives it home ...
Back to the lathe to add a small chamfer to the tenon ...
Before the handle is cut to length, some finish is added. Initially, this was just Renaissance Wax. However, later when sharpening the blade I notice that this failed to stop the wood becoming black (as the tannin in oak is apt to do around iron filings). I returned later to re-finish the handle in Ubeaut Shellawax.
After 30 years, the ferrule has been hammered and has flat spots. These need to be removed otherwise it will not fit over the end of the handle. I used a knife to scrape the inside of the band ...
To re-fit the ferrule, the handle is marked off with about 2mm spare ...
At this stage the ferrule does not fit ...
... and the end of the handle needs to be pared ...
It can be hammered on until it lies flush ...
I do not own a tool for seating the ferrule. Over the years I have set the ferrules on Japanese chisels using a brass plumbing connector ...
Drive the ferrule down about 2mm below the end of the handle ...
Then peen the edges of the handle over the ferrule ...
The peened ends do not extend over the ferrule - it is the handle you hit, not the ferrule.
All put together ...
The blade is sharpened. Japanese blades are a composite of a hard steel layer, the “hagane”, and a softer iron body called “jigane”. In cheap or poorly made blades, the hagane is thin and uneven. The hagane in the Kiyohisa is thick and even ...
Three Kiyohisa oire nomi (6mm, 24mm and 30mm): US White Oak, Japanese White Oak, and Japanese Red Oak ...
I am happy with the new addition.
Regards from Perth
Derek
So Yamashita writes about Watanabe:https://www.japan-tool.com/nomi/Kiyohisa_Oiire/Kiyohisa_Oiire.html
There are better nomi than Kiyohisa, that is, blades which hold a longer edge, but using these always makes me smile.
I wanted some of the oire nomi - bench chisels - however they have become collector's tools and incredibly expensive. There are some silly prices on eBay. Not sure if they are actually sold at the asking money. I've been lucky, and managed to pick up a few - and new! - for very reasonable amounts.
A few weeks ago I purchased a 30mm oire nomi on eBay. It was going quite cheaply, mainly because it was 30 years old and used. It arrived yesterday, and I was disappointed. It had not been looked after. Yes, the blade was worn, but there is a lot of meat left, and it said to me that it was used well. It was smaller than expected, but not the issue on its own. It was the handle, now about 3/4" to 1" shorter than the original .. and this made it too small for my hand.
The advert in the auction did not represent the state of the chisel accurately. I could have sent it back, but the cost of doing so was prohibitive (what has happened to US shipping costs!!!). The Seller was really a good guy. We talked about it. In the end he refunded part of the purchase price (making it even cheaper), and I decided to renovate the chisel. Perhaps restore some of it past glory?
This is going to be one of those articles with LOTS of photos - all you wanted to know about dismantling and rebuilding an oire nomi

Here is the chisel when it arrived, alongside a 24mm Kiyohisa oire nomi (on the left), which is new ...
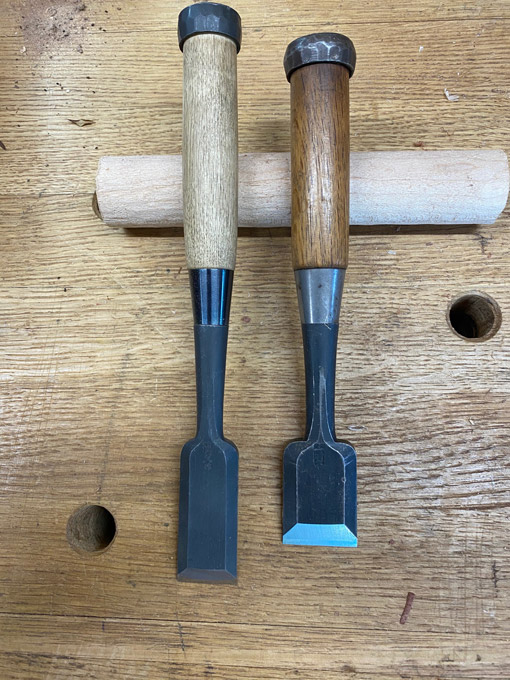
So ... we need to make a new handle. I have some US White Oak, which is the closest wood to the Japanese White Oak used by Watanabe among the others in my collection. That will have to do ... I can always make another handle if this does not work out.
First step is to remove the handle. These chisels are constructed with a tang and a socket. How do you get them apart? The answer is to rap the handle on a hard surface ...
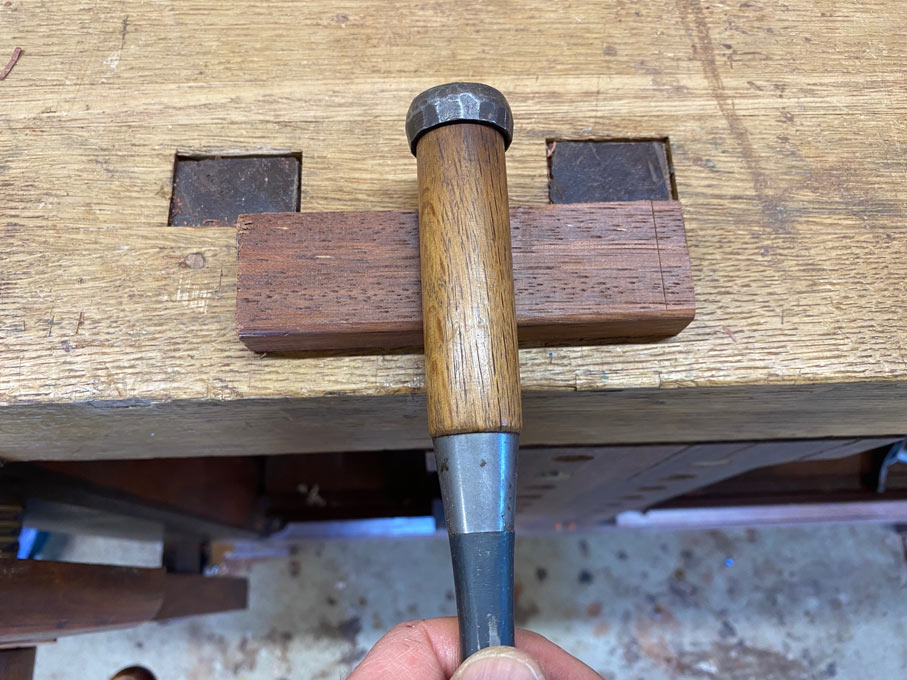
Just keep tapping. It will come apart ... eventually.
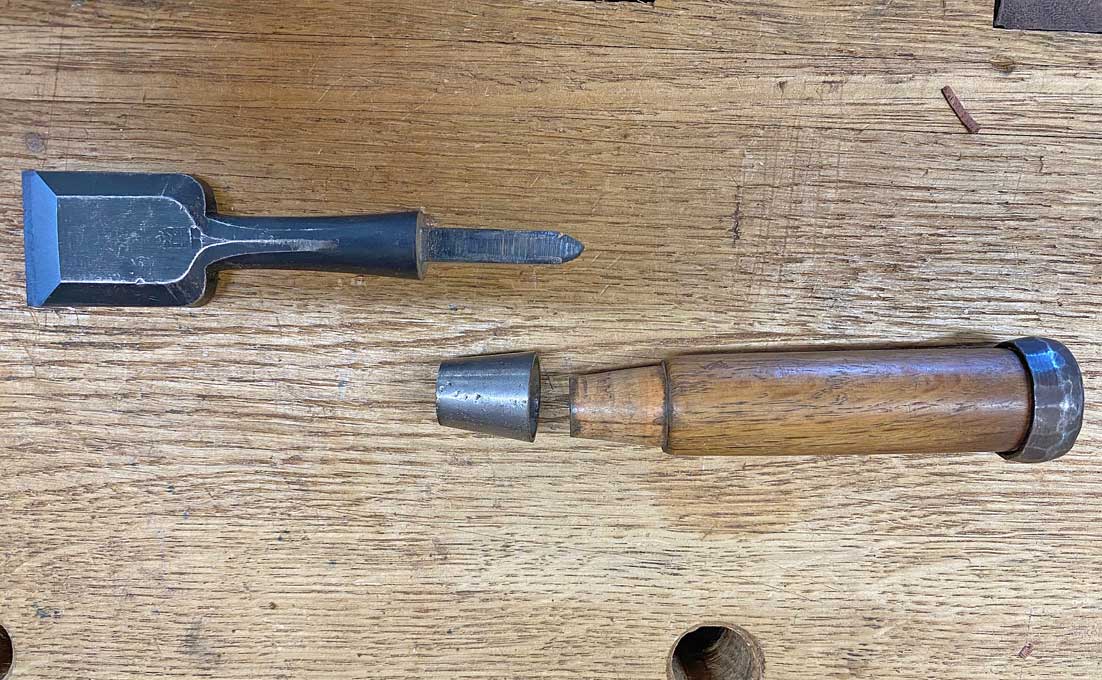
Take note - the tag is square, as is the mortice ...
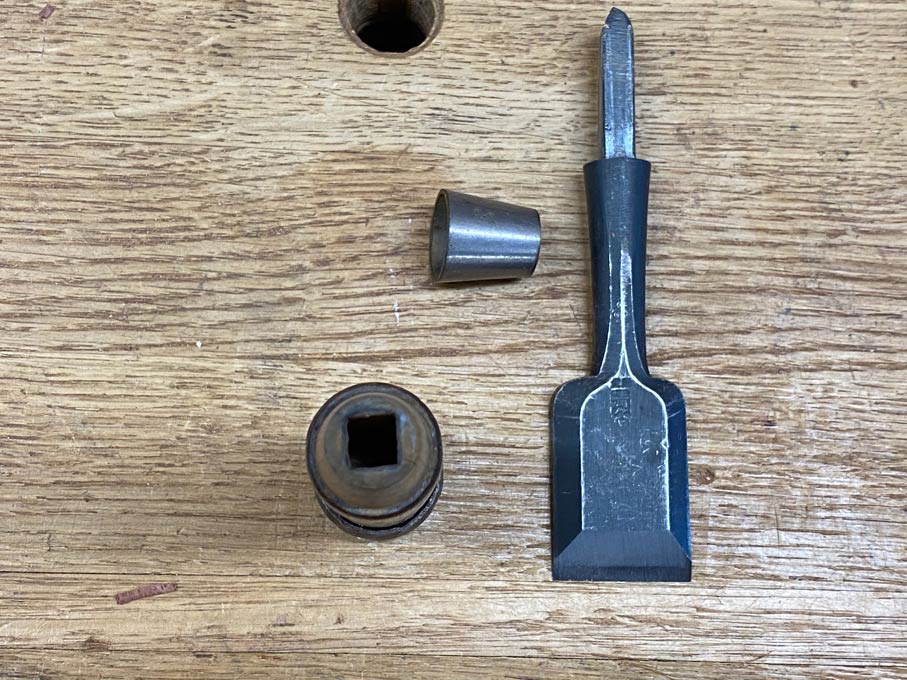
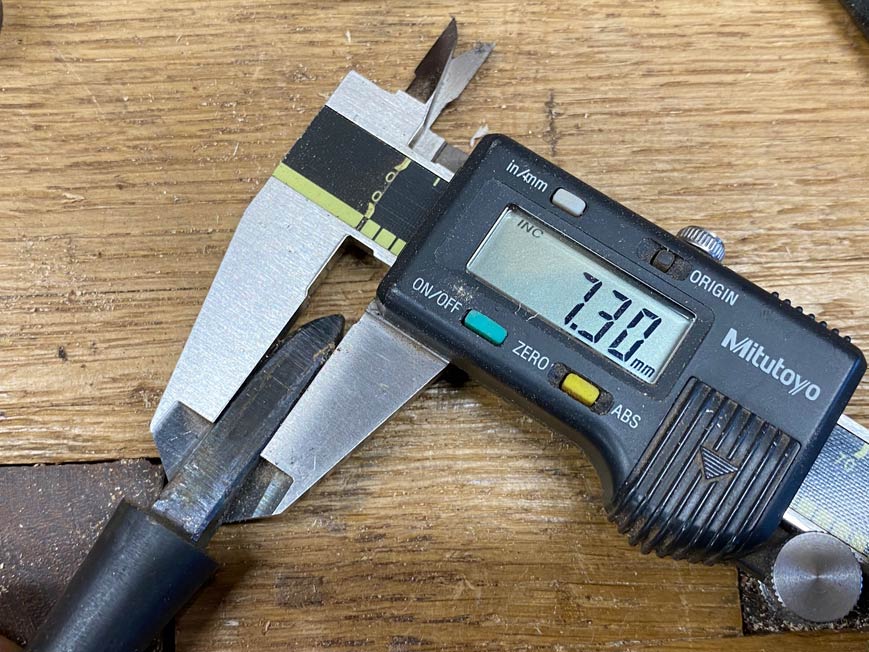
Next: remove the ferrule. It comes off the opposite way it went on! I had an idea to make a tool to do this from a short section of aluminium tube - hammered the end flat ....
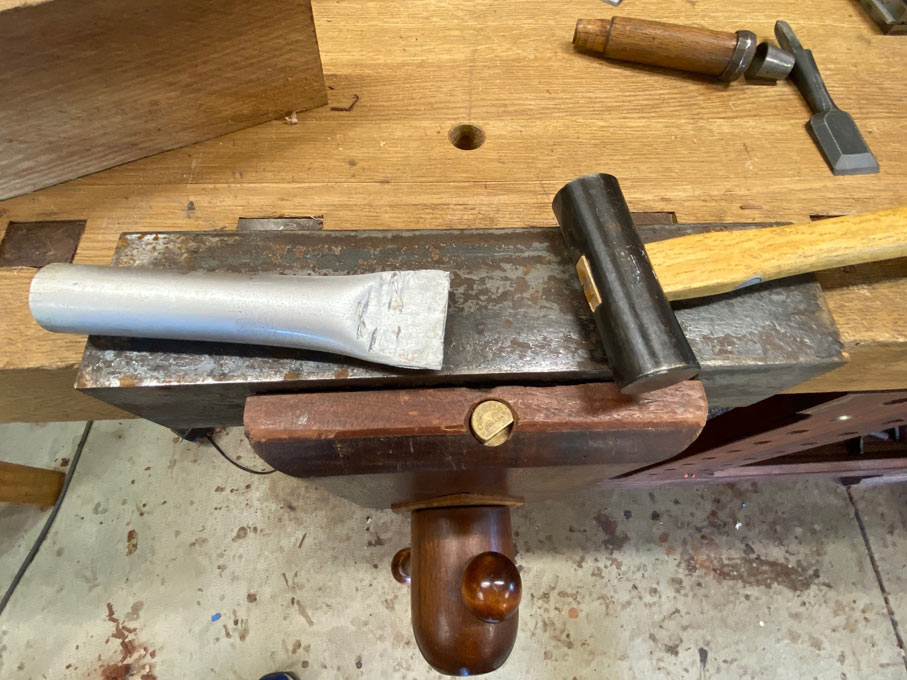
... then popped the handle inside, and tapped the end down ...

... and off came the ferrule ...
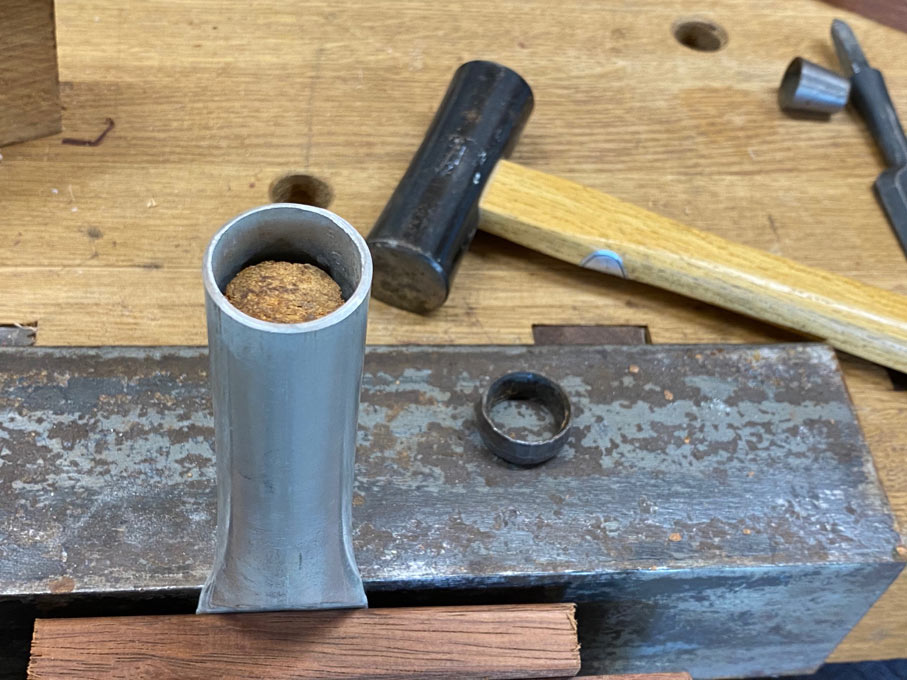
Now we go over to the lathe. The White Oak has been turned into a cylinder, and the length of the handle marked from the 24mm Kiyohisa. I have orientated the wood until the grain runs as straight as possible ...
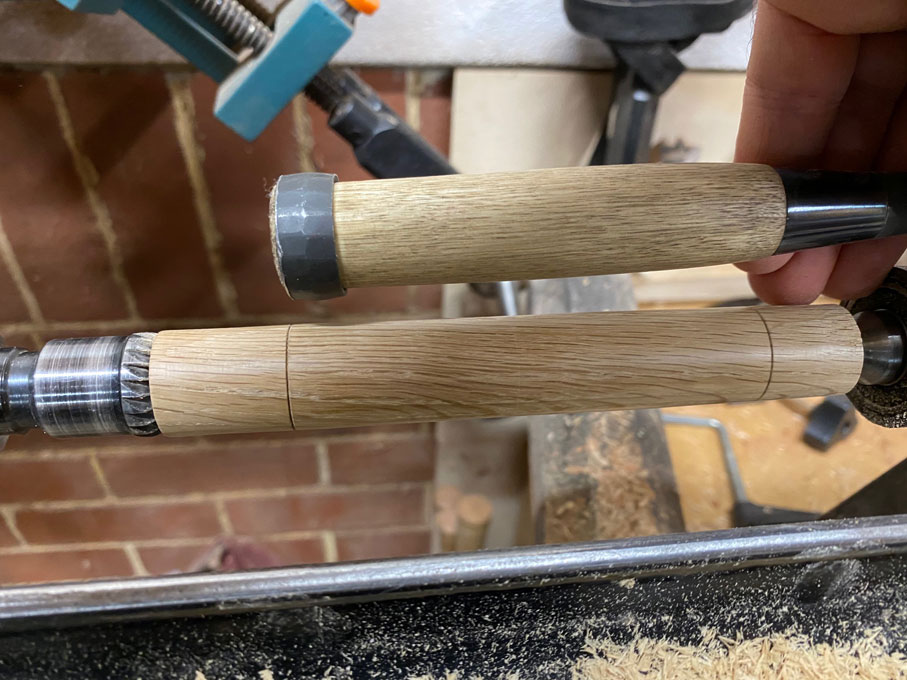
The other measurements that are needed are the diameter of the handle, and the start and end of the tenon ...
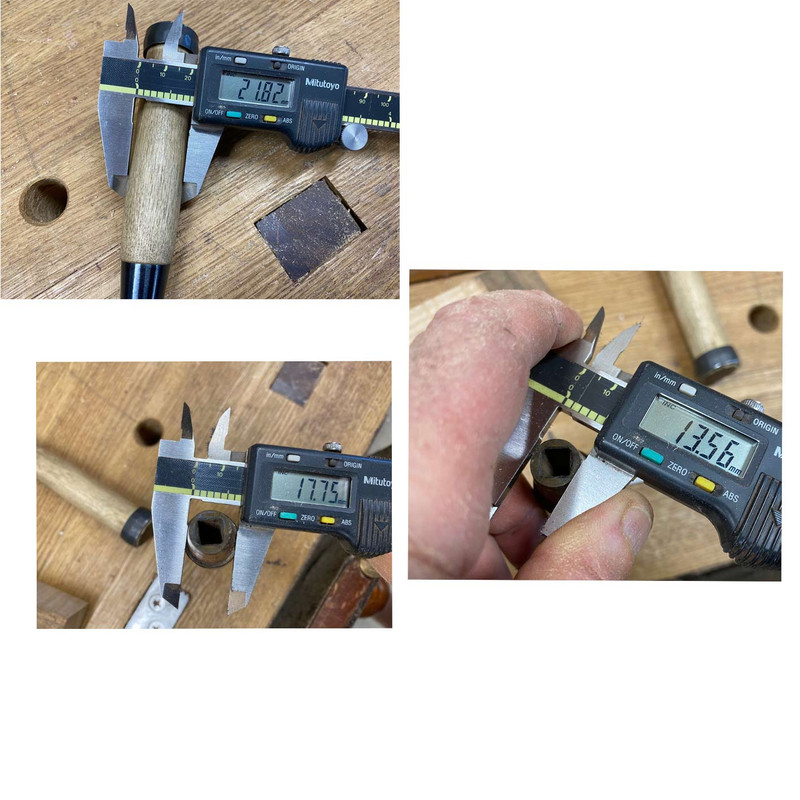
The tenon is turned from the latter measurements ...
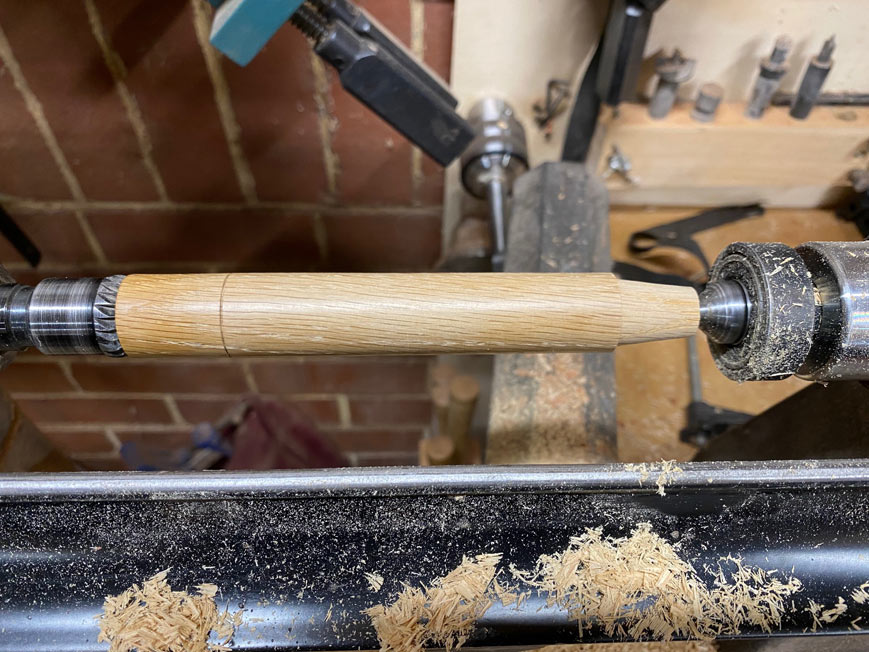
Next, clean the inside of the ferrule. It is rusty.
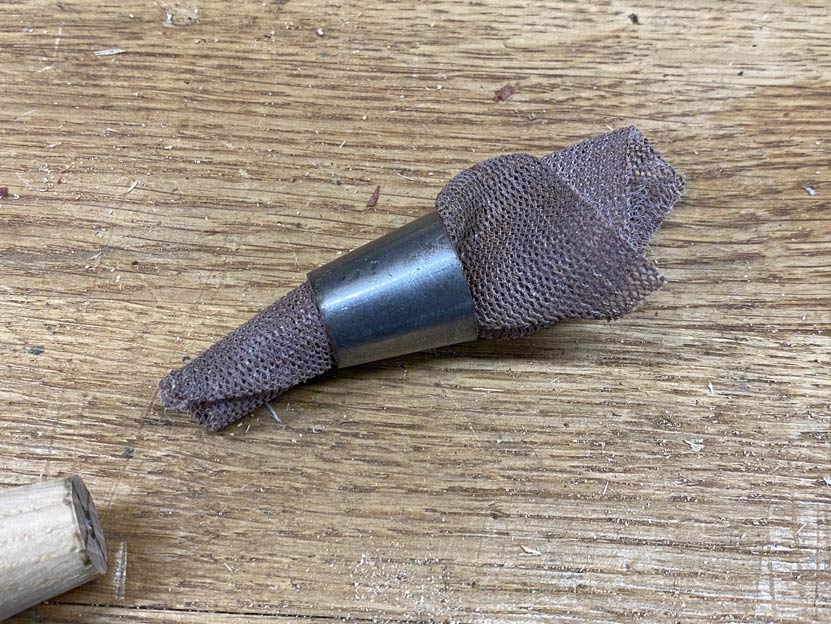
It needs to slip on firmly, and sit flush with the end of the tenon ...
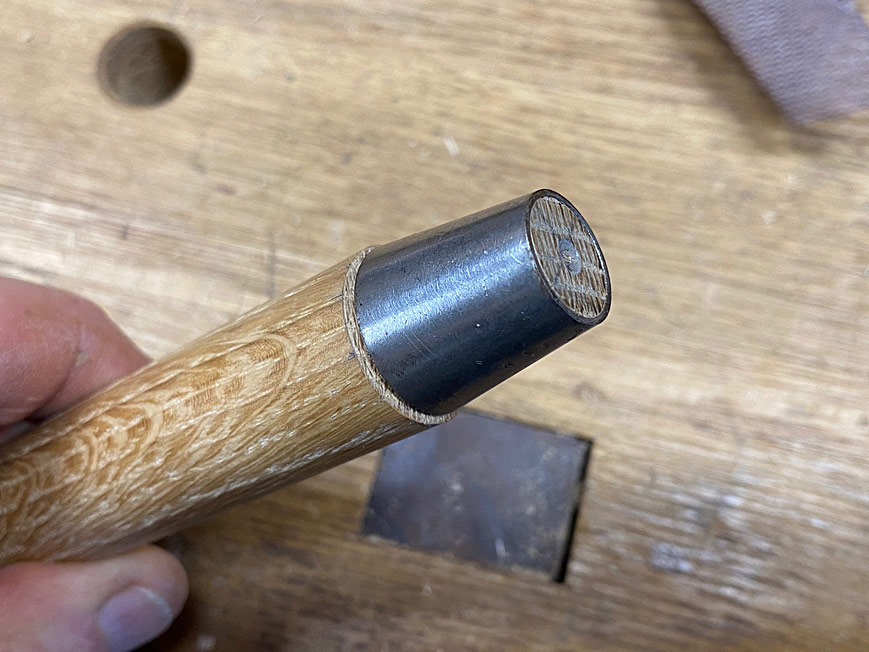
Drill out most of the mortice ...
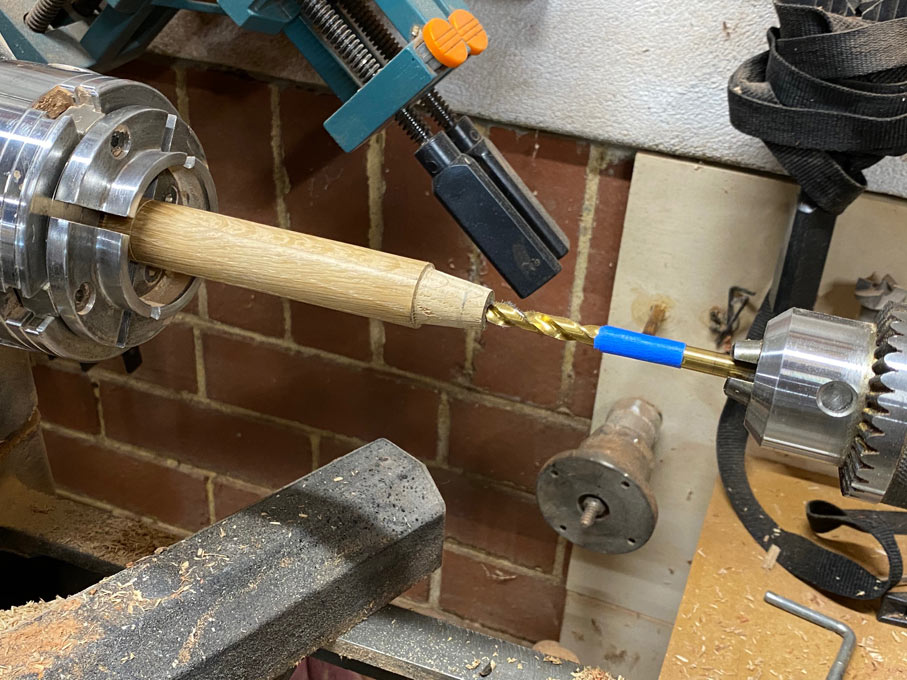
... and then mark and chisel out an exact fit for the tang ...
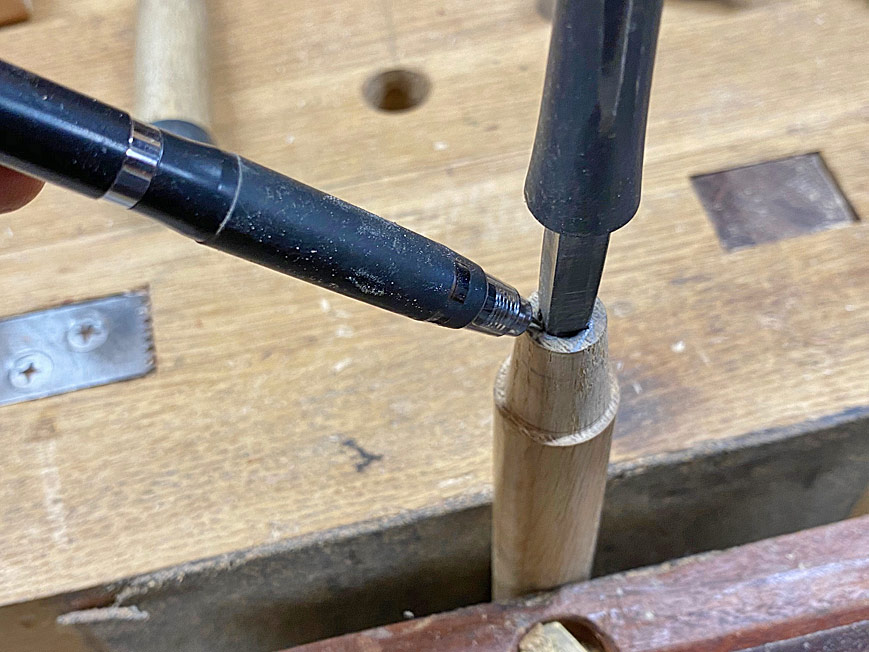
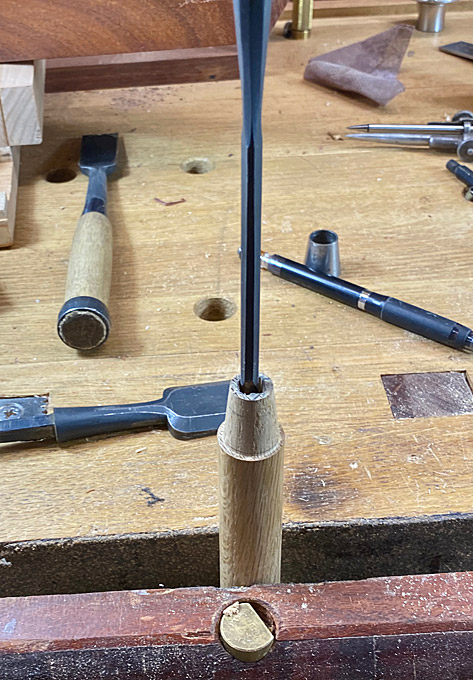
The fit is as good as I could hope for - a little force drives it home ...
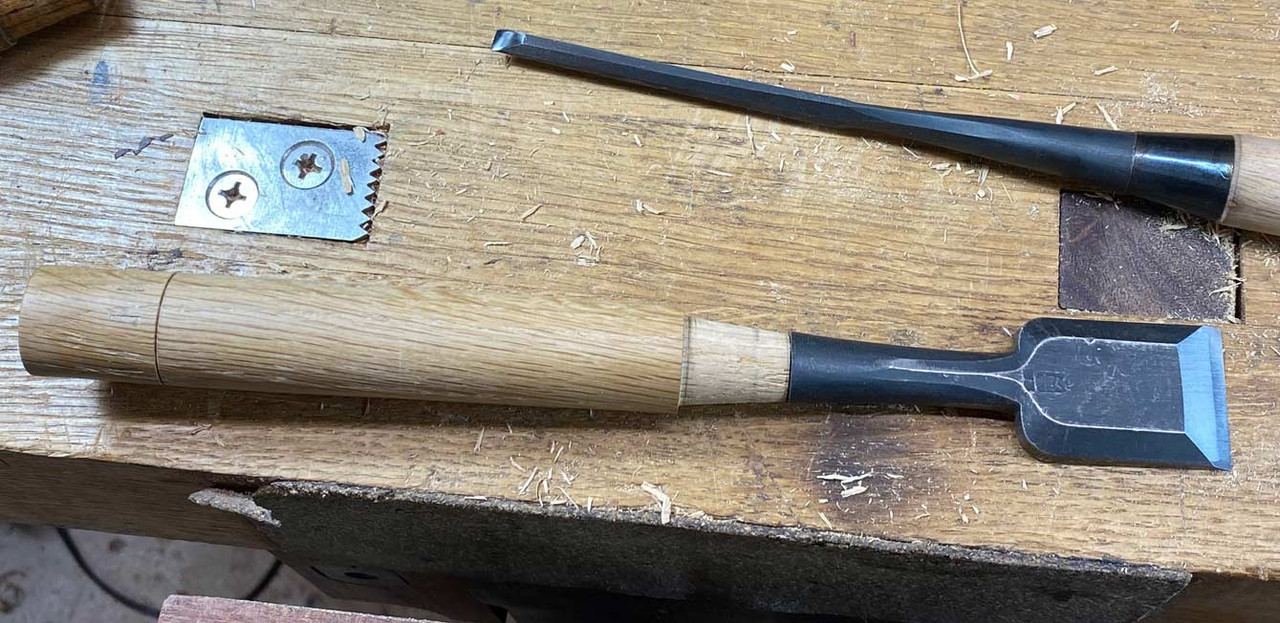
Back to the lathe to add a small chamfer to the tenon ...
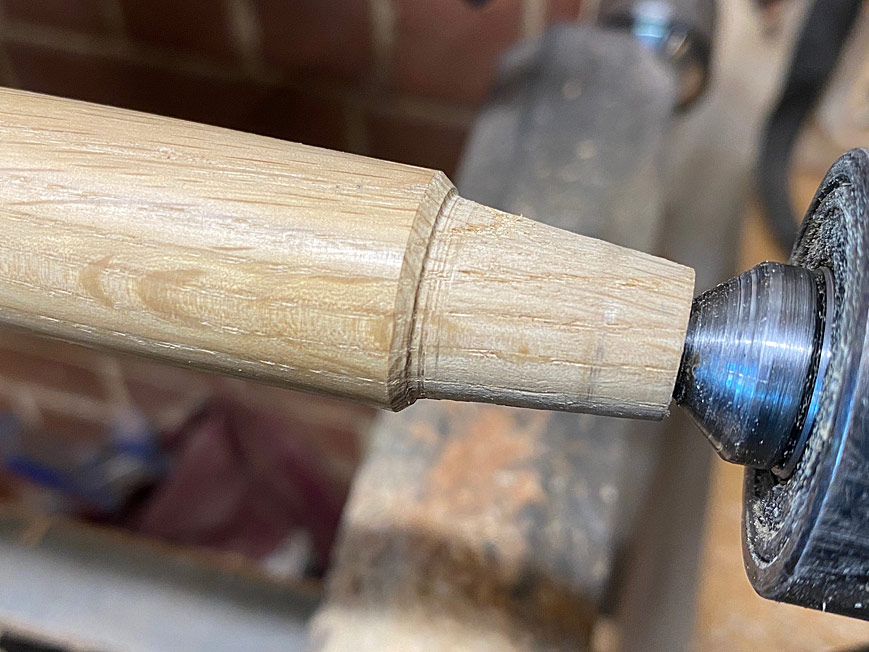
Before the handle is cut to length, some finish is added. Initially, this was just Renaissance Wax. However, later when sharpening the blade I notice that this failed to stop the wood becoming black (as the tannin in oak is apt to do around iron filings). I returned later to re-finish the handle in Ubeaut Shellawax.
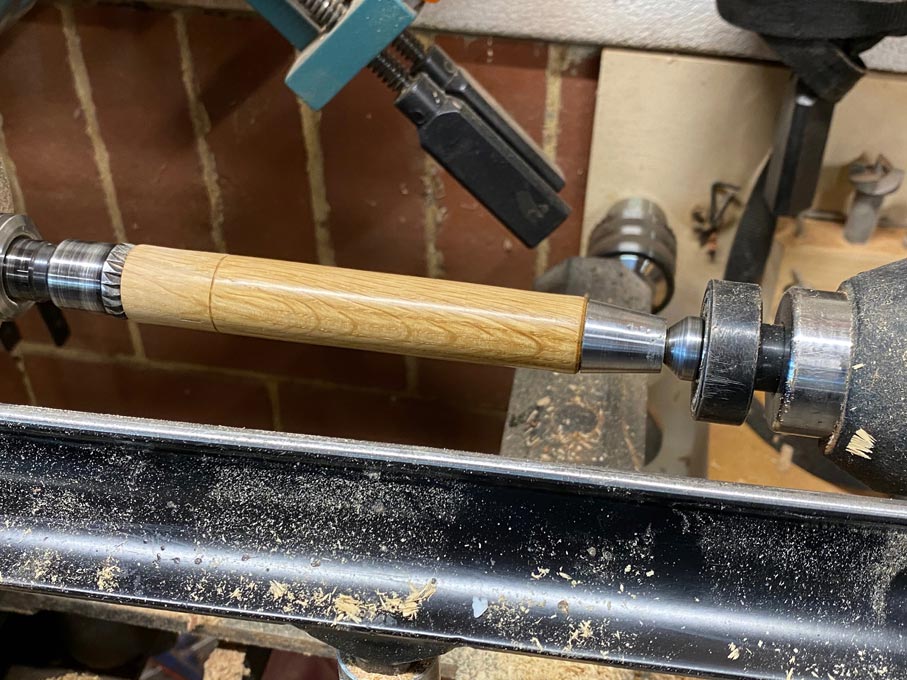
After 30 years, the ferrule has been hammered and has flat spots. These need to be removed otherwise it will not fit over the end of the handle. I used a knife to scrape the inside of the band ...
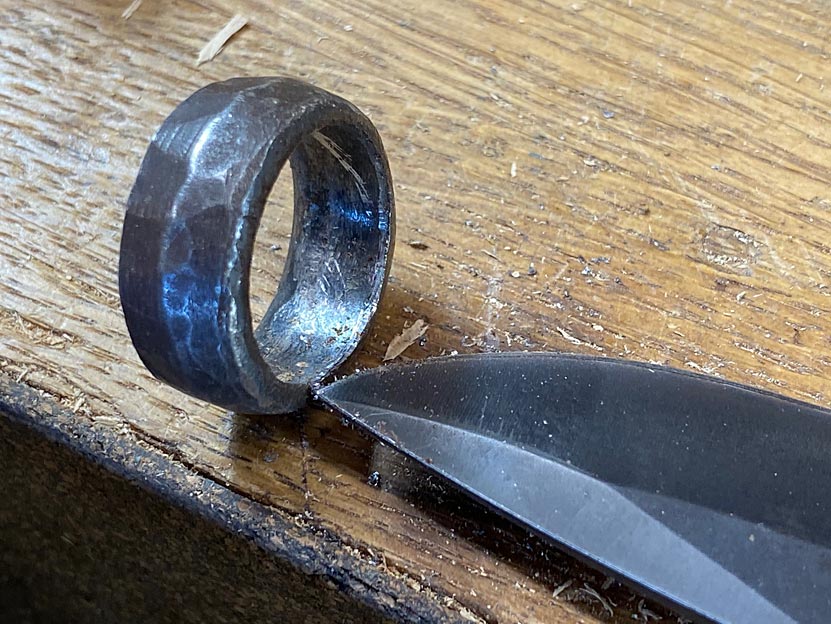
To re-fit the ferrule, the handle is marked off with about 2mm spare ...
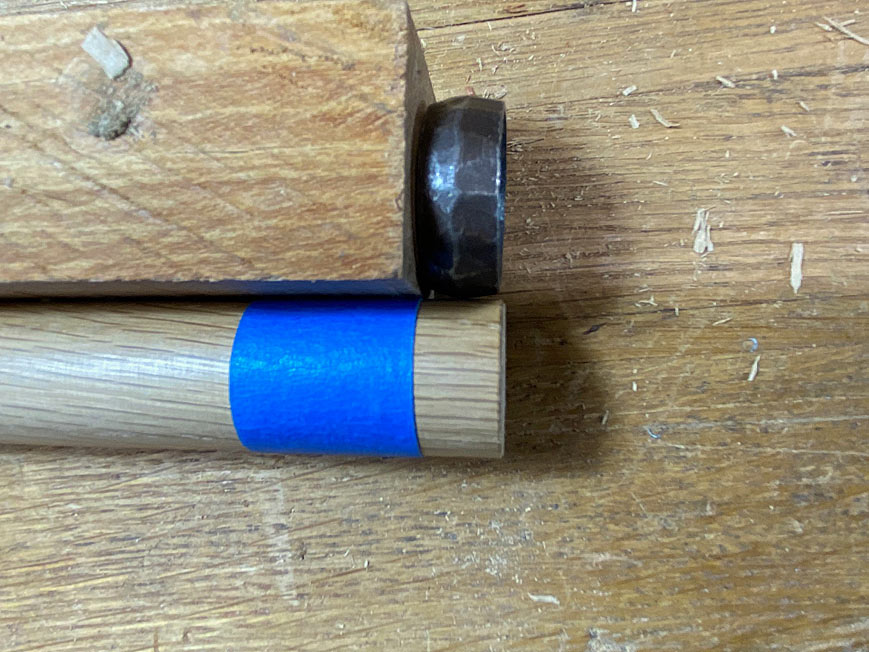
At this stage the ferrule does not fit ...
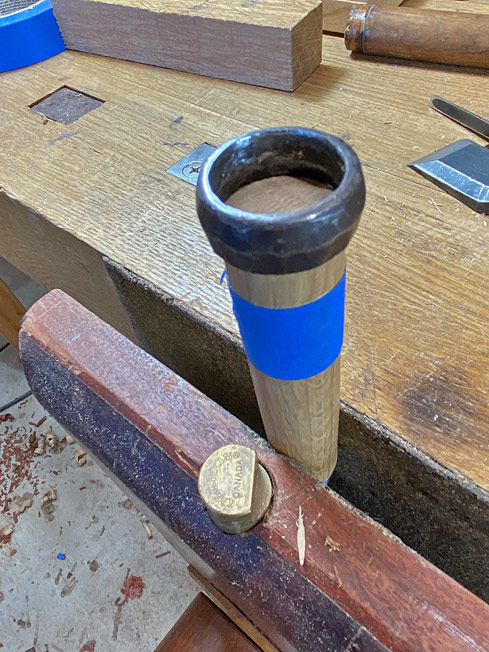
... and the end of the handle needs to be pared ...
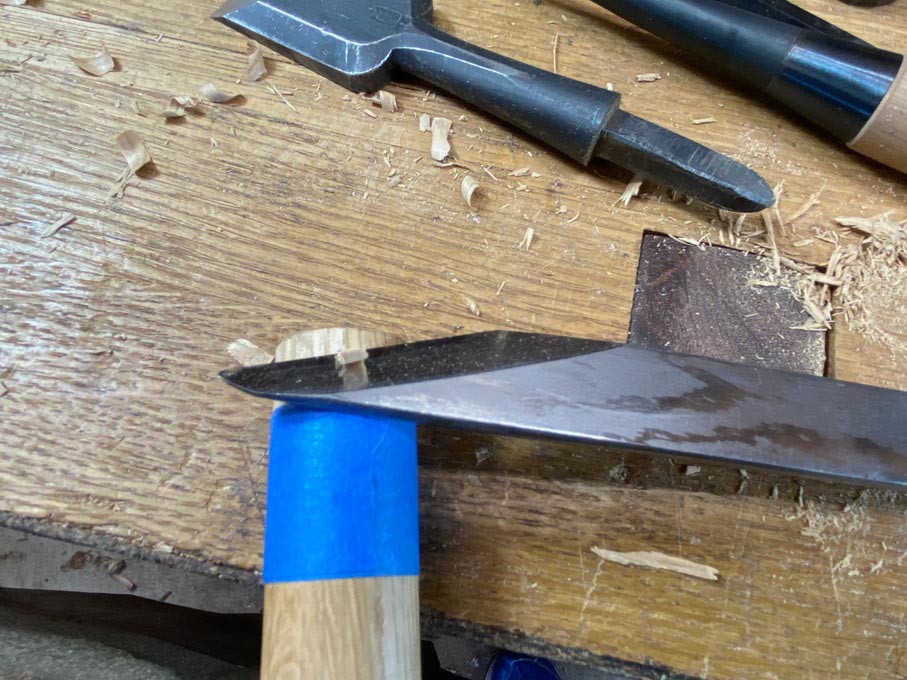
It can be hammered on until it lies flush ...
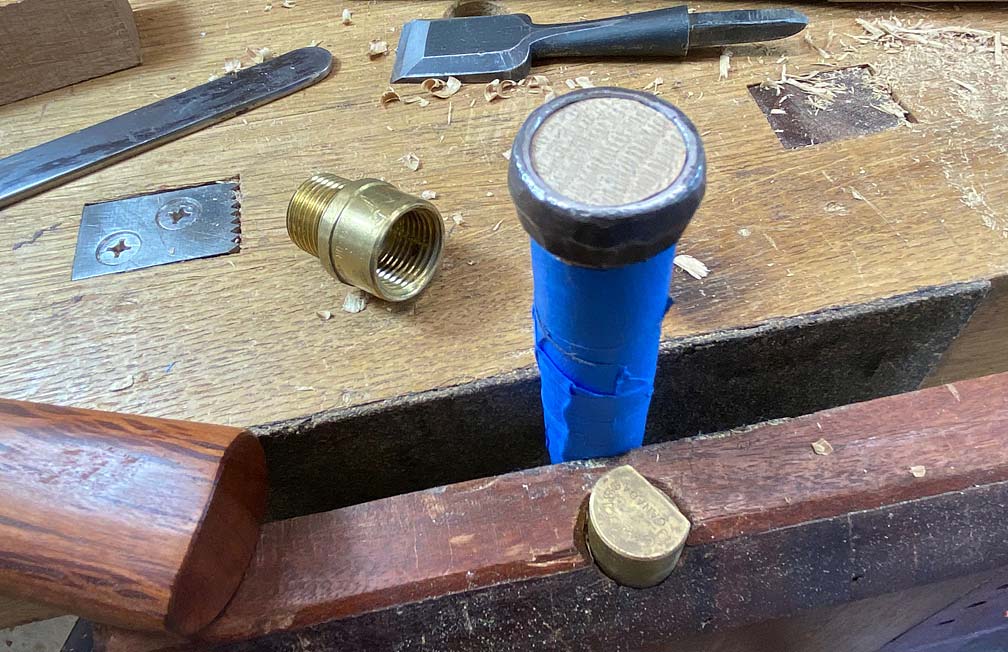
I do not own a tool for seating the ferrule. Over the years I have set the ferrules on Japanese chisels using a brass plumbing connector ...
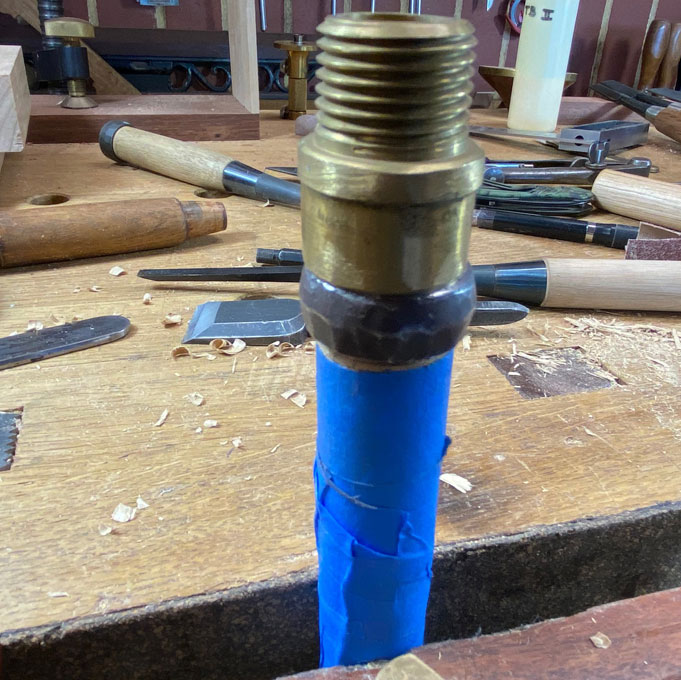
Drive the ferrule down about 2mm below the end of the handle ...
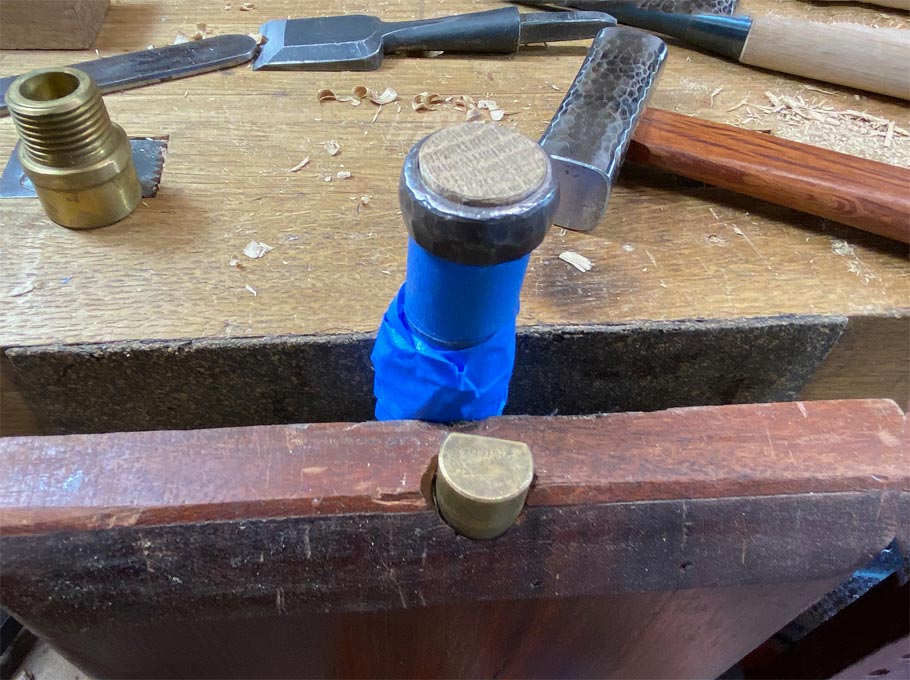
Then peen the edges of the handle over the ferrule ...
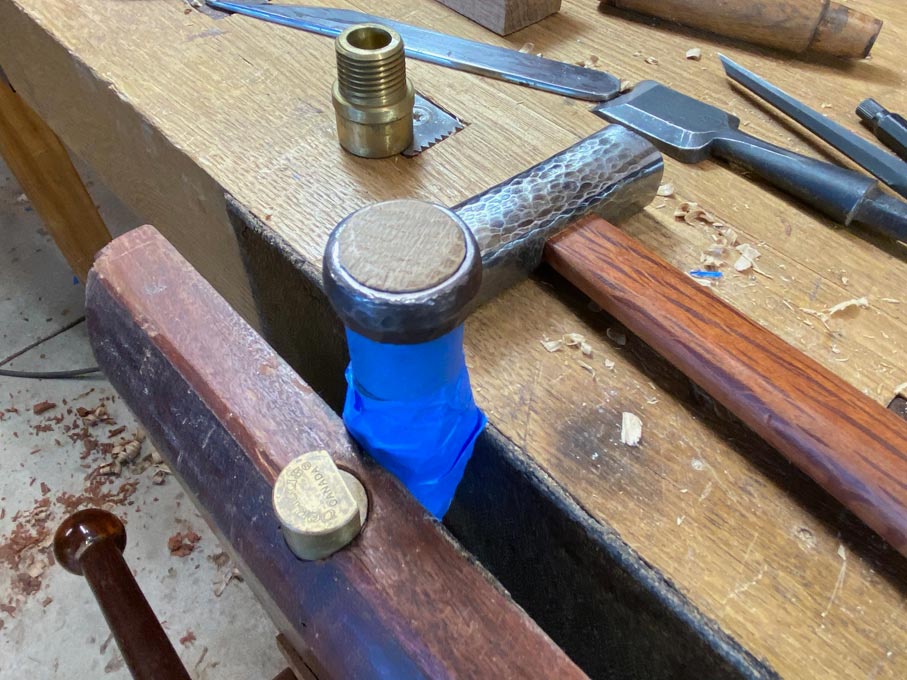
The peened ends do not extend over the ferrule - it is the handle you hit, not the ferrule.
All put together ...
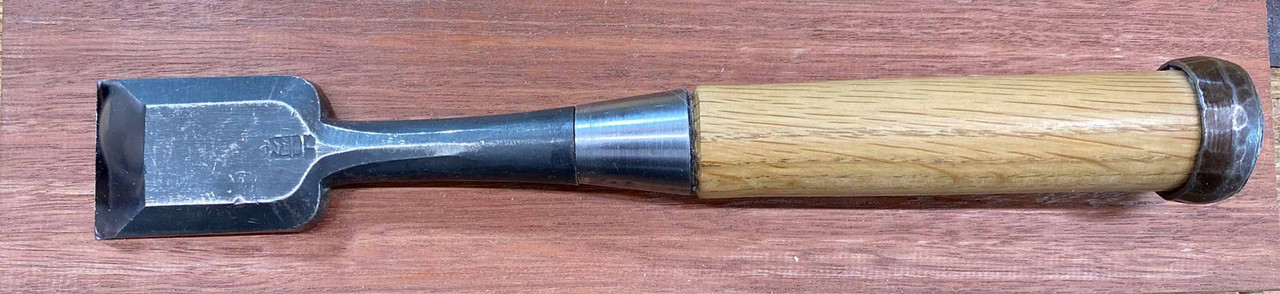
The blade is sharpened. Japanese blades are a composite of a hard steel layer, the “hagane”, and a softer iron body called “jigane”. In cheap or poorly made blades, the hagane is thin and uneven. The hagane in the Kiyohisa is thick and even ...
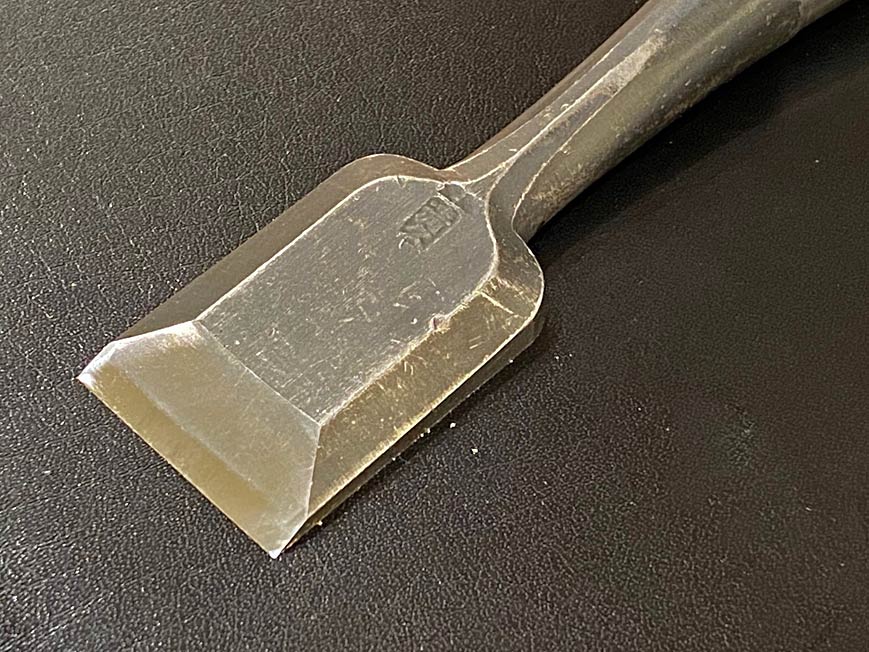
Three Kiyohisa oire nomi (6mm, 24mm and 30mm): US White Oak, Japanese White Oak, and Japanese Red Oak ...
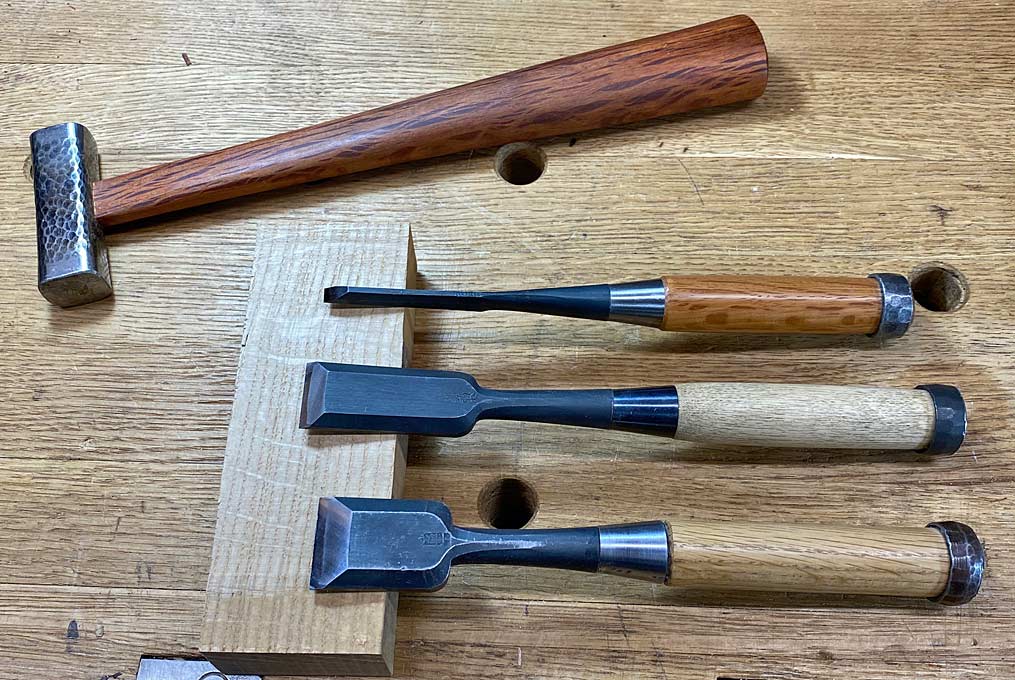
I am happy with the new addition.
Regards from Perth
Derek