4nthony
Member
I'm building a knock-down desk for my daughter and had planned on using cross dowels. After some thought, I decided I didn't want the cross dowels holes visible -- however, the connectors will still be visible -- so I ordered some threaded inserts. I wasn't paying close attention and ended up ordering flanged inserts instead of flush.
I can countersink the flange so the attaching piece is pulled flush, but it got me thinking: why is there a flange on a threaded insert?
This is probably a silly question, but I'm sure there's a valid reason for the flange. I just can't think of one.
Maybe they are specific to soft-wood inserts as hardwood inserts seem to all be flush. Anyway, just curious about this.
[cool]
I can countersink the flange so the attaching piece is pulled flush, but it got me thinking: why is there a flange on a threaded insert?
This is probably a silly question, but I'm sure there's a valid reason for the flange. I just can't think of one.
Maybe they are specific to soft-wood inserts as hardwood inserts seem to all be flush. Anyway, just curious about this.
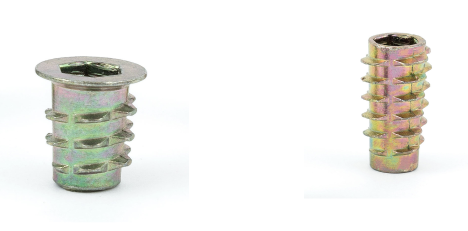
[cool]