derekcohen
Member
- Joined
- Jun 22, 2008
- Messages
- 962
While I have a Roubo-style workbench and prefer hand tools ...
... and have a Hammer K3 slider to take care of rip- and crosscutting ...
... it has dawned on me that that a MFT (multifunction table) would provide more than just another option for sawing - it could provide an ideal small assembly bench as well as a bench for holding small parts for routing and sanding. The balance was tipped when I recently acquired a (new) Festool AT 65EB track saw ... 20 years old but used once or twice at most.
I build a small workbench in solid timber: 1200 x 600mm pine frame and merbau top. Although I have a Domino, the construction was mortice-and-tenon. Since the top was not a standard MFT, it was necessary that I drill the 20mm holes. These were to be 96mm apart, as with the Festool MFT.
There are basically two methods to make one's own: the UFK Parf guide (drill), and the Trend template (router). The cheaper Trend template is $300 in Australia. Fortunately, I was offered the opportunity to make a template by a friend with a CNC. This went one better than the Trend, by doubling it in size. The template has 30mm holes and is used with a guide bush and 20mm router bit to create the 20mm holes.
The bench top was prepared by ensuring all sides were square, and then the template was squared to the front and right side ...
My old Elu router is at least 25 years old. It used a 30mm Trend guide bush fitted into a custom made adapter ..
The router bit is a Trend 20mm ...
I was also very pleased to see how well the dust collection worked. The Elu did not come with dust collection - this was not important 25 years ago! - and I adapted the fitting from a Dewalt to fit it.
Once all the holes were routed ...
... the template needed to be moved to complete the bench top. This was facilitated by two dogs which my friend had thoughtfully made for this purpose ...
The dogs are fitted into the existing holes to align the pattern ...
The remaining holes were drilled.
It only then occurred to me to check the bench top for flat - I should have done this earlier, although the top was flat when I first put it together. There was a 0.5mm gap at the centre, and I decided to plane it flat ...
The top was then sanded(80 grit) ...
... all is flat ...
The holes received a fine chamfer ...
... and the right side was bevelled at 20 degrees.
The reason for this is that the bench will also act as a outfeed for the jointer/thicknesser-planer and sliding tablesaw ...
Finally, the top received a coat of flat poly to protect it during glue-ups ..
Thanks for watching. I will return once a fence is built, and show the various work-holding methods.
Regards from Perth
Derek
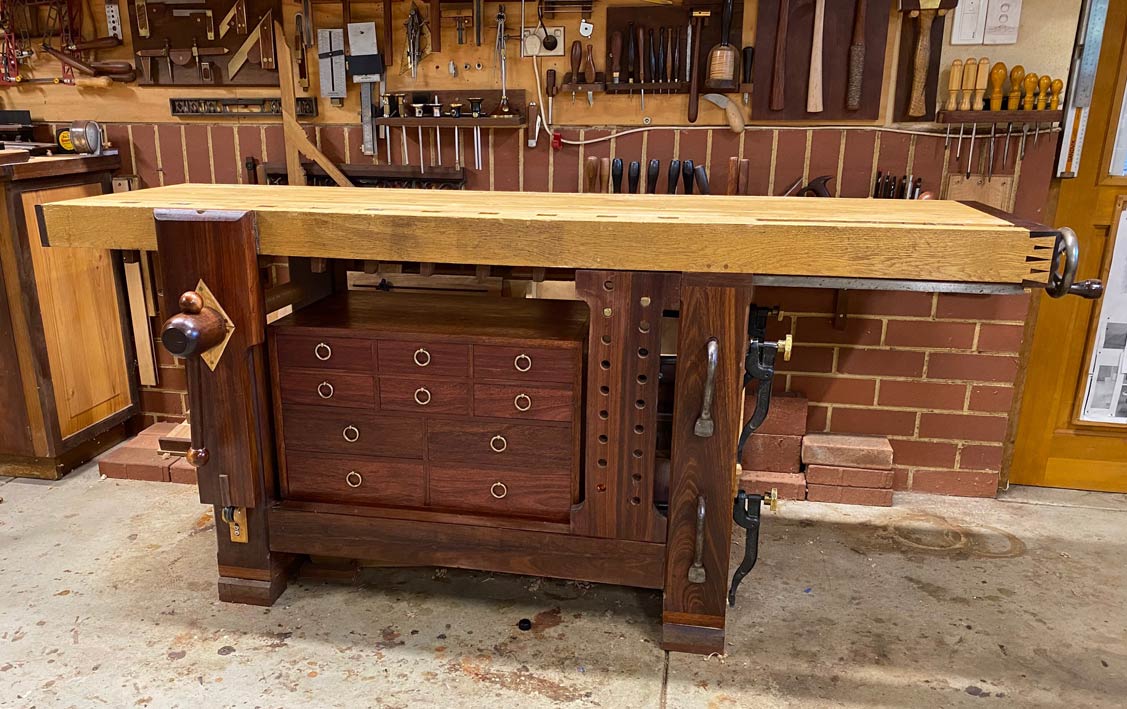
... and have a Hammer K3 slider to take care of rip- and crosscutting ...
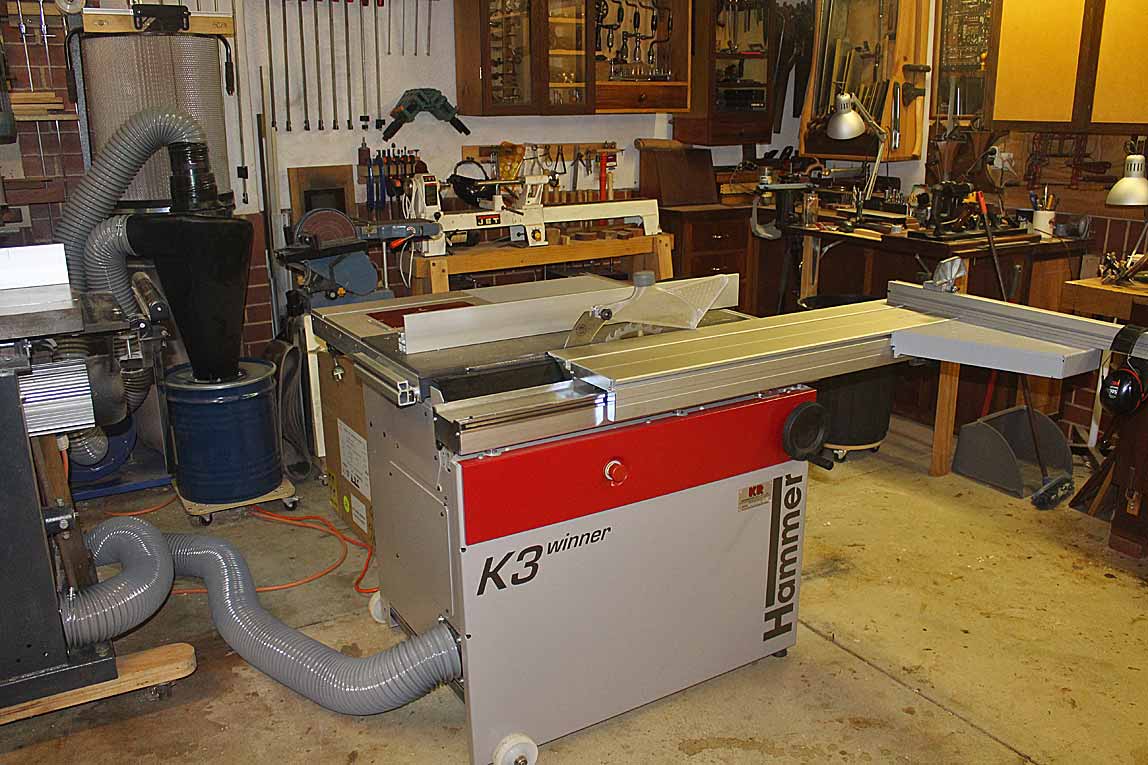
... it has dawned on me that that a MFT (multifunction table) would provide more than just another option for sawing - it could provide an ideal small assembly bench as well as a bench for holding small parts for routing and sanding. The balance was tipped when I recently acquired a (new) Festool AT 65EB track saw ... 20 years old but used once or twice at most.
I build a small workbench in solid timber: 1200 x 600mm pine frame and merbau top. Although I have a Domino, the construction was mortice-and-tenon. Since the top was not a standard MFT, it was necessary that I drill the 20mm holes. These were to be 96mm apart, as with the Festool MFT.
There are basically two methods to make one's own: the UFK Parf guide (drill), and the Trend template (router). The cheaper Trend template is $300 in Australia. Fortunately, I was offered the opportunity to make a template by a friend with a CNC. This went one better than the Trend, by doubling it in size. The template has 30mm holes and is used with a guide bush and 20mm router bit to create the 20mm holes.
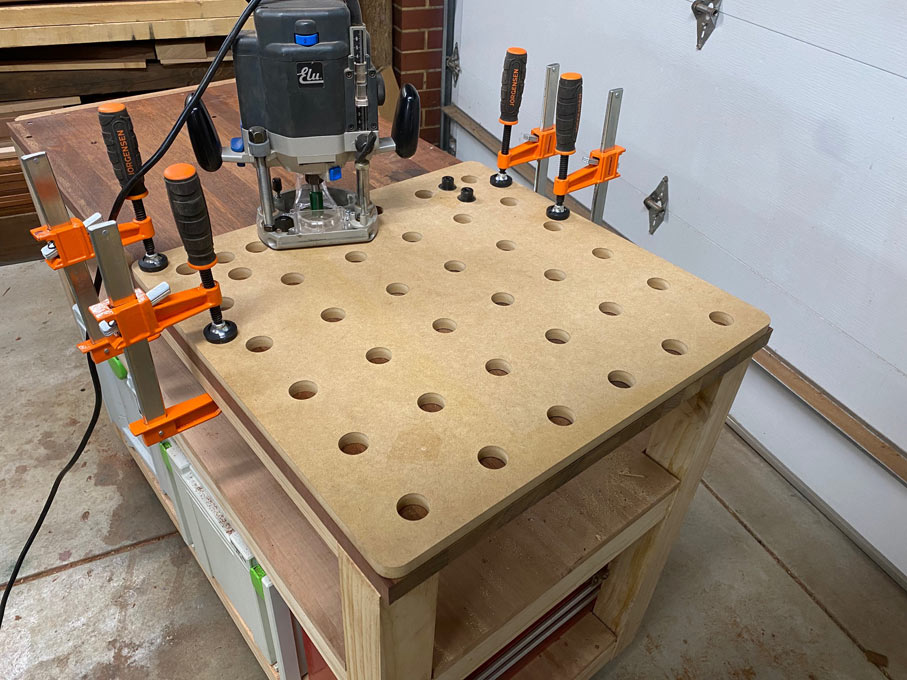
The bench top was prepared by ensuring all sides were square, and then the template was squared to the front and right side ...
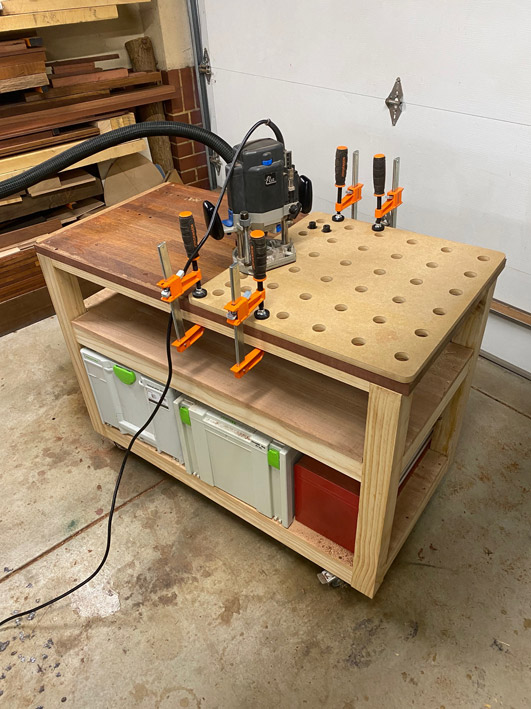
My old Elu router is at least 25 years old. It used a 30mm Trend guide bush fitted into a custom made adapter ..
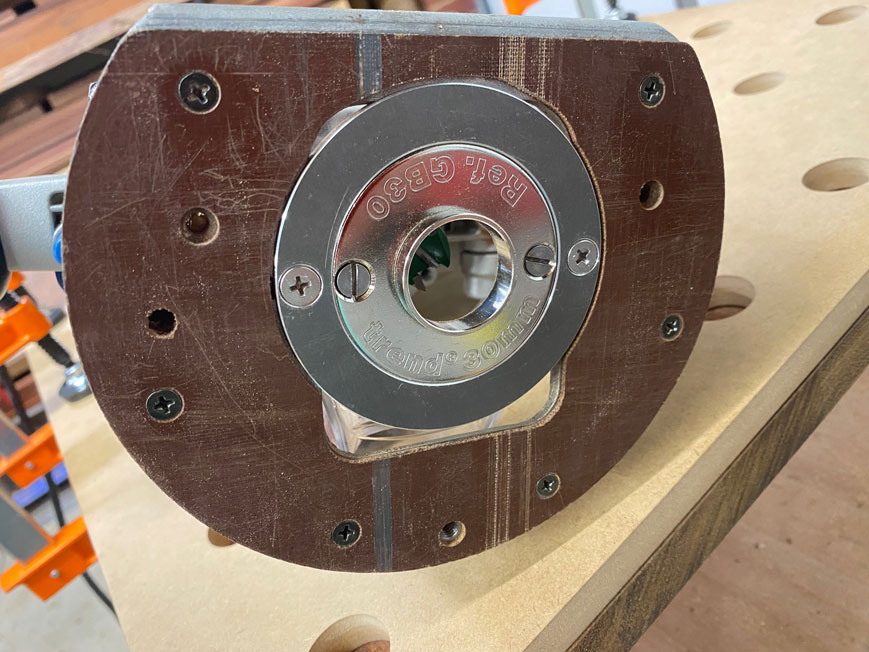
The router bit is a Trend 20mm ...
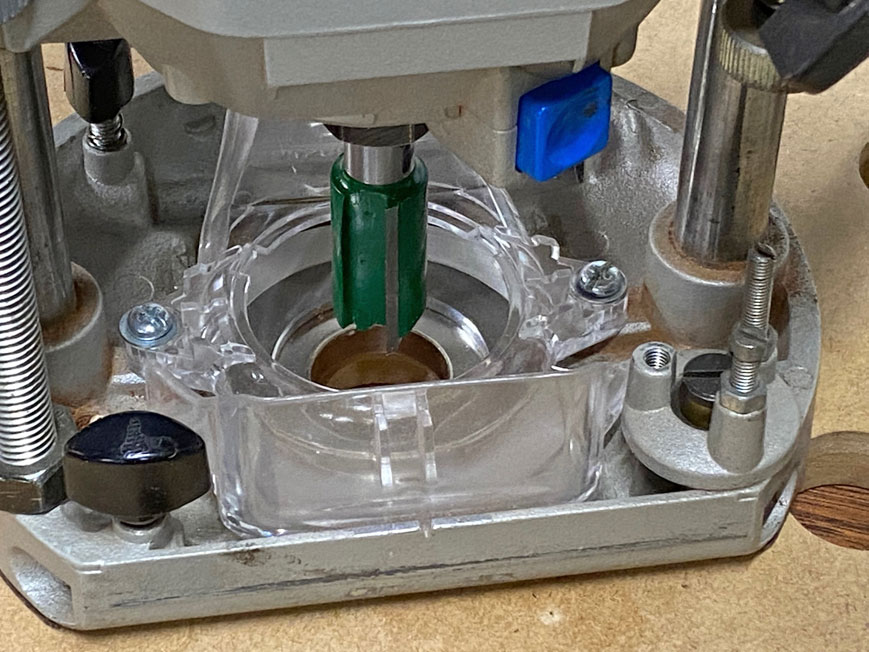
I was also very pleased to see how well the dust collection worked. The Elu did not come with dust collection - this was not important 25 years ago! - and I adapted the fitting from a Dewalt to fit it.
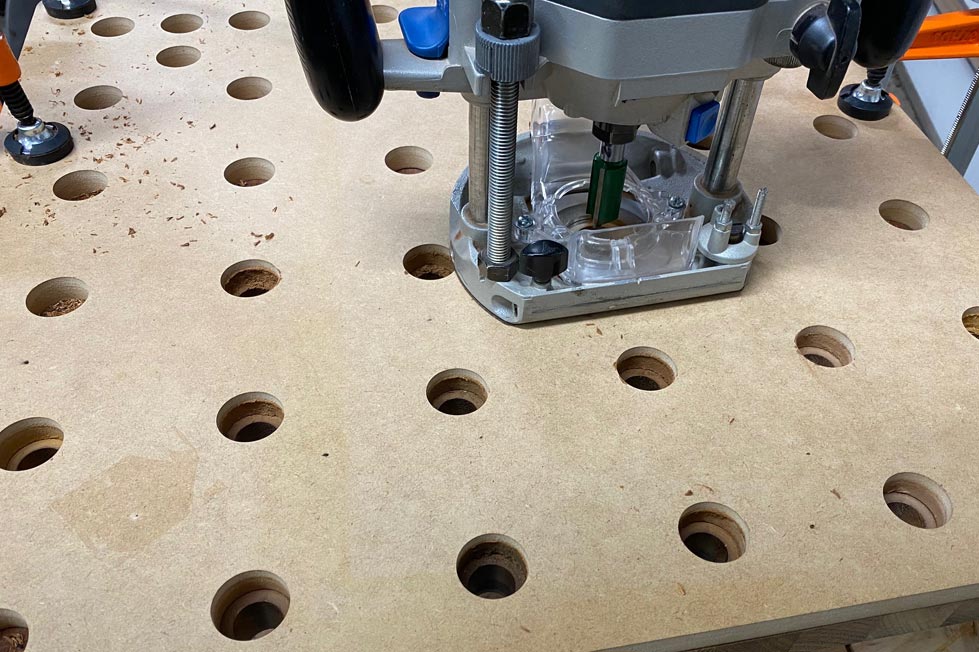
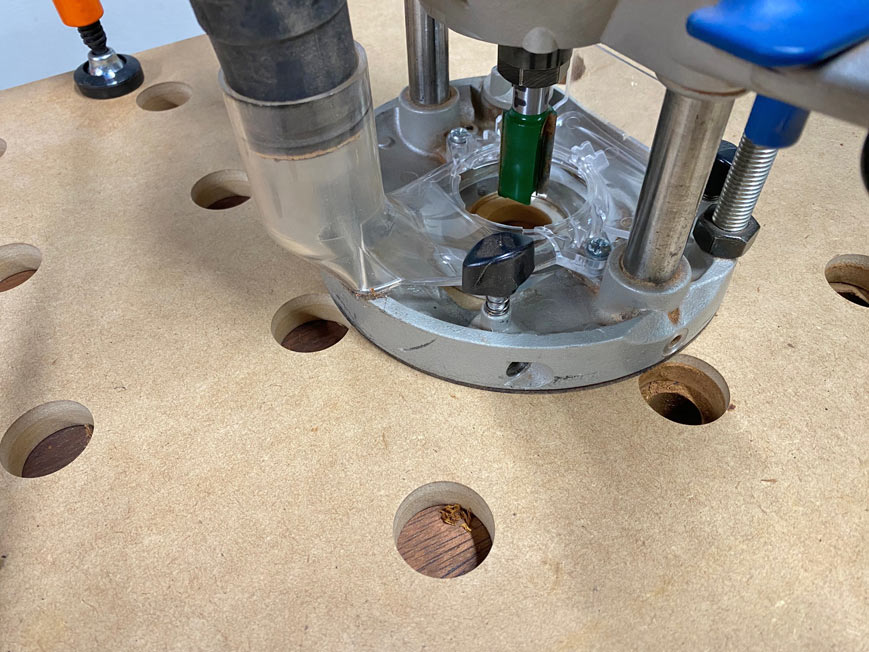
Once all the holes were routed ...
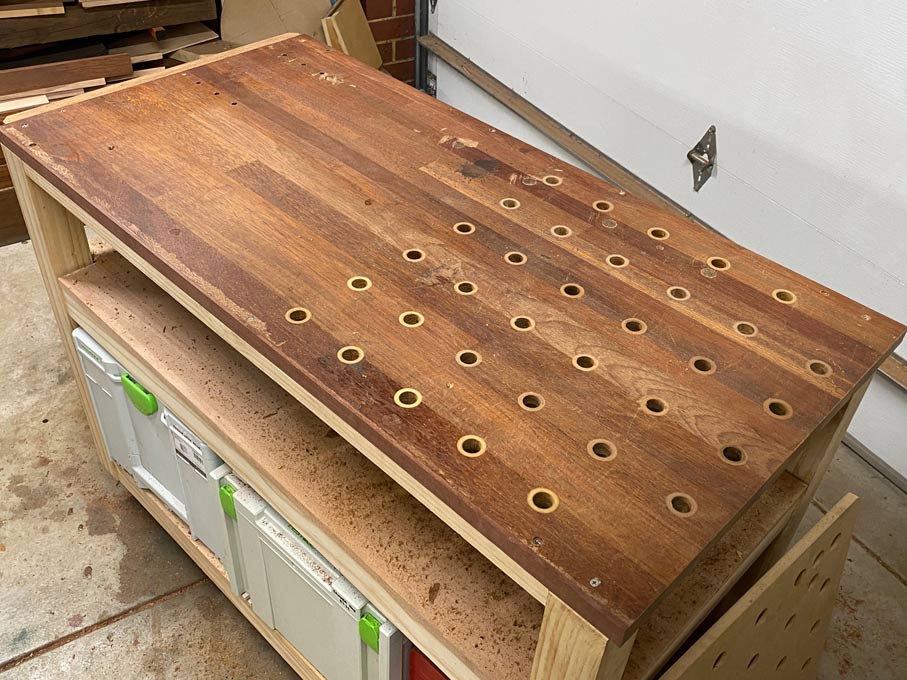
... the template needed to be moved to complete the bench top. This was facilitated by two dogs which my friend had thoughtfully made for this purpose ...
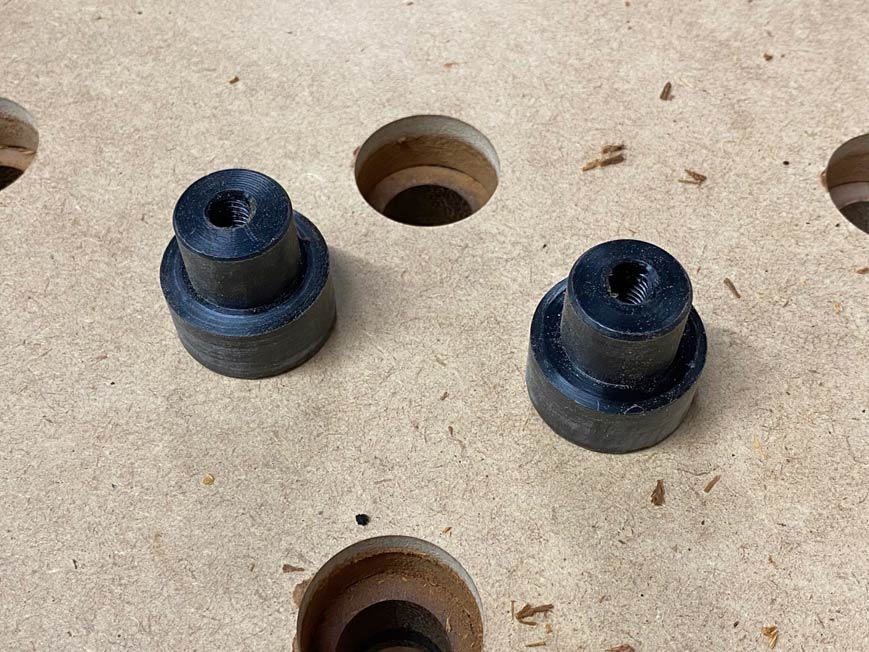
The dogs are fitted into the existing holes to align the pattern ...
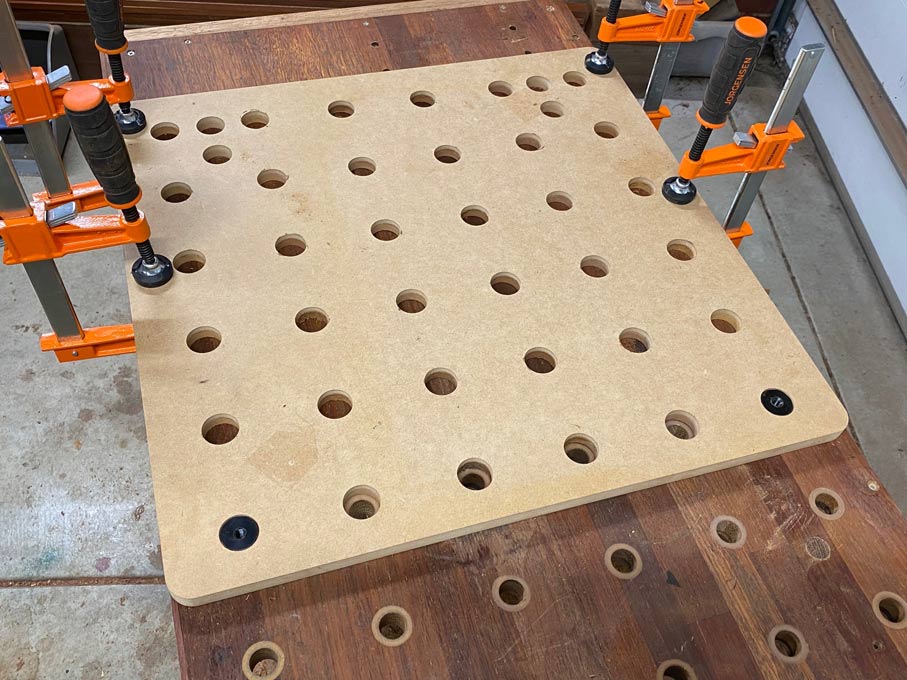
The remaining holes were drilled.
It only then occurred to me to check the bench top for flat - I should have done this earlier, although the top was flat when I first put it together. There was a 0.5mm gap at the centre, and I decided to plane it flat ...
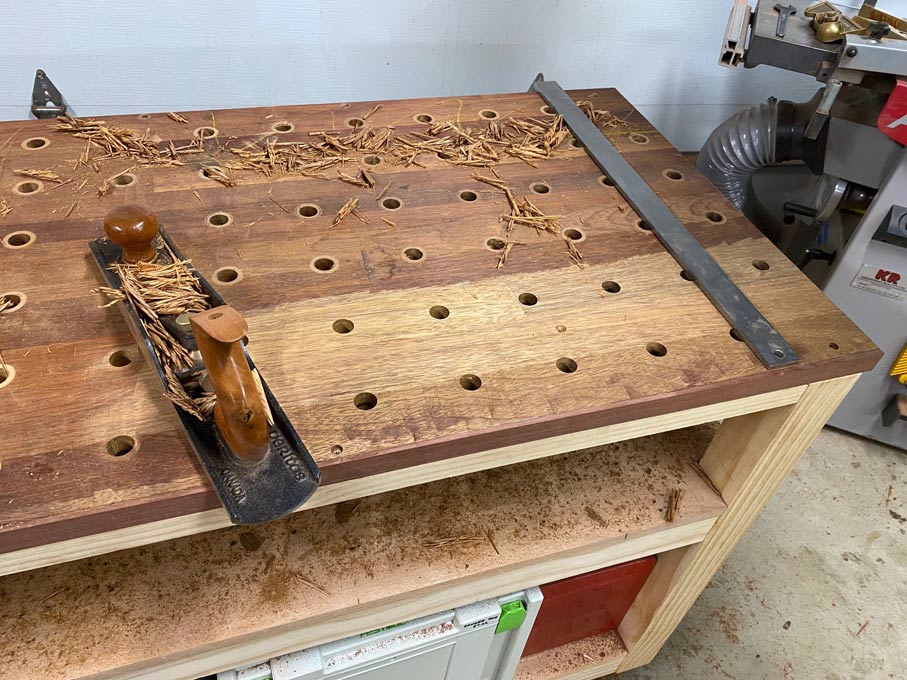
The top was then sanded(80 grit) ...
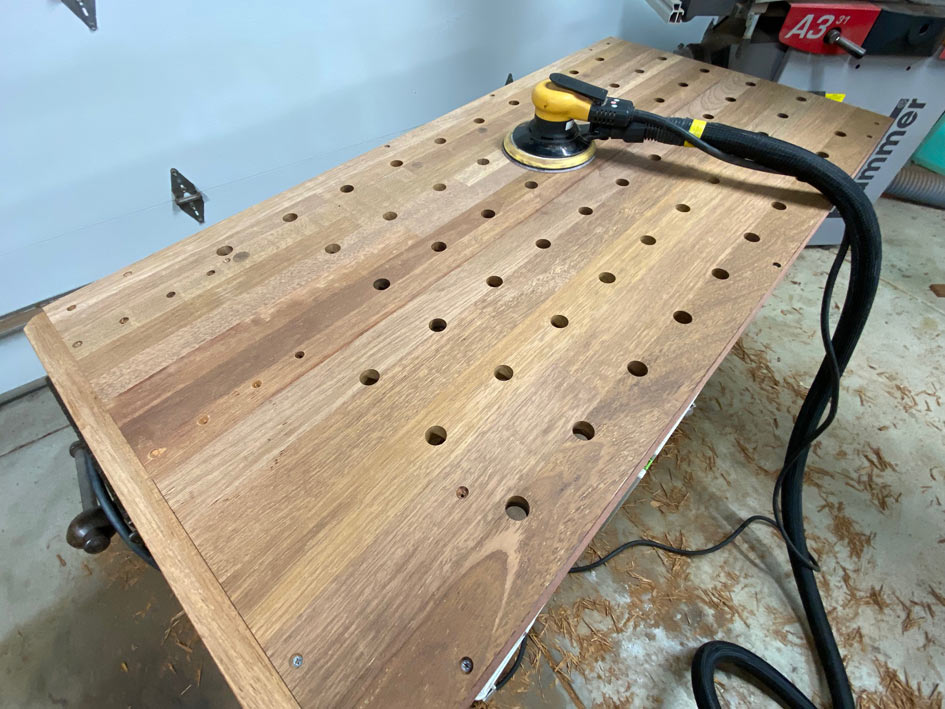
... all is flat ...
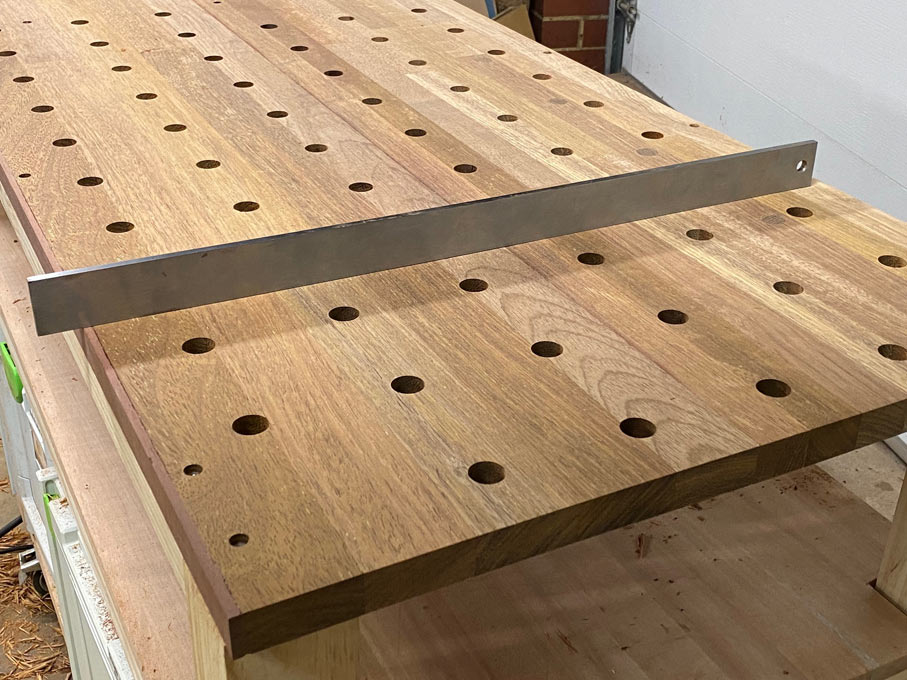
The holes received a fine chamfer ...
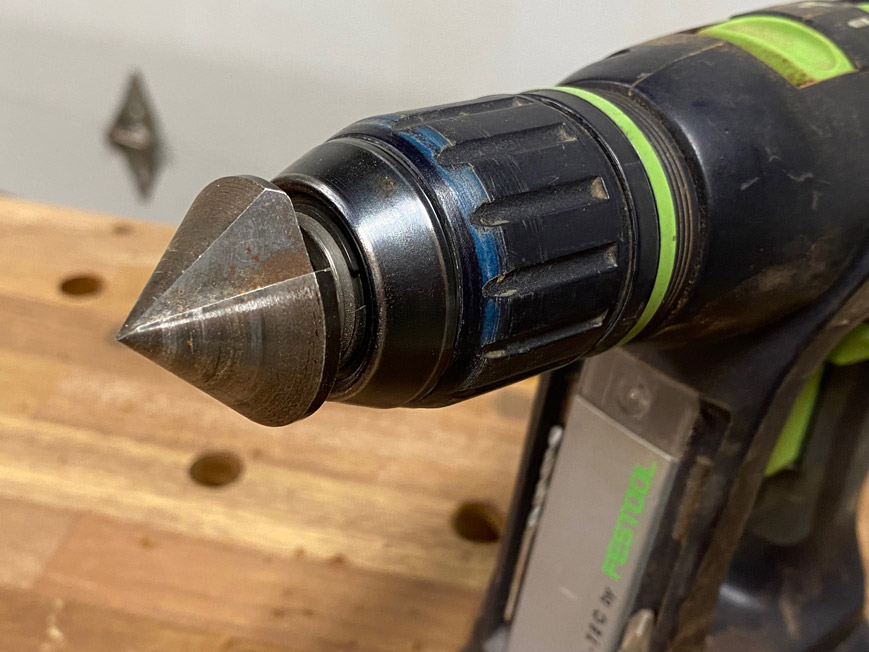
... and the right side was bevelled at 20 degrees.
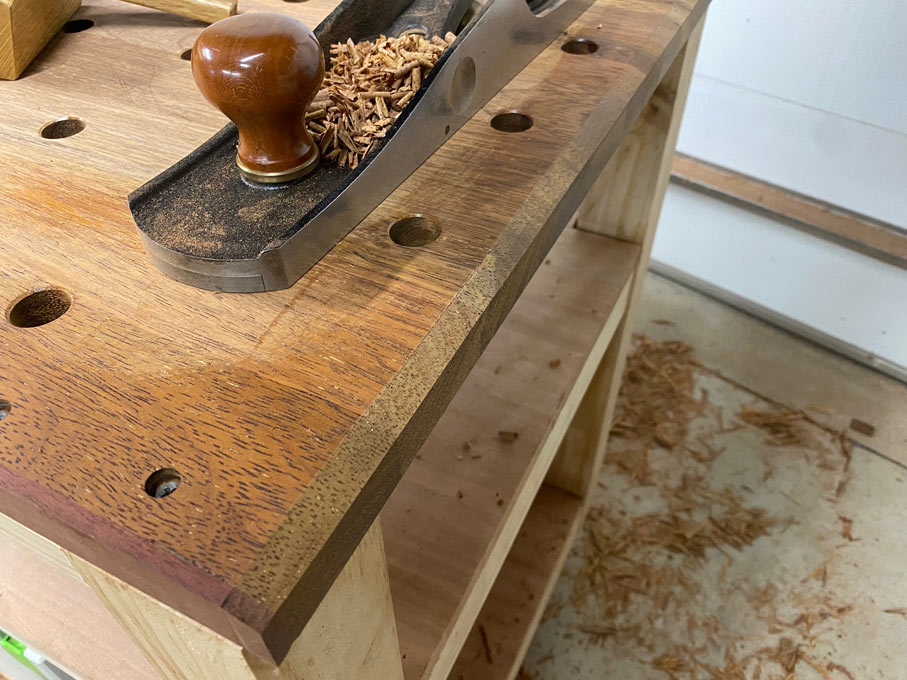
The reason for this is that the bench will also act as a outfeed for the jointer/thicknesser-planer and sliding tablesaw ...
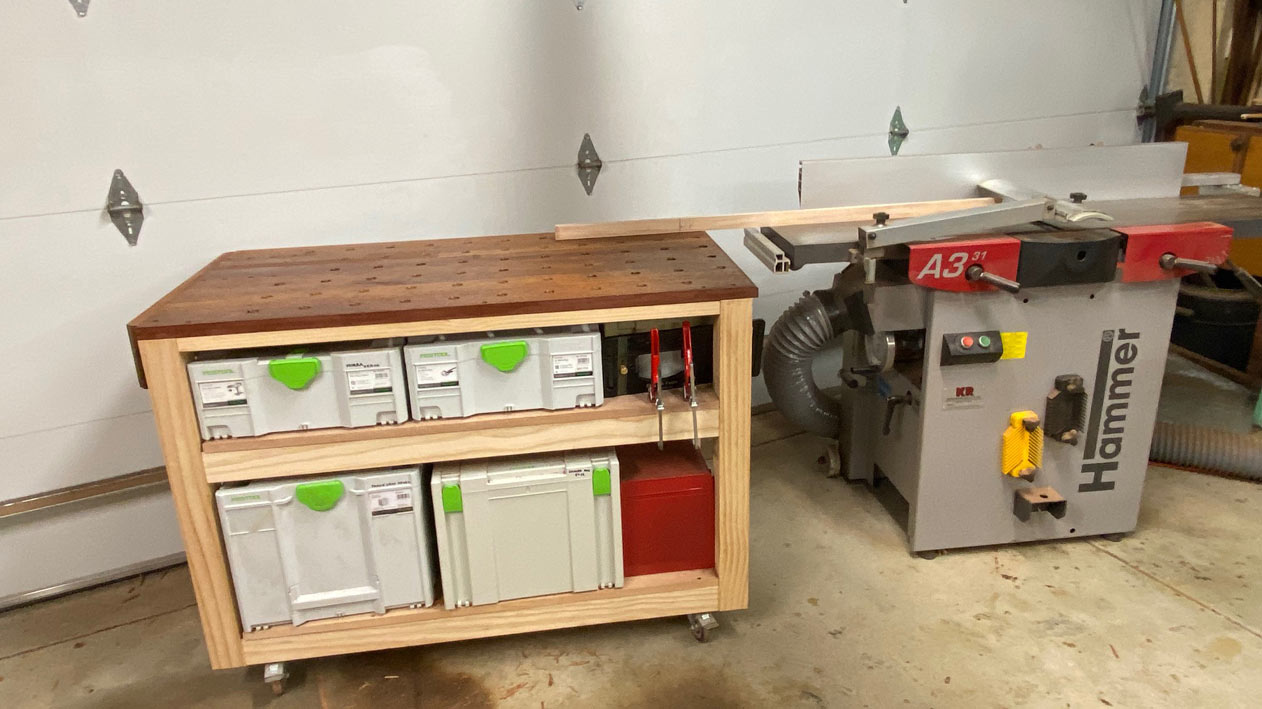
Finally, the top received a coat of flat poly to protect it during glue-ups ..
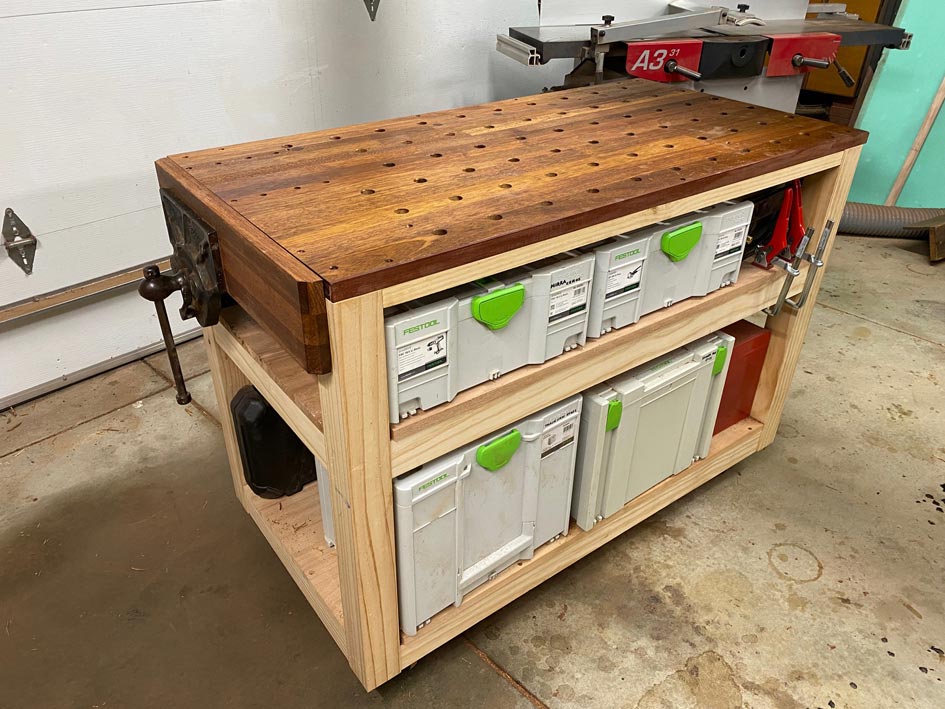
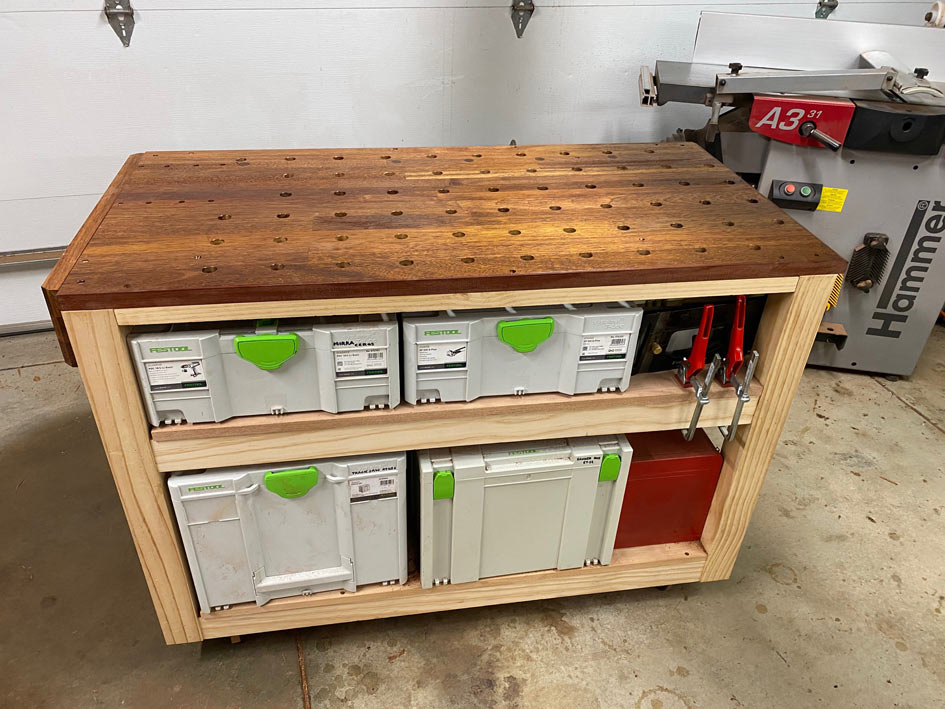
Thanks for watching. I will return once a fence is built, and show the various work-holding methods.
Regards from Perth
Derek