smorgasbord
Member
- Joined
- Jan 7, 2022
- Messages
- 1,280
Start at 5:52 if the link doesn't for you:
Exterior door out of cherry, rail and stile construction.
For the panel, they "glue" up some narrow boards. I put "glue" in quotes because they're claiming their secret is to not use glue, but a flexible silicone. Here's the quote while they're showing the construction:
"This allows the expansion and contraction of the wood pieces, but still maintains a waterproof seal. On a panel this large with a tongue and groove construction, you wouldn't want to physically glue these together because you need them to float so that this panel isn't going to expand so much that it begins to separate your stile and rail joinery."
I don't get this:
1) They are literally "gluing" the long tongues to the long grooves, yes with silicone, but it's not like the tongue doesn't reach all the way into the groove. As you can see in this screenshot after they cut the assembly to length, the cut-off stays together:
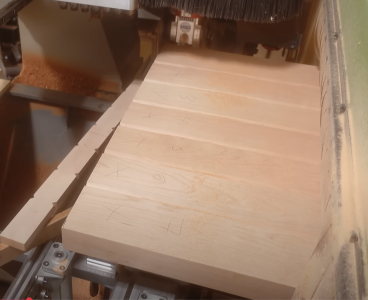
So, it's really just a glued up wide board.
2) Worse, they use Titebond III to not only glue up the rails and stiles, but also TO GLUE THE PANEL IN. Photo showing the glue along the long edge of the stile:
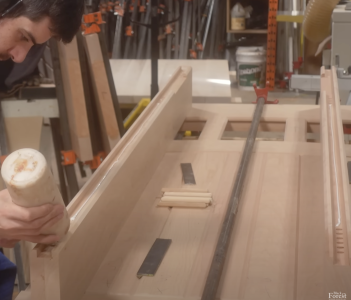
3) Worse yet(!), they cross-grain glue the panel in place:
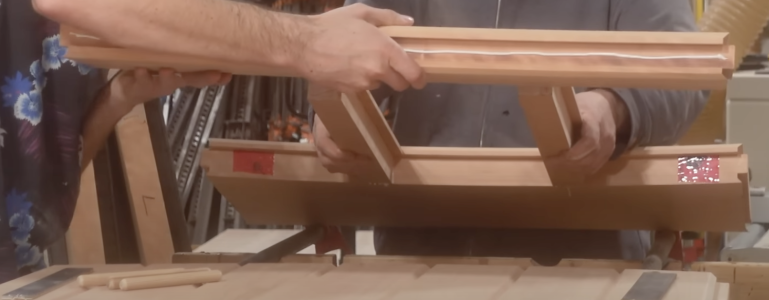
4) So, I'm thinking the idea is that while the edges of the panel is glued to the stiles, the inner pieces of the panel can shrink and still have that silicone hold.
5) BUT - what about if the panel expands? They don't talk about installing this during the wet time of year. And that cross-grain glue is a no-no no matter what.
So, either I'm missing something or this door may self-destruct like the door they're replacing, lol.
Note that I do agree with them on using oil-based finishes rather than polyurethane, even Spar Varnishes. There are no clear finishes that hold up for a long long time to the sun's UV rays, so you might as well go with something that's easier to maintain to avoid having to strip the door completely.
But, this door construction technique seems very wrong to me. I built my own front door 3 decades ago, and all the joinery on it is still tight as the day it was installed. Exterior finish is CPES and Sikkens, but I'm thinking of stripping the Sikkens next time and going with something else.
Exterior door out of cherry, rail and stile construction.
For the panel, they "glue" up some narrow boards. I put "glue" in quotes because they're claiming their secret is to not use glue, but a flexible silicone. Here's the quote while they're showing the construction:
"This allows the expansion and contraction of the wood pieces, but still maintains a waterproof seal. On a panel this large with a tongue and groove construction, you wouldn't want to physically glue these together because you need them to float so that this panel isn't going to expand so much that it begins to separate your stile and rail joinery."
I don't get this:
1) They are literally "gluing" the long tongues to the long grooves, yes with silicone, but it's not like the tongue doesn't reach all the way into the groove. As you can see in this screenshot after they cut the assembly to length, the cut-off stays together:
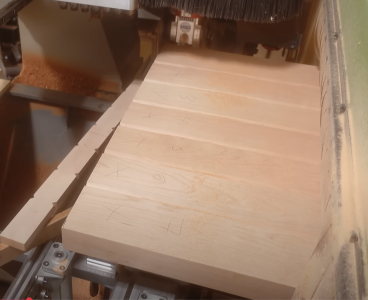
So, it's really just a glued up wide board.
2) Worse, they use Titebond III to not only glue up the rails and stiles, but also TO GLUE THE PANEL IN. Photo showing the glue along the long edge of the stile:
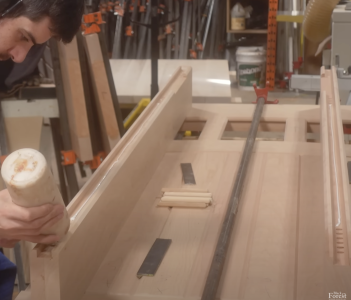
3) Worse yet(!), they cross-grain glue the panel in place:
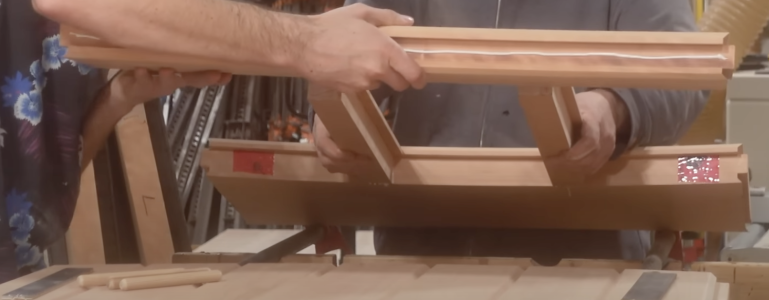
4) So, I'm thinking the idea is that while the edges of the panel is glued to the stiles, the inner pieces of the panel can shrink and still have that silicone hold.
5) BUT - what about if the panel expands? They don't talk about installing this during the wet time of year. And that cross-grain glue is a no-no no matter what.
So, either I'm missing something or this door may self-destruct like the door they're replacing, lol.
Note that I do agree with them on using oil-based finishes rather than polyurethane, even Spar Varnishes. There are no clear finishes that hold up for a long long time to the sun's UV rays, so you might as well go with something that's easier to maintain to avoid having to strip the door completely.
But, this door construction technique seems very wrong to me. I built my own front door 3 decades ago, and all the joinery on it is still tight as the day it was installed. Exterior finish is CPES and Sikkens, but I'm thinking of stripping the Sikkens next time and going with something else.