derekcohen
Member
- Joined
- Jun 22, 2008
- Messages
- 956
The first 9 chapters of this build are on my website (bottom of this Index Page:http://www.inthewoodshop.com/Furniture/index.html ). Read these for the full background to the build. This features a mitred case with a curved front, and two drawers. One is a main drawer with curved front and slipped bottom, and a smaller drawer at the rear.
The reason for the title is to emphasise that good woodworking is not about power or hand tools, but about using these together as harmoniously as one can.
A little catch-up:
The clean lines of these mitred cases ...
... comes from shooting all the mitres to achieve smooth surfaces ..
Parts for two cases ...
Moving ahead.
Drawers on their way to becoming bow-fronted ...
Here is the latest chapter: It's beginning to look like a nightstand!
The project ended last time with all the parts cut and shaped for the two bases ..
Square peg into a round hole? Not quite, but the square ends of the aprons must join flush with the round legs ...
The choice was either to cope the end face of the apron to match each leg, or to shape the leg to match the end of the apron. I decided on the latter as each leg had a taper and the ends of the aprons were angled at 3 degrees. Matching the legs seemed much simpler. Still, it would prove to be a fair amount of work.
Step 1 - mark out the recess:
Step 2 - chop out the waste with a chisel:
The fit is decent ...
Eight joints later, and the first stage of the first base is at glue-up stage ...
Tapers round legs splayed at 3 degrees ...
The matching rounded front can be seen here ...
Close up of joints ...
I couldn't resist a little mock-up (but lots still to do - not only that this is one of two) ...
Regards from Perth
Derek
The reason for the title is to emphasise that good woodworking is not about power or hand tools, but about using these together as harmoniously as one can.
A little catch-up:
The clean lines of these mitred cases ...

... comes from shooting all the mitres to achieve smooth surfaces ..

Parts for two cases ...


Moving ahead.
Drawers on their way to becoming bow-fronted ...





Here is the latest chapter: It's beginning to look like a nightstand!
The project ended last time with all the parts cut and shaped for the two bases ..
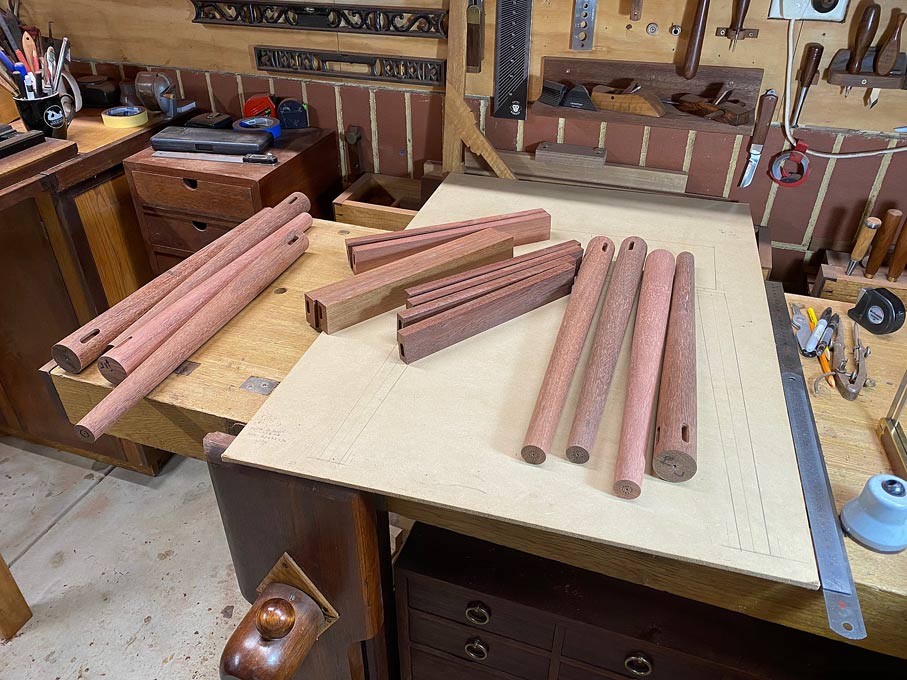
Square peg into a round hole? Not quite, but the square ends of the aprons must join flush with the round legs ...
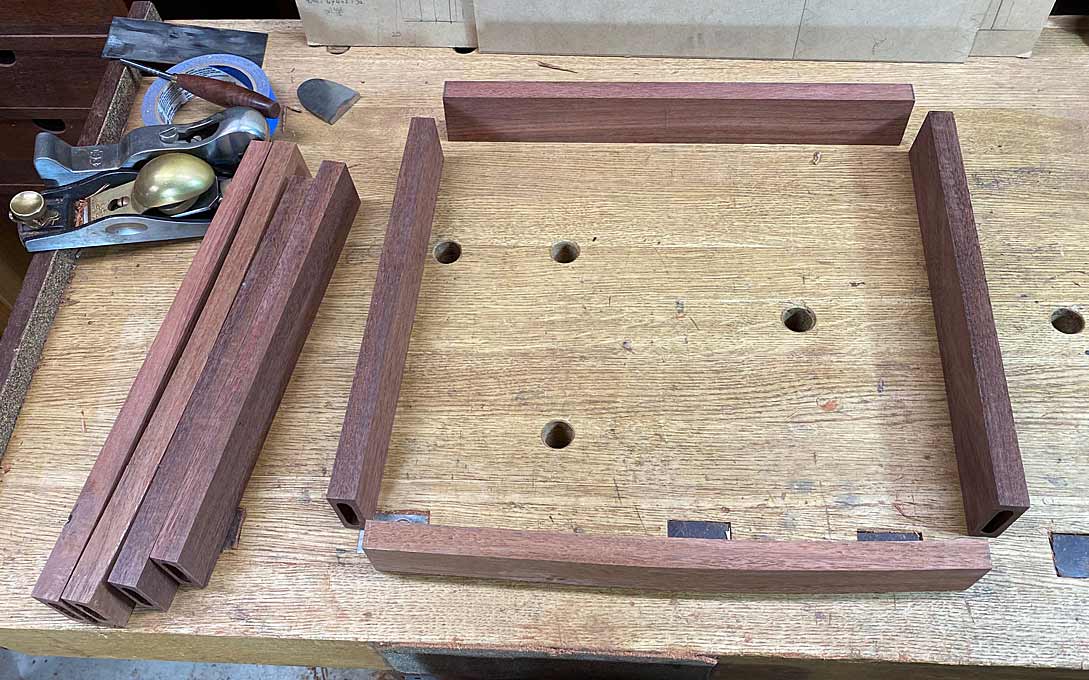
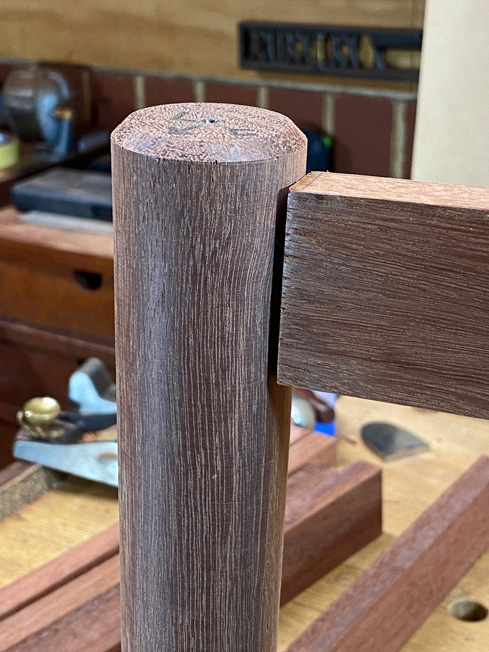
The choice was either to cope the end face of the apron to match each leg, or to shape the leg to match the end of the apron. I decided on the latter as each leg had a taper and the ends of the aprons were angled at 3 degrees. Matching the legs seemed much simpler. Still, it would prove to be a fair amount of work.
Step 1 - mark out the recess:
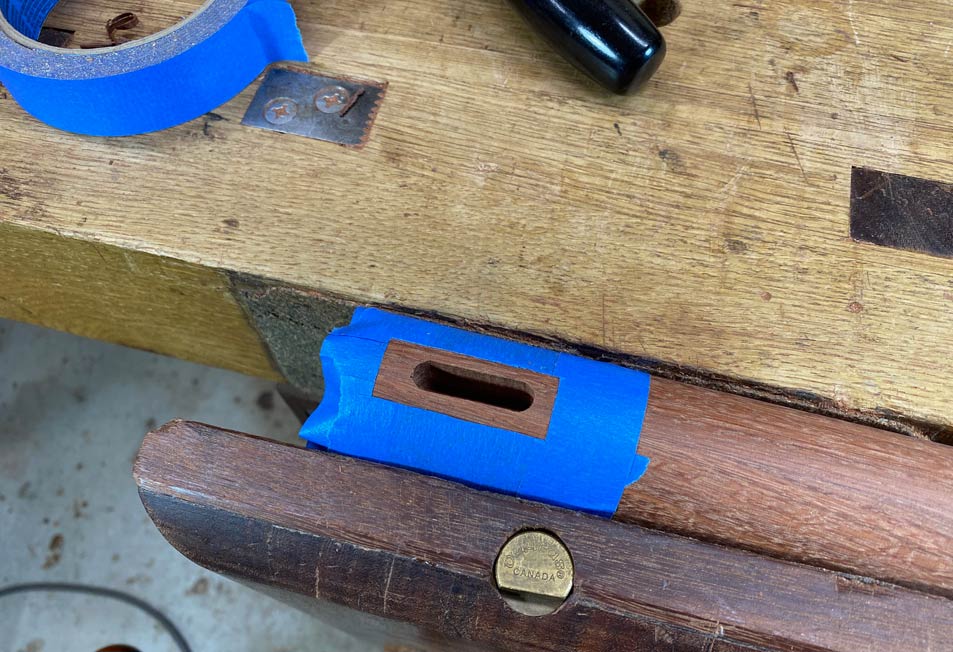
Step 2 - chop out the waste with a chisel:
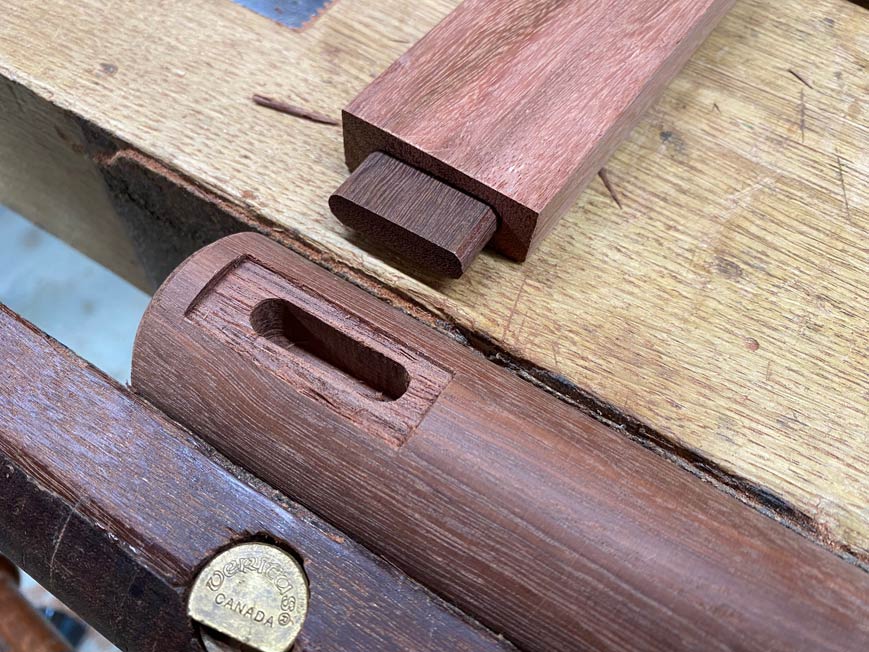
The fit is decent ...
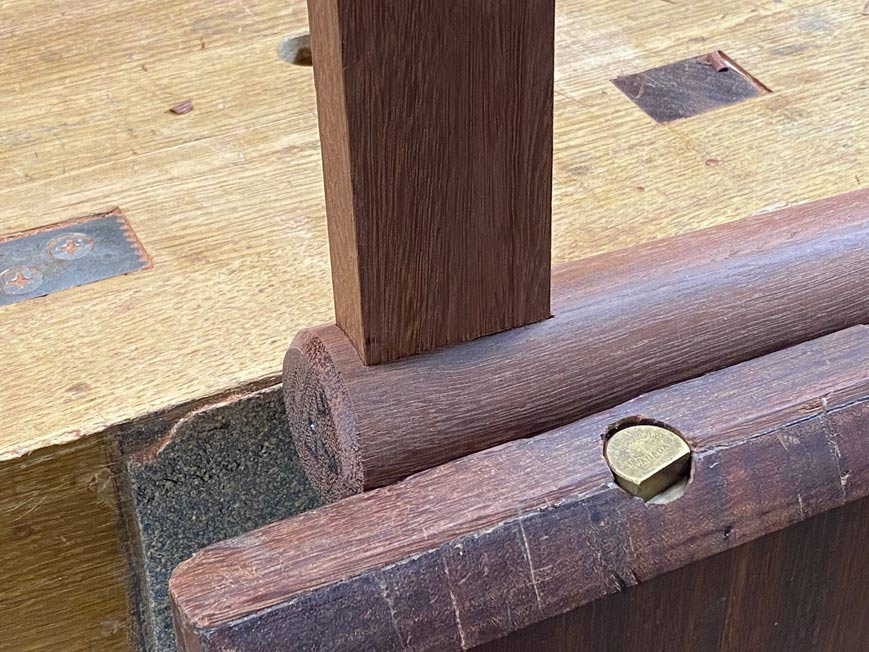
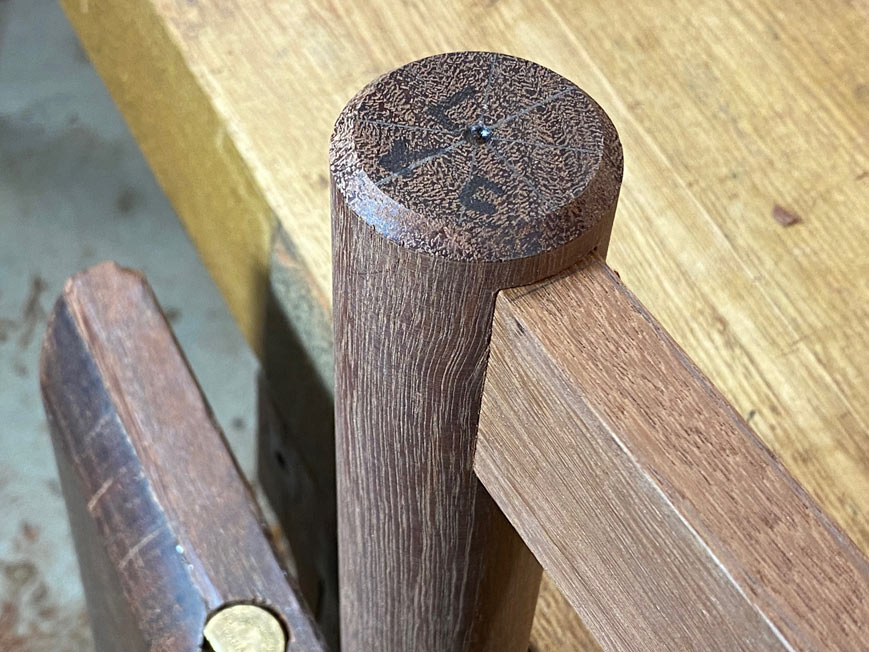
Eight joints later, and the first stage of the first base is at glue-up stage ...
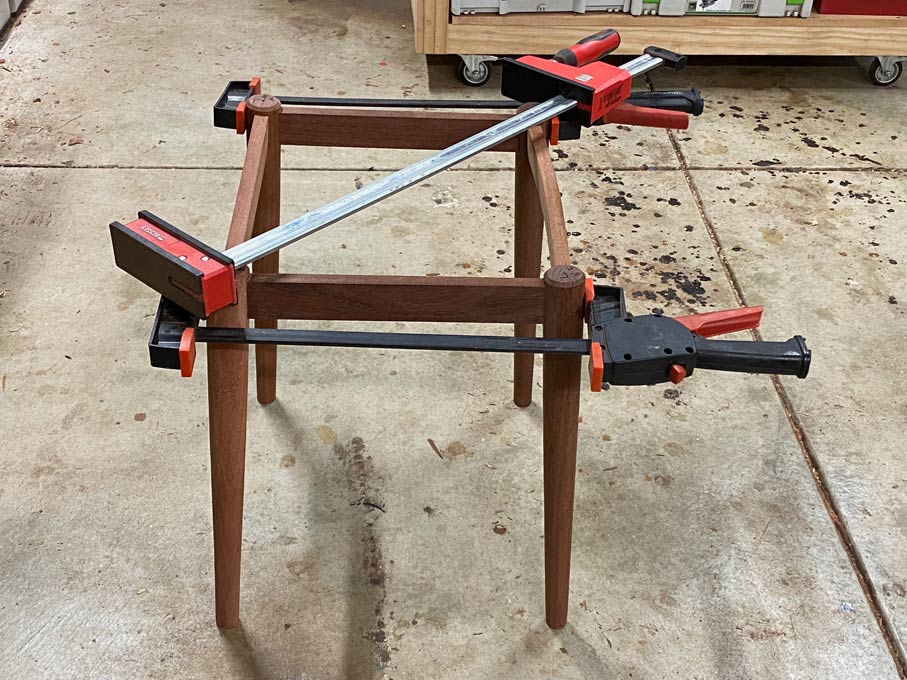
Tapers round legs splayed at 3 degrees ...
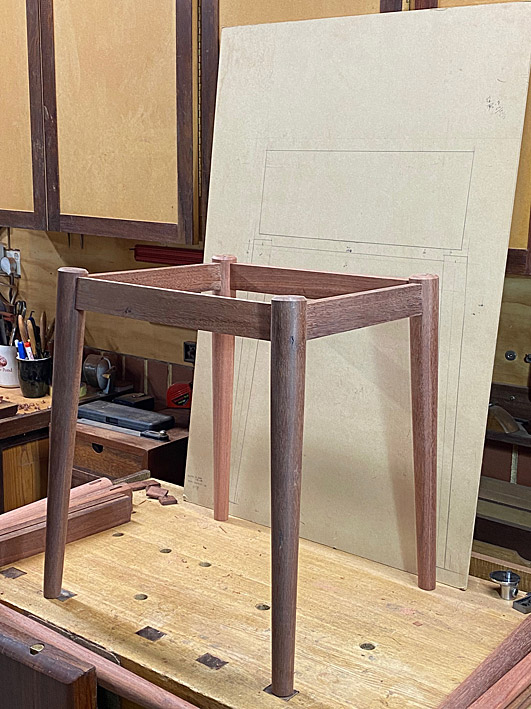
The matching rounded front can be seen here ...
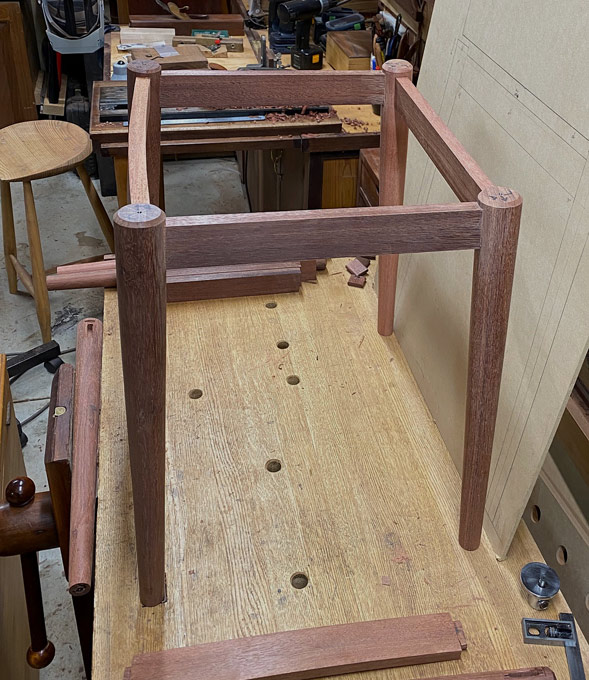
Close up of joints ...
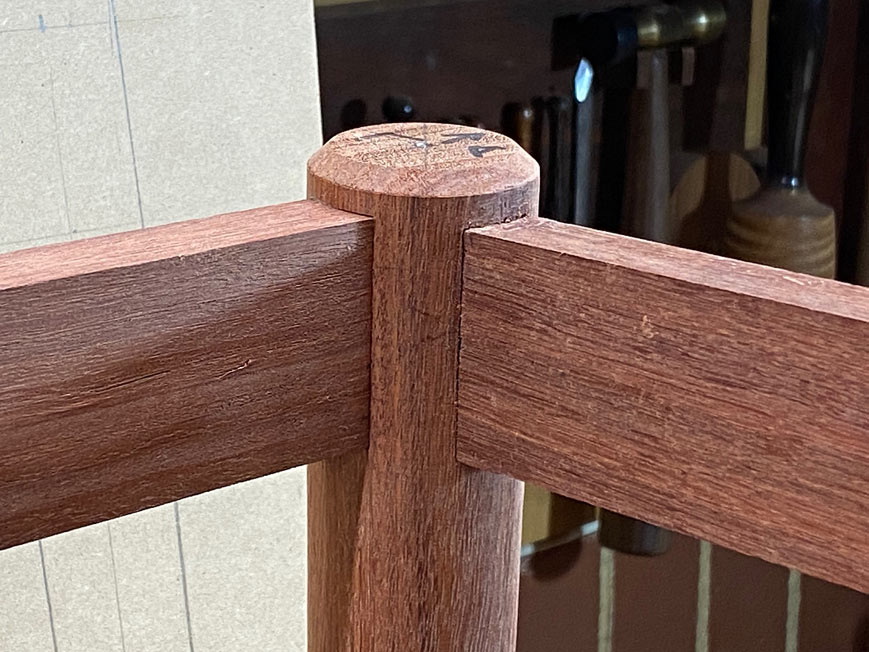
I couldn't resist a little mock-up (but lots still to do - not only that this is one of two) ...
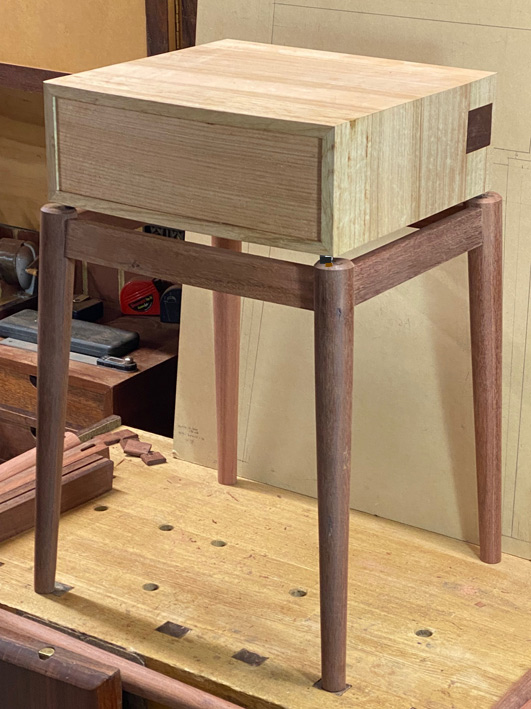
Regards from Perth
Derek